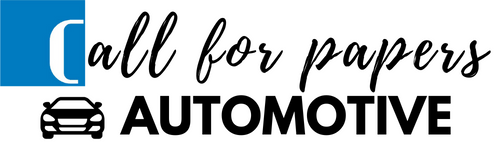
Finora, i tradizionali campi di applicazione dei materiali compositi erano limitati al trasporto leggero o agli articoli sportivi, ma oggi stanno guadagnando sempre più spazio anche in diversi rami di mercato. Ciò è chiaramente dovuto alle loro peculiari proprietà, come la loro leggerezza unita alle eccellenti proprietà meccaniche. D’altronde, alcune delle loro caratteristiche, come la bassa eco-sostenibilità ne limitano una diffusione capillare di cui ci sarebbe necessità. Ciò deriva principalmente dalle resine che vengono utilizzate come matrice composita, che sono solitamente polimeri termoindurenti, e come tali hanno più difficoltà di riutilizzo e smaltimento. Chiaramente, i compositi a matrice termoplastica possono essere una valida soluzione a questo problema, ma la loro viscosità tipicamente elevata è un limite per un’impregnazione delle fibre di successo.
Per ridurre tale problema Hikari, una start-up innovativa con sede a Briosco (MB) Italia, in collaborazione con Ranger Compositi, con sede a Castelletto Cervo (BI) Italia, insieme al Laboratorio Polimeri e Compositi del Dipartimento di Ingegneria dell’Università di Ferrara Italia, hanno studiato un nuovo materiale composito che è stato denominato Green Moulding Composite o GMC (fig.1). Questo materiale è simile a un normale Sheet Moulding Compound, cioè SMC, o un Bulk Moulding Compound, cioè BMC, ma in cui i tradizionali componenti sono stati sostituiti da soluzioni più compatibili con l’ambiente. Innanzitutto, le tradizionali fibre di vetro sono state sostituite da fibre naturali. Nel caso in questione, si tratta di fibre di lino che sono ovviamente di origine vegetale. In secondo luogo, anche la resina che viene utilizzata per impregnare le fibre di lino è un poliestere con una parte consistente di origine naturale, ovvero un materiale in cui circa il 50% in peso proviene anche da risorse rinnovabili. Infine, la carica minerale è stata sostituita da scarti di lavorazione di produzioni alimentari.
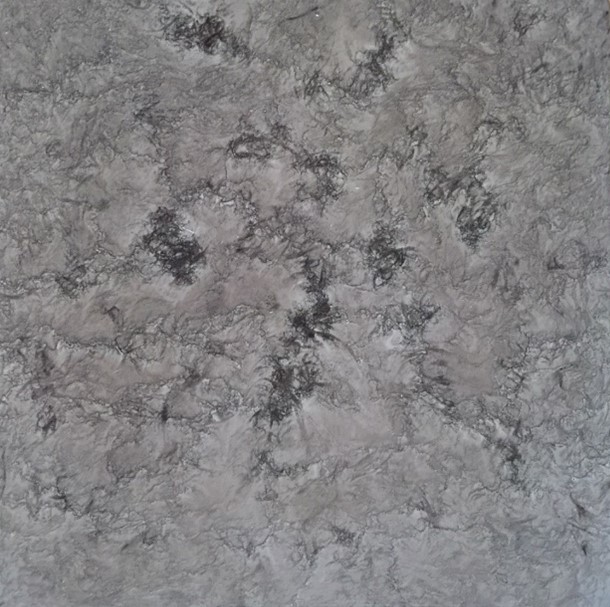
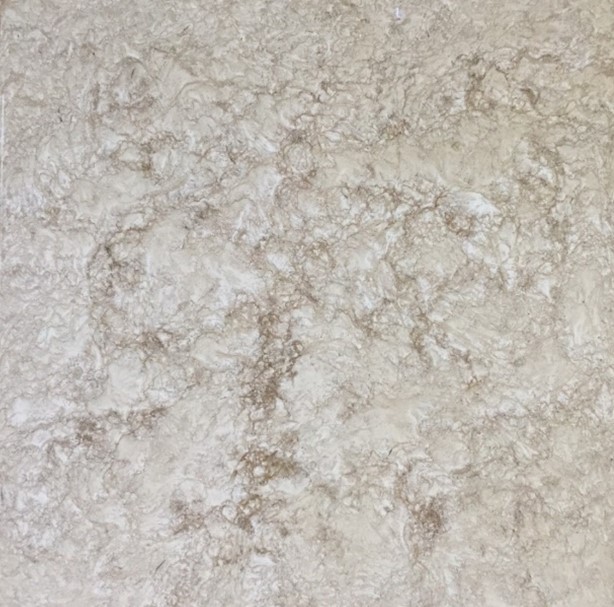
Il risultato finale è un materiale che può essere accostato ad un normale SMC o BMC e trasformato tramite un comune processo di stampaggio a compressione, ma il suo contenuto ecosostenibile è notevolmente superiore rispetto alle soluzioni tradizionali come vedremo dall’analisi della carbon footprint.
Hikari e Ranger Compositi hanno sviluppato tale materiale per la realizzazione di battery cover ecosostenibili (fig.2). Per realizzare questo progetto è stato importante trovare un compromesso tra un basso impatto ambientale e adeguate proprietà meccaniche. La battery cover, tipica applicazione dei materiali compositi nell’ambito delle vetture elettriche, infatti, possiede alcuni requisiti strutturali per cui si è dovuto garantire una resistenza adeguata visto che l’oggetto viene fissato ad un telaio e deve essere autoportante. Allo stesso tempo il settore automotive prevede numerose attività di riduzione della carbon footprint e questo richiedeva un minor utilizzo di fibre di vetro come rinforzo nella formulazione.
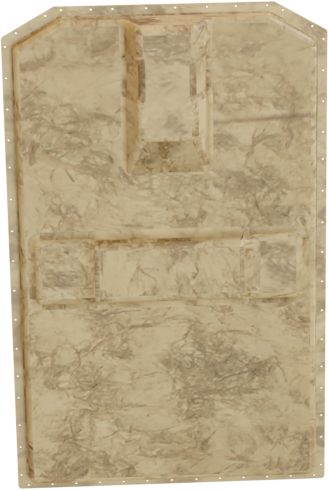
Come è noto, però, sostituire le fibre di vetro con fibre di origine vegetale non è un obiettivo facilmente raggiungibile. In questo caso i problemi da affrontare sono stati diversi, primo tra tutti il fatto che i valori medi di rigidità e resistenza sono inferiori a quelli delle normali fibre di vetro e la loro deviazione standard è maggiore rispetto a quella delle fibre sintetiche (tab.1). La seconda criticità, invece, era data da un valore inferiore delle proprietà meccaniche, che è stata affrontata ottimizzando il design del pezzo da produrre, in modo da raggiungere una soglia minima. Infine, per la dispersione, che può essere considerata una caratteristica peculiare dei materiali di origine naturale, l’unica soluzione praticabile è un design sovradimensionato per garantire la sicurezza.
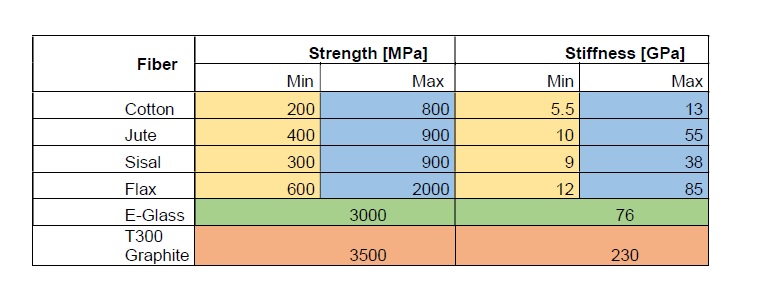
Un ulteriore problema che coinvolge l’uso di fibre naturali è l’interfaccia fibra-matrice. È noto che le fibre di origine vegetale sono particolarmente idrofile, poiché il loro principale componente strutturale è la cellulosa, che è un polisaccaride. Le matrici polimeriche, invece, sono spesso idrofobiche, o comunque non idrofile come la cellulosa; pertanto, talvolta è necessario l’utilizzo di opportuni agenti di accoppiamento per “costruire un ponte” tra i due componenti e quindi realizzare un efficiente trasferimento di carico tra la matrice e le fibre.
L’idrofilia delle fibre comporta un altro importante ostacolo: i poliesteri, che sono spesso usati come matrici composite, sono molto sensibili alla degradazione idrolitica, risulta quindi abbastanza chiaro che prima dell’impregnazione deve essere eseguita un’attenta essiccazione delle fibre, altrimenti il vapore acqueo che si svilupperebbe dalle fibre non essiccate degraderebbe il poliestere, abbassando ulteriormente le proprietà meccaniche del composito.
Un’altra sfida importante viene dal processo. A causa della natura idrofila delle fibre di lino, queste tenderebbero a fondersi insieme e formare fasci di fibre. La formazione di fasci di fibre è dannosa da molti punti di vista. Innanzitutto, il materiale risultante presenterebbe porzioni troppo ricche di fibre, oltre a porzioni troppo vuote di rinforzo. Ciò porta inevitabilmente a punti di concentrazione delle sollecitazioni mentre le parti sono caricate meccanicamente in servizio, e ciò a sua volta può causare guasti o deformazioni eccessive. Certo, ridurre la lunghezza delle fibre aiuterebbe sicuramente da questo punto di vista, ma d’altra parte l’effetto rinforzante delle fibre corte è molto inferiore a quello delle fibre lunghe; quindi, va ricercata una soluzione di compromesso tra proprietà meccaniche e de-bundling delle fibre. Per affrontare una tale sfida, il flusso di resina all’interno dello stampo durante lo stampaggio a compressione deve essere attentamente previsto in modo tale che i fasci possano essere rotti a causa dell’azione viscosa della resina liquida che scorre durante il processo di produzione.
Un ultimo problema legato anche alla lavorazione è il degrado termico della fibra. Le fibre vegetali sono costituite da cellulosa, emicellulosa e lignina. Nonostante la cellulosa, ovvero la componente strutturale, si degradi intorno ai 250°C, si raccomanda vivamente di non superare la temperatura di degradazione dell’emicellulosa, situata intorno ai 200°C, durante la lavorazione. Sebbene le temperature di indurimento siano generalmente inferiori a tali valori, i tempi di indurimento possono essere sufficientemente lunghi da consentire ancora il degrado termico delle fibre, portando ad un drastico decadimento delle proprietà meccaniche del materiale risultante, oltre a dare origine ad antiestetiche bruciature.
Con l’aiuto del Dipartimento di Ingegneria dell’Università di Ferrara, molti di questi problemi sono stati affrontati e risolti e GMC® è oggi una realtà. Le proprietà di trazione e flessione del GMC sono illustrate in figura 3. In effetti, le proprietà meccaniche non sono buone come quelle di un SMC rinforzato con vetro standard, tuttavia il materiale può essere utilizzato con successo per applicazioni moderatamente strutturali come Battery Cover per veicoli elettrici/ibridi.
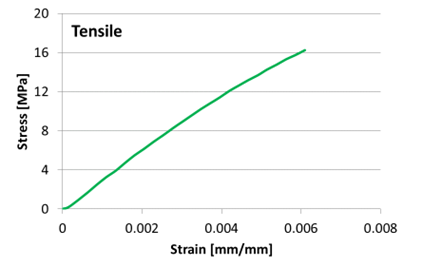
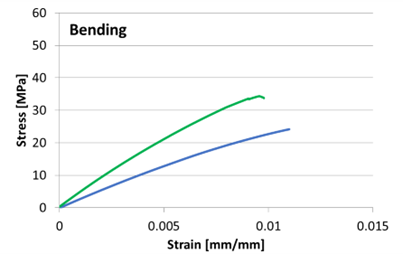
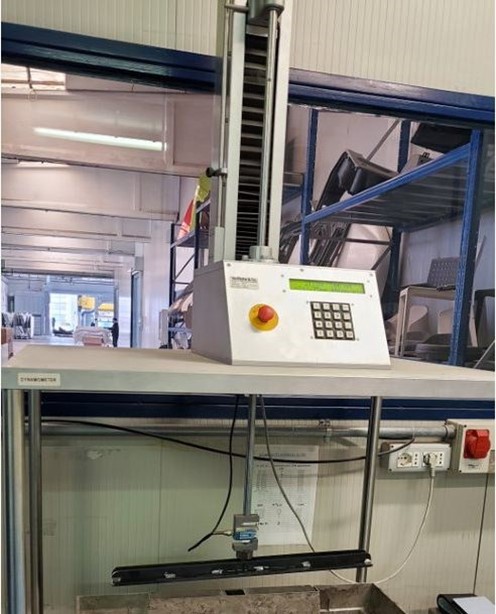
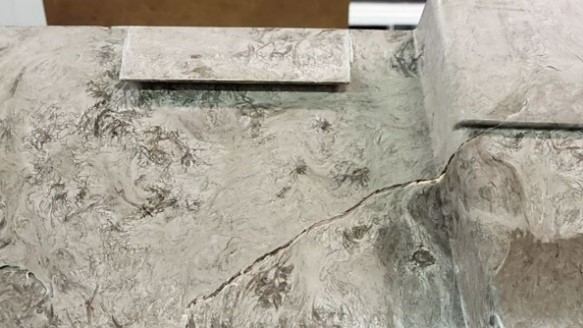
La società infine ha incaricato un ente esterno di calcolare la carbon footprint del GMC® rispetto alle soluzioni tradizionali, l’esito di tale sviluppo ha visto un risultato molto soddisfacente come mostrato in figura 5.
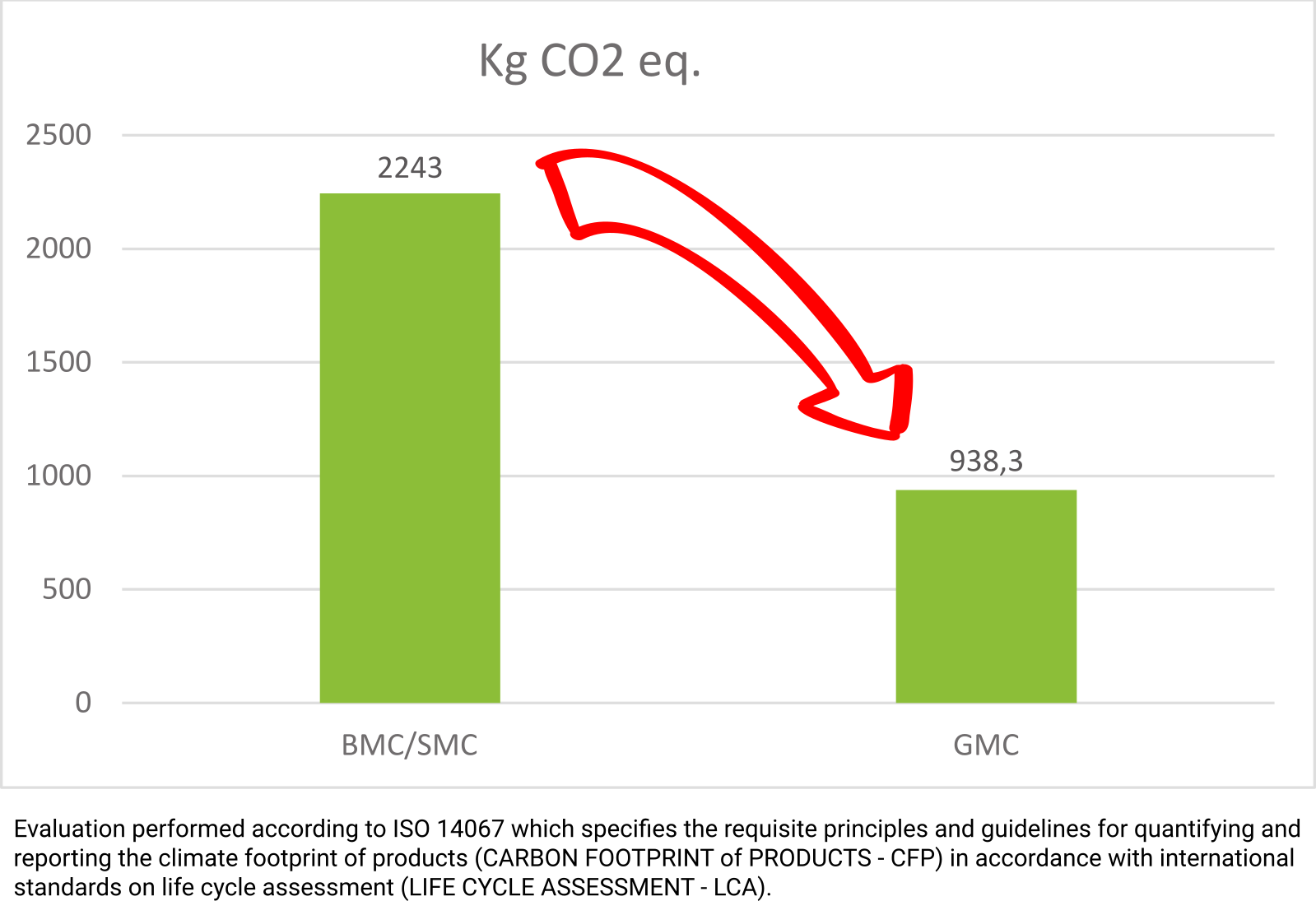
In conclusione, la partnership industria università ha raggiunto l’importante risultato di aprire un varco sullo sviluppo di materiale compositi ecosostenibili e la collaborazione tra le due entità si sta ora focalizzando su applicazioni in settori ed ambiti più diversificati dove l’uso dei compositi è ricorrente come il settore automotive e quello elettrico.