Designing equipment to protect limbs against the extreme temperatures and deadly projectiles that accompany an explosion during wars has been difficult because of a fundamental property of materials. Materials that are strong enough to protect against ballistic threats can’t protect against extreme temperatures, and vice versa. As a result, much of today’s protective equipment is composed of multiple layers of different materials, leading to bulky, heavy gear that, if worn on the arms and legs, would severely limit a soldier’s mobility.
Now, researchers at Harvard University, in collaboration with the US Army Combat Capabilities Development Command Soldier Center (CCDC SC) and West Point, have developed a lightweight, multifunctional nanofiber material that can protect wearers from both extreme temperatures and ballistic threats. The researchers report this new material in a paper in Matter.
“Our goal was to design a multifunctional material that could protect someone working in an extreme environment, such as an astronaut, firefighter or soldier, from the many different threats they face,” said Grant Gonzalez, a postdoctoral fellow at Harvard SEAS and first author of the paper.
To achieve this practical goal, the researchers needed to explore the trade-off between mechanical protection and thermal insulation, properties rooted in a material’s molecular structure and orientation.
Materials that provide strong mechanical protection, such as metals and ceramics, have a highly ordered and aligned molecular structure. This structure allows them to withstand and distribute the energy of a direct blow. Insulating materials, on the other hand, have a much less ordered structure, which prevents the transmission of heat through the material.
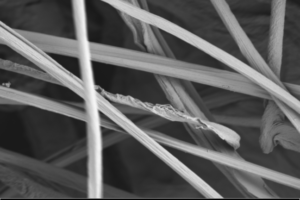
Kevlar and Twaron are commercial products used extensively in protective equipment, and can provide either ballistic or thermal protection, depending on how they are manufactured. Woven Kevlar, for example, has a highly aligned crystalline structure and is used in protective bulletproof vests. Porous Kevlar aerogels, on the other hand, have been shown to have high thermal insulation.
“Our idea was to use this Kevlar polymer to combine the woven, ordered structure of fibers with the porosity of aerogels to make long, continuous fibers with porous spacing in between,” said Gonzalez. “In this system, the long fibers could resist a mechanical impact while the pores would limit heat diffusion.”
The research team used immersion Rotary Jet-Spinning (iRJS), a technique developed by Parker’s Disease Biophysics Group, to manufacture the fibers. In this technique, a liquid polymer solution is loaded into a reservoir and then pushed out through a tiny opening by centrifugal force as the device spins.
When the polymer solution shoots out of the reservoir, it first passes through an area of open air, where the polymers elongate and the chains align. Then the solution hits a liquid bath that removes the solvent and precipitates the polymers to form solid fibers. Since the bath is also spinning – like water in a salad spinner – the nanofibers follow the stream of the vortex and wrap around a rotating collector at the base of the device.
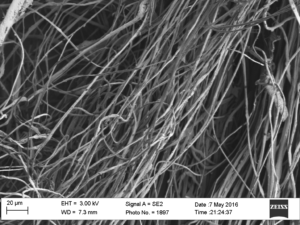
By tuning the viscosity of the liquid polymer solution, the researchers were able to spin long, aligned nanofibers into porous sheets – providing enough order to protect against projectiles but enough disorder to protect against heat. In about 10 minutes, the team could spin sheets about 10cm by 30cm in size.
To test the sheets, the Harvard team turned to their collaborators to perform ballistic tests. Researchers at CCDC SC simulated shrapnel impact by shooting large, BB-like projectiles at the sample, sandwiching the nanofiber sheets between sheets of woven Twaron. They observed little difference in protection between a stack of all woven Twaron sheets and a combined stack of woven Twaron and spun nanofibers. But in testing for thermal protection, the researchers found that the nanofibers provided 20 times the heat insulation capability of commercial Twaron and Kevlar.
“The capabilities of the CCDC SC allow us to quantify the successes of our fibers from the perspective of protective equipment for warfighters, specifically,” said Gonzalez. “While there are improvements that could be made, we have pushed the boundaries of what’s possible and started moving the field towards this kind of multifunctional material.”
Harvard’s Office of Technology Development has filed a patent application for the technology and is actively seeking commercialization opportunities.
Source: Materials Today