9T Labs introduces its digital composite manufacturing solution for series production
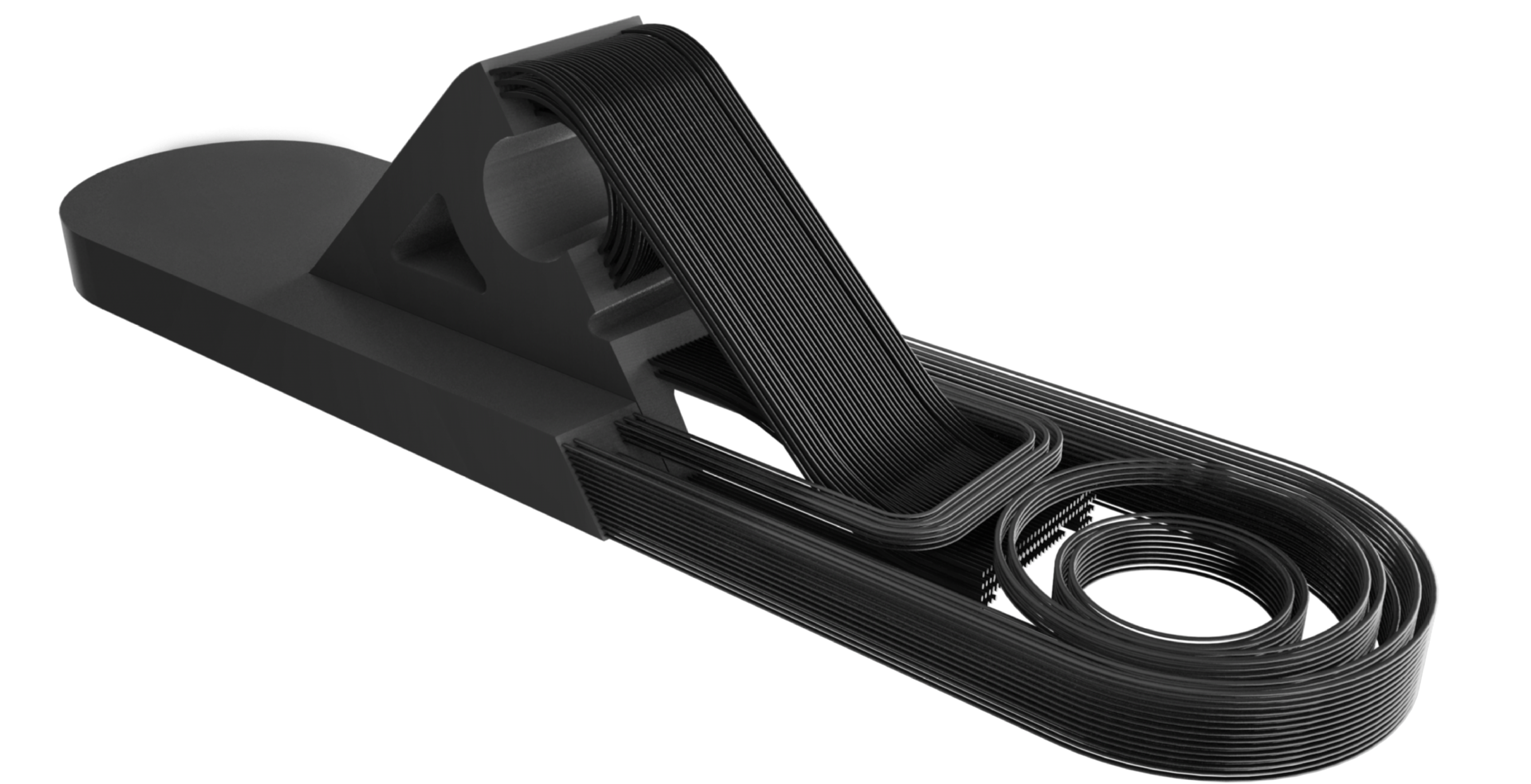
What does it take to make load carrying fiber composite structures more accessible?
High performance composites possess excellent mechanical and chemical characteristics, making them applicable for various industries such as aerospace, automotive, medtech and leisure. Remouldability and high fracture toughness of thermoplastic based matrix systems led to new applications with short cycle times in production and high damage tolerance. However, the comparably high costs associated with carbon fiber (CF) composite parts to its aluminium or steel contenders, remain a constraining factor.
Clearly, a higher degree of freedom to optimize the part geometry and the fiber layup in combination with increased automation in manufacturing will reduce the current constraint.
Toward a game-changing solution for composite
When screening the process landscape additive manufacturing shows the highest potential to deliver on those demands for manufacturing.
9T Labs, an ETH Zurich spin-off, aims to lower complexity and costs by including advanced software technologies, innovative production machinery equipment, and industry-standard material with the goal to meet the expected industrial standards while lowering both complexity and costs.
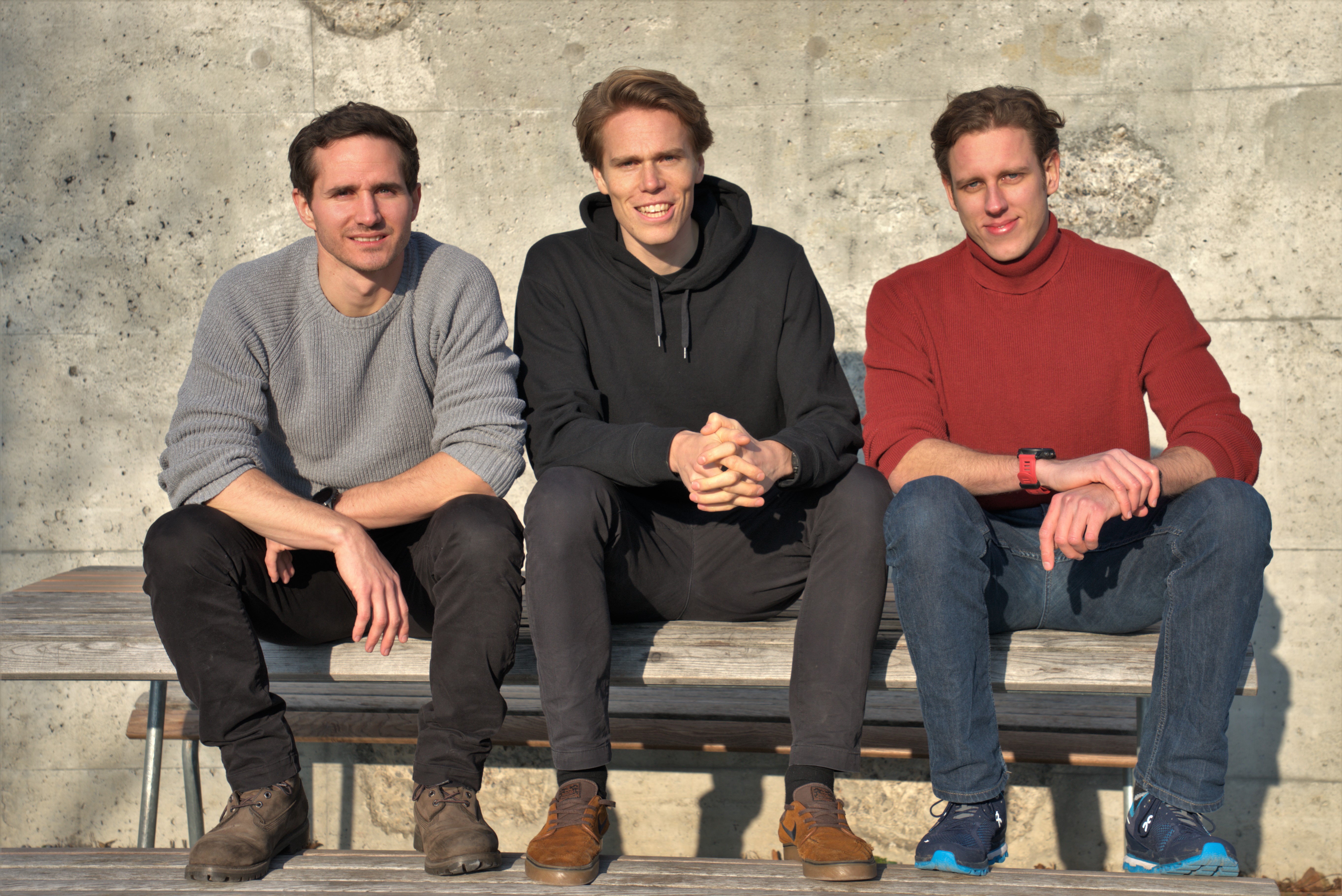
From left to right: Martin Eichenhofer, Chester Houwink, Giovanni Cavolina
Industry-standard Materials – Toward true anisotropy
Nowadays, the production of many composite parts starts with a technical textile having a constant fiber-volume content. In this case, the full freedom in designing a part based on the expected load cases is already very limited from the very beginning of the value-chain. In fact, this results in less than average material-efficiency in many applications with associated negative impacts on both environmental footprint and cost structure.
Wouldn’t it be valuable to place fibers only exactly where needed?
Currently, 9T Labs focuses on two polymers, PA12 and PEKK. To ensure the highest consistency of the continuous fiber material, they supply CF/PA12 and CF/PEKK filaments that are used to build the part.
While the material is key for the processability and the end function of the parts, the software component of the whole value chain plays a crucial role to enable the optimal part design.
Quickly and reliably manufacture the most optimal designs

Hinge with optimal fiber layup in fibrify Design Suite based on the simulation in Ansys ACP.
The most lightweight part can be reached by optimal fiber layup.
Today, 9T Labs is able to quickly define optimal fiber designs through integrated FEA simulation tools.
Firstly, fibrify™ Design Suite – the design engineer’s toolkit – enables variable fiber angles and designs that comprise plastic regions exempt from fiber reinforcements to bring new designs to life. It features an intuitive manual workflow that gives the user full control over fiber placement throughout the part. In addition, intelligent fiber lay-up proposals are made based on user inputs to accelerate the design process.
Secondly, the design output, together with application specific data, are fed into Ansys’ Composite PrepPost (ACP), a FEA simulation software. There, designs can be structurally validated before being produced. This enables a quick iterative design process (digital prototyping) that results in an optimized design within minutes.
Last but not least, fibrify™ Production enables users to connect to 9T Labs’ equipment, start production and monitor the process.
Produce industry grade serial parts
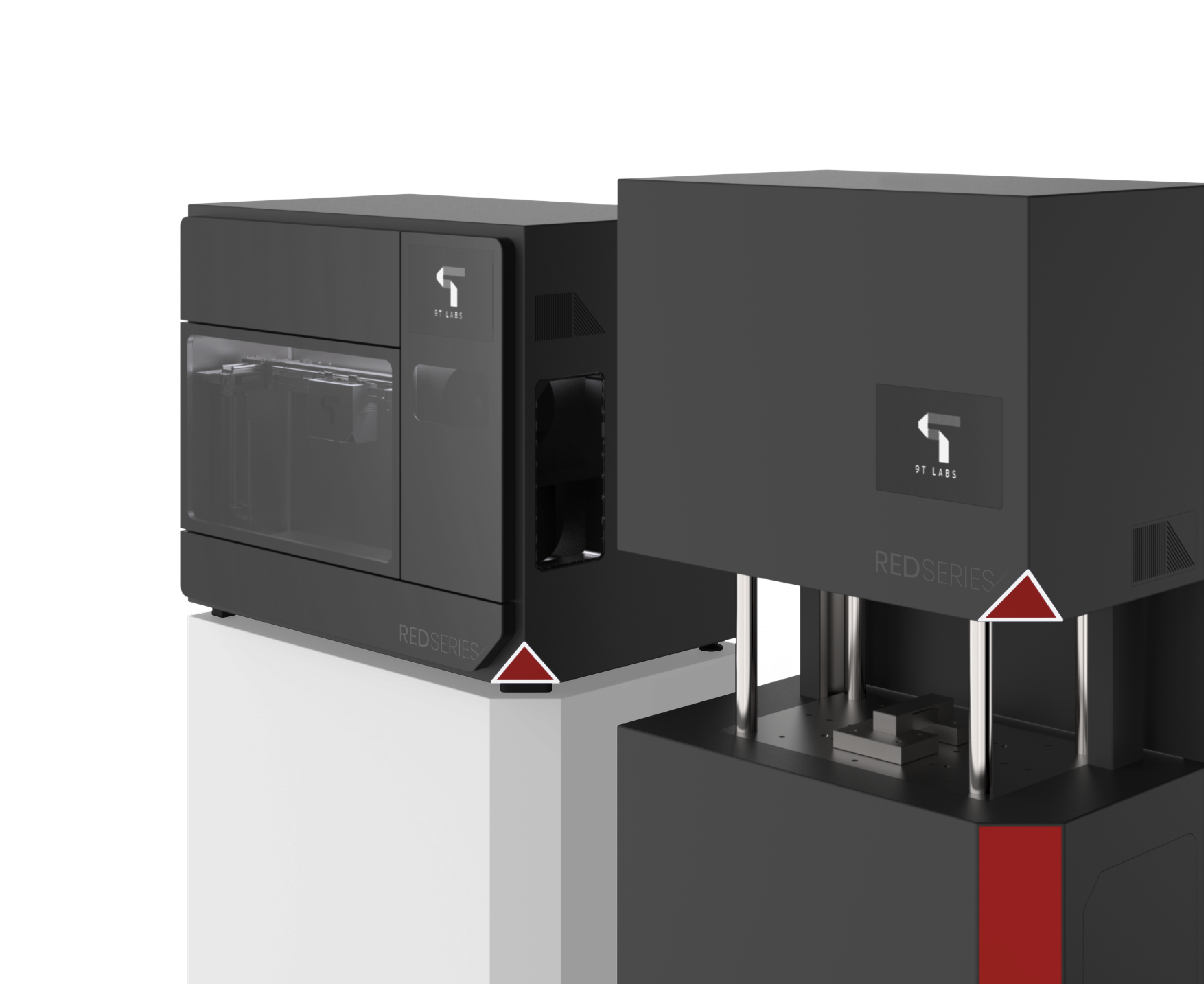
9T Labs hardware lineup: Build module and fusion module
Additive manufacturing shows a high potential when it comes to design flexibility. As 9T Labs is looking at continuous fiber reinforced structures, technologies based on filaments – especially FDM/FFF – are in scope. 9T Labs’ build module includes a proprietary depositioning head with a neat plastic filament extruder and a CF/plastic depositioning mechanism.
For proper consolidation, the parts are post-processed by applying pressure and temperature in the fusion module. This is especially attractive when working with thermoplastic materials.
In fact, this 2-stage process ensures part quality, reproducibility and cost competitiveness for series production applications. Last but not least, it allows welding multiple parts together, thus enabling true 3D fiber orientation in the final consolidated part.
Red Series is your vehicle to maximize the speed from idea to serial part production.
Would you like to challenge 9T Labs’ technology with your applications?
Get your part design and cost structure validated in a feasibility study.