A team from Netherlands-based Brightlands Materials Center has developed self-sensing 3D printed composite parts through the use of integrated fibers. The unique self-sensing characteristic of the parts is expected to enable sophisticated critical structure monitoring in sectors such as construction and prosthetics in the future.
What is self-sensing?
Self-sensing is the ability of a material to act as a sensor and collect information about its own condition. Previously, polymer-matrix composites with infused continuous carbon fiber have been used as self-sensors, whereby changes in the electrical resistance of the fibers have been measured. Self-sensing materials, with enough fibers, would allow us to monitor the structural health of large parts in aerospace applications or even bridges.
The traditional production of self-sensing composite parts, however, is often a complex multi-step process and requires specialist apparatus to integrate the continuous fibers. The Brightlands team set out with the goal of manufacturing self-sensors using additive manufacturing, drawing on the strengths of two technologies for a more effective result.
3D printing continuous fibers
3D printing would allow for the precise positioning of carbon fibers within a composite part, with placements and orientations running along critical areas where they are needed. The fibers could also be grouped together in batches to provide more sensitive monitoring where required – all made possible by the geometric freedom of additive manufacturing.
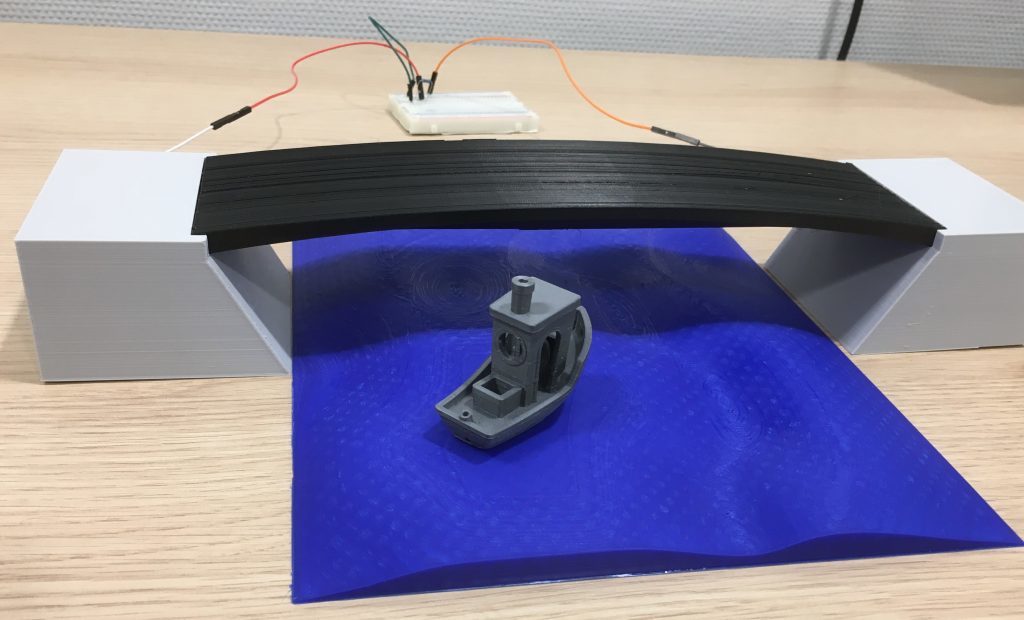
The Brightlands researchers conducted an experiment to validate their method of 3D printing sensor fibers by monitoring the deformation of a scale model pedestrian bridge. The bridge was simply a bending beam made of a thermoplastic polymer matrix infused with carbon fiber. It was printed with the Anisoprint Composer A4 composite 3D printer, which allows for fibers to periodically be inserted along the build direction via co-extrusion, resulting in – you guessed it – anisotropy. Electrical connections were made with a few of the fibers protruding out of the bridge and their resistances were measured with varying applied loads.
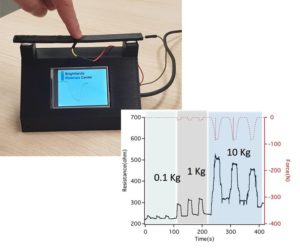
Future perspectives
The results showed a clear correlation between the applied load on the bridge and the electrical resistance of the continuous fibers, with resistance increasing as force increased. This validated the team’s 3D printing of continuous fiber infused composites for self-sensing applications.
They hope to scale the novel approach up to real use circumstances, where 3D printed self-sensing prototypes could provide useful data on what sections of a component bear the most load or what range of forces the component will need to withstand. Engineers can use this data to design prosthesis to more efficiently distribute stresses or build bridging structures to support greater loads.
Research partners
Brightlands Materials Center is an independent research center founded by the Netherlands Organisation for applied scientific research TNO (The Hague) and the province of Limburg. It supports innovation in industry with a strong application focus and offers dedicated contract research and participation, including a research roadmap on 3D printed self-sensing composites.
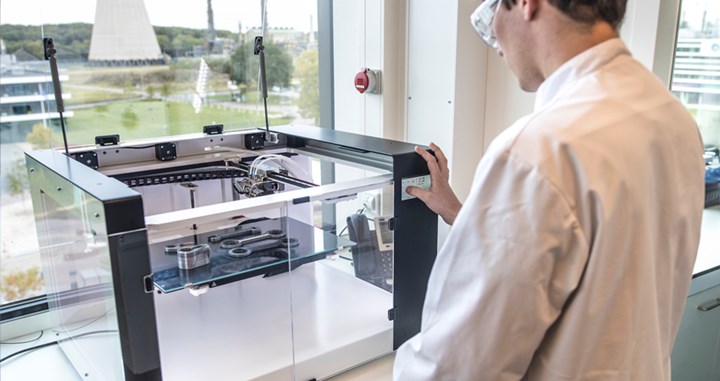
Anisoprint is an inventor of anisoprinting — the technology for design and production of optimal composite structures through continuous fiber 3D deposition. The company manufactures 3D printers, materials (based on carbon and basalt fibers) and software for producing anisoprinted composite parts to help scientists solve research problems in new, more effective ways and to enable manufacturing companies to reduce their costs.
Photos via BMC.