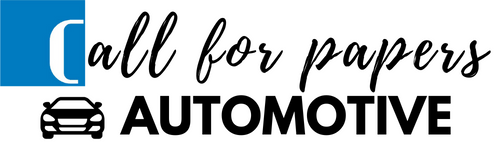
Claudia Persico – VP & Rotational Director del Gruppo Persico
OEM, Tier1 e tutte le aziende coinvolte nella filiera produttiva dell’automotive stanno lavorando per trovare la soluzione migliore verso la produzione di nuovi veicoli, intesi come complessi dispositivi elettronici nel rispetto dell’ambiente.
Il Gruppo Persico è coinvolto in questa evoluzione da molti punti di vista:
• rispetta l’ambiente e produce la propria energia elettrica rinnovabile per la sua sede centrale (sita a Nembro, in provincia di Bergamo) tramite energia solare e idroelettrica. Inoltre, l’energia non prodotta direttamente dall’azienda proviene da fonti rinnovabili;
• gestisce le regole richieste dagli OEM all’intera filiera produttiva dell’automotive: un piano di sostenibilità ambientale che coinvolgerà l’intero processo produttivo, creando prodotti a zero emission;
• affronta la situazione attuale, offrendo alternative al fabbisogno di gas e materie prime: per esempio, ha implementato la sua tecnologia SMART® per la produzione di corpi cavi;
• sviluppa e offre strumenti e attrezzature per la produzione di componenti di veicoli attuali e futuri, come i liner per serbatoi idrogeno e le cover per le batterie dei veicoli elettrici.
Serbatoi di idrogeno ad alta pressione
L’interesse per l’utilizzo dell’idrogeno in campo automobilistico è in crescita, non solo per il grande impegno nello sviluppo di soluzioni e tecnologie che ne consentano un facile utilizzo, ma anche per la creazione di componenti che ne semplifichino l’installazione sui veicoli. Uno degli aspetti rilevanti è lo stoccaggio dell’idrogeno: attraverso questa tecnologia, il gas deve essere immagazzinato a una pressione fino a 700 bar in serbatoi compositi in fibra di carbonio, con un guscio interno in polimero chiamato “liner”. I serbatoi di idrogeno sono sottoposti a carichi meccanici e termici (riscaldamento del gas quando il serbatoio viene riempito e raffreddamento quando avviene il consumo dello stesso). Allo stesso tempo, il rivestimento polimerico non deve piegarsi e collassare quando si svuota il gas del serbatoio. L’obiettivo è creare serbatoi leggeri e poco ingombranti che offrano alti livelli di resistenza e sicurezza.
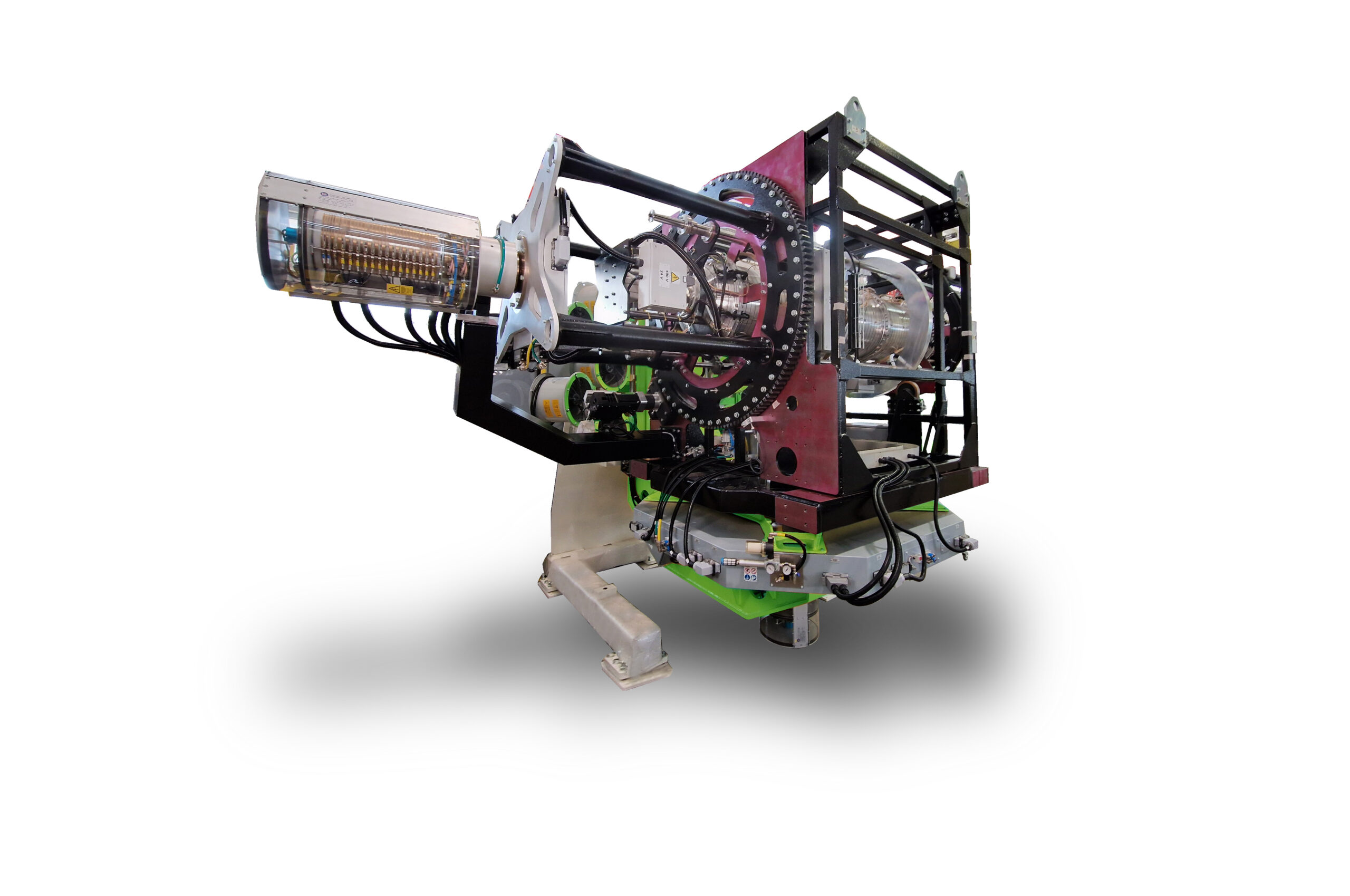
Negli ultimi anni, il Gruppo Persico ha lavorato con OEM e Tier1 per sviluppare un serbatoio in materiali compositi per lo stoccaggio dell’idrogeno.
Grazie al suo concetto innovativo, il peso del serbatoio e degli elementi accessori può essere ridotto di un terzo rispetto ai tradizionali serbatoi cilindrici in acciaio. La forma adattabile si presta a un elevato livello di flessibilità, consentendo un significativo risparmio energetico. Inoltre, i sistemi accessori sono integrati nel contenitore del serbatoio, riducendo lo spazio nel veicolo e facilitando la manutenzione. Il serbatoio interno è progettato su base modulare, per semplificare il processo di produzione. Diverse tecnologie producono rivestimenti in polimero per i serbatoi di idrogeno, come lo stampaggio a iniezione, il soffiaggio e lo stampaggio rotazionale.
I vantaggi dello stampaggio rotazionale: SMART® Technology
Si tratta di una tecnologia di lavorazione delle materie pastiche, basata sull’adesione della materia prima a stampi cavi in rotazione. Lo stampaggio rotazionale consente la produzione di corpi cavi anche di grandi dimensioni, che non necessitano di successive fasi di saldatura e montaggio. Diffusa nel mondo con forti tassi di crescita, questa tecnologia è apprezzata in svariati contesti, che vanno dal design all’architettura, dai componenti di veicoli alle lavapavimenti e ai serbatoi.
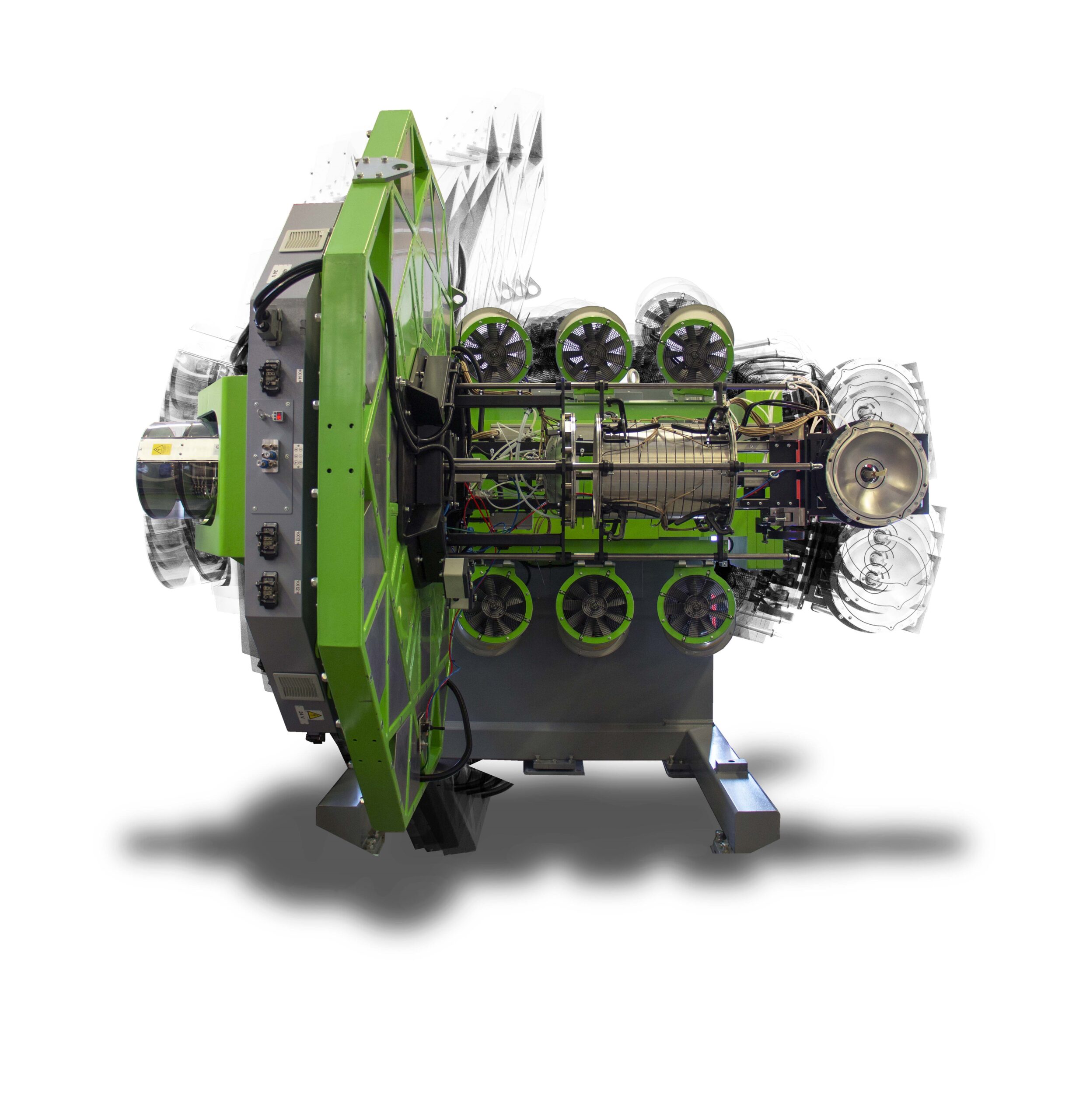
Le fasi di un processo di stampaggio rotazionale sono:
- caricamento del materiale polimerico nello stampo
- riscaldamento dello stampo in un forno e rotazione su uno o due assi, permettendo al materiale polimerico di aderire alle pareti dello stampo
- raffreddamento dello stampo, sempre in rotazione, consentendo la solidificazione del materiale polimerico nella forma desiderata
- apertura dello stampo ed estrazione del manufatto plastico.
Attraverso la tecnologia SMART®, lanciata nel 2013, Persico ha sviluppato macchine e utensili DTH (riscaldamento diretto dell’utensile) per stampare centinaia di prodotti diversi, tra cui rivestimenti e gusci rimovibili per prodotti compositi.
SMART® è una cella di produzione compatta, pulita e sicura che offre un uso efficiente di energia e materiali. La produzione può essere completamente automatizzata, grazie alla combinazione di una o più macchine con robot antropomorfi. Queste celle possono eseguire il caricamento delle polveri, il caricamento degli inserti, la spruzzatura del distaccante, i cicli di stampaggio automatizzati e lo scarico del prodotto. Di conseguenza, la tecnologia rotazionale garantisce alti tassi di produzione, risparmi sui costi di produzione, riduzione della manodopera e rapido ritorno dell’investimento.
Rispetto ai processi di stampaggio rotazionale tradizionali, SMART® ha un ingombro molto ridotto e funziona per mezzo del riscaldamento elettrico, anziché impiegare il gas. Possono essere presenti fino a 48 zone di riscaldamento elettrico separate, ciascuna con monitoraggio e controllo della temperatura. La temperatura interna, la pressione, il vuoto, l’atmosfera inerte e il raffreddamento interno sono tutti disponibili con un controllo completo e consentono ad un’ampia gamma di materiali di essere trasformati in prodotti finali complessi.
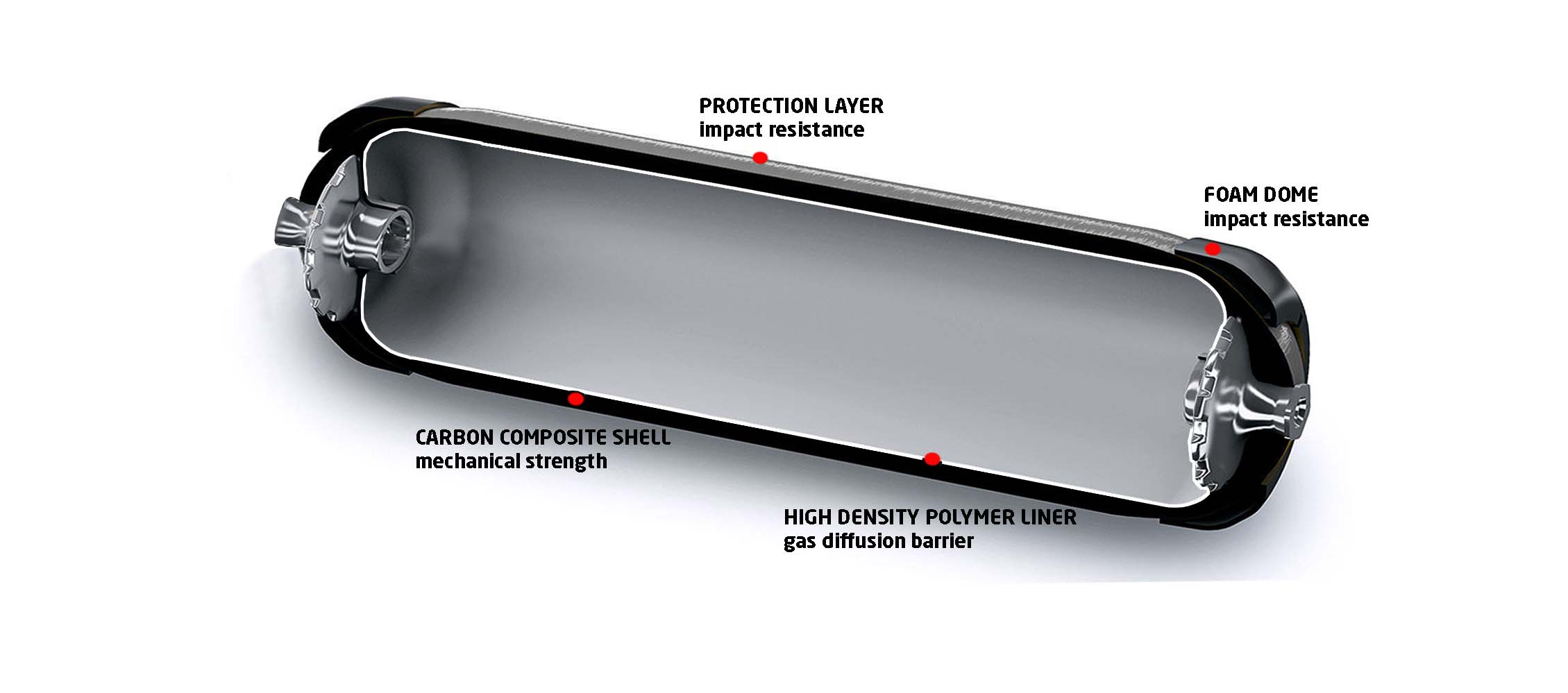
Queste caratteristiche permettono:
- cicli più brevi e ripetibili
- ripetitività del processo e meno scarti
- massima efficienza di scambio termico (DTH SMART®)
- controllo degli spessori delle pareti
- automazione.
Queste premesse garantiscono inoltre un risparmio sui costi di produzione.
I liners prodotti con il processo di stampaggio rotazionale
Un serbatoio a pressione per idrogeno di Tipo IV è composto da:
- Liner in polimero: lo strato interno termoplastico è a tenuta di gas e garantisce una buona barriera.
- Rivestimento in materiale composito: sopportando il carico, il materiale composito è la parte strutturale del serbatoio.
- Boccole: la borchia metallica funge da collegamento tra il liner e la valvola di riempimento.
Persico ha sviluppato e consegnato diversi progetti per la produzione di liners per serbatoi idrogeno ad alta pressione e bombole CNG. Questi progetti hanno incluso la progettazione e lo sviluppo del liner, la prototipazione e la fornitura di macchine e stampi in celle di produzione “chiavi in mano”. L’azienda ha sviluppato una nuova generazione di macchine SMART® specificamente pensate per la produzione di liners:
- SMART® 2.8: può essere scelto per la produzione di piccoli rivestimenti e per la produzione di prototipi.
- KIT H2®: partendo dalla macchina tradizionale SMART® 2.8, il KIT H2® è composto da un telaio con un sistema di rotazione dedicato, in grado di gestire il movimento rock&roll per la produzione di liner di medie dimensioni.
- SMART® H2: questa macchina offre un movimento rock&roll con velocità indipendenti per la produzione di liners di grandi dimensioni e, ove necessario, può essere potenziata per realizzare liners XL.
Tutte queste soluzioni possono essere parzialmente o completamente automatizzate, compreso il carico delle polveri, il carico degli inserti e lo scarico delle stampate.