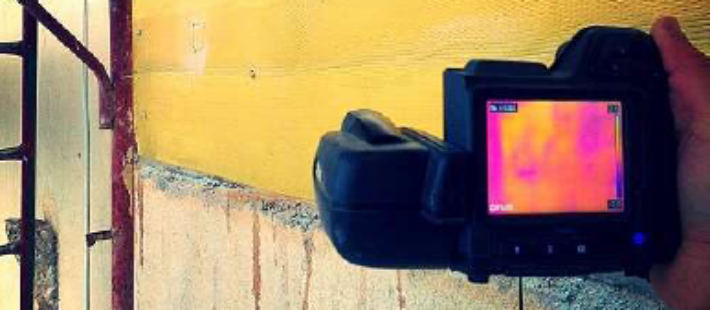
L’illuminazione naturale è da sempre una risorsa nella progettazione architettonica. Già ai tempi dei romani si costruivano chiese e abitazioni con lucernari vetrati. Oggi, grazie all’evoluzione tecnologica, architetti e ingegneri possono scegliere tra diverse soluzioni in grado di combinare illuminazione solare, comfort termico e facilità di installazione. Una di queste è la cupola, che, avendo una struttura simile a quella dei lucernari, favorisce il passaggio della luce verso l’interno dell’edificio…
In occasione dell’evento JEC Forum ITALY – organizzato da JEC Group in collaborazione con Assocompositi – del prossimo 6-7 giugno 2023 a Bologna, Prof. Luigi Ascione terrà un intervento all’interno della sessione “Applicazioni dei compositi nel costruito”. Disponibile ora l’abstract dello speech!…
L’energia eolica è una delle risorse di energia rinnovabile più utilizzate. Le pale delle turbine eoliche, tuttavia, essendo realizzate in resina rinforzata con fibre di vetro o carbonio, sono difficili da riciclare a fine vita e spesso vengono smaltite in discarica. Per risolvere il problema, un’azienda italiana, esperta nella produzione di componenti edilizi prefabbricati, e una polacca, specializzata nel riciclo di rifiuti, hanno collaborato allo sviluppo di un procedimento di recupero degli scarti di vetroresina delle pale eoliche che vengono poi incorporati in miscele di cemento per dare vita ad un blocco da costruzione ecosostenibile. …
Il rilevante intervento di restauro conservativo dell’ex Mercato ortofrutticolo generale di Genova ha permesso di mantenere l’integrità materica delle superfici e l’unitarietà del complesso, riportando allo stato di efficienza i diversi edifici. I progettisti che si sono occupati dei lavori hanno potuto contare sulla collaborazione di Kerakoll che ha fornito loro la propria di linea di sistemi di ripristino e rinforzo Geolite, GeoCalce e Geosteel…