La possibilità di ottenere materiali leggeri che incrementino il risparmio di carburante è uno dei principali vantaggi alla base del crescente impiego dei materiali compositi nella realizzazione di auto e veicoli. Se il loro utilizzo è ormai una prassi affermata per ciò che riguarda le vetture sportive o di fascia alta, negli ultimi anni la tendenza è ricorrere a questi materiali anche nella produzione di veicoli di serie. Ma la spinta all’innovazione non si ferma qui: l’ultima tendenza in atto consiste, infatti, nell’impiego di compositi a base naturale per rendere le vetture sempre più amiche dell’ambiente, non solo per quanto riguarda i bassi consumi di carburante, ma già a partire dalle materie prime utilizzate.
Con questo obiettivo è nato il progetto europeo Naturtruck, che si propone di sviluppare componenti per l’industria dei veicoli commerciali realizzati con compositi termoplastici a base di materie prime rinnovabili. Tali biocompositi verranno utilizzati per costruire parti degli interni in sostituzione del materiale oggi prevalentemente utilizzato in queste applicazioni, l’ABS, e dovranno quindi soddisfare gli alti standard di sicurezza ed estetici richiesti dal settore, presentando pertanto migliori proprietà termiche, di resistenza alla propagazione della fiamma e un’alta qualità della finitura superficiale. Il tutto, ovviamente, a un costo competitivo.
Il progetto, della durata di 32 mesi, è portato avanti da un consorzio che riunisce partner da tutta Europa, guidato dal centro di ricerca spagnolo Aimplast, e vede la collaborazione di Total che ha fornito al consorzio europeo uno dei materiali base: l’acido polilattico (PLA). È questo un biopolimero, ottenuto a partire dalla macinazione del mais, tra i primi a entrare nel mercato ed essere commercializzato su vasta scala, in virtù delle eccellenti proprietà fisiche e meccaniche che, almeno per alcune applicazioni, lo rendono uno dei migliori sostituti di termoplastici da fonte petrolchimica. Inizialmente utilizzato nel settore biomedicale, con la produzione di fili di sutura, il suo impiego si è infatti gradualmente esteso ad altri comparti, anche se la stragrande maggioranza dei consumi riguarda il settore packaging.
Nello specifico, il progetto prevede di mettere a punto nuovi biocompositi a partire da PLA appositamente modificato e fibre naturali per produrre parti delle cabine di autocarri, e parallelamente di sviluppare i processi produttivi e di trasformazione necessari per la loro applicazione a livello industriale. In tal modo, oltre ad ottenere ulteriori vantaggi in termini di riduzione di peso e di consumi, si facilita l’intera gestione dei componenti, che una volta giunti al termine della loro vita utile non verranno conferiti in discarica, ma potranno essere smaltiti come gli altri rifiuti di natura organica o riutilizzati come fertilizzanti nell’agricoltura.
La presenza di bioplastiche nel settore automobilistico è attualmente abbastanza scarsa, sebbene questo rappresenti il nuovo trend del comparto, e limitata per lo più alla produzione di pannelli per interni, dove rinforzi come la fibra di vetro sono stati sostituiti da altri rinforzi a base di fibre naturali. Con il progetto Naturtruck, dunque, l’obiettivo diventa molto più ambizioso, in quanto si prevede di sostituire la maggior parte dei materiali normalmente utilizzati negli interior con materiali di origine naturale e rinnovabili per oltre l’80% delle applicazioni.
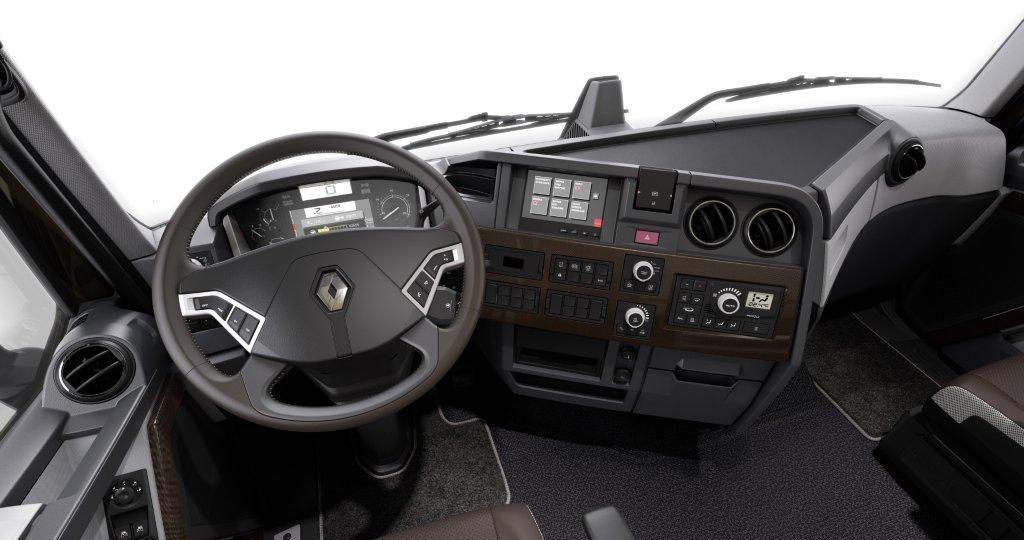