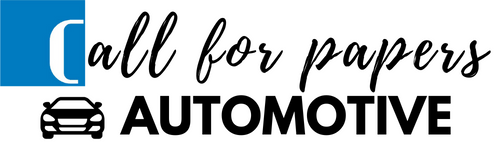
The automotive industry is in the midst of a revolution, grappling with urgent sustainability requirements and expectations. From the environmental impacts of material sourcing and manufacturing to novel propulsion technologies and end-of-life disposal, the challenges are complex and multifaceted. The design, production, and adoption of electric vehicles (EVs) has been a significant step forward, but truly reducing the sector’s carbon footprint requires a broader rethink. One promising avenue of exploration lies in the realm of “sustainable lightweighting” and dematerialisation– using natural fibre composites with viable, ‘circular’, end-of-life possibilities.
Volvo Cars is now the first global automotive manufacturer to use such a material in serial production. The exciting new EX30 small SUV will have the lowest carbon footprint of any model in Volvo Cars’ history, and launch with an option for innovative natural fibre composites in its dashboard and door trim. Bcomp, the Swiss producer of the natural fibre composites used in the EX30, is excited by the possibilities of large-scale automotive applications.
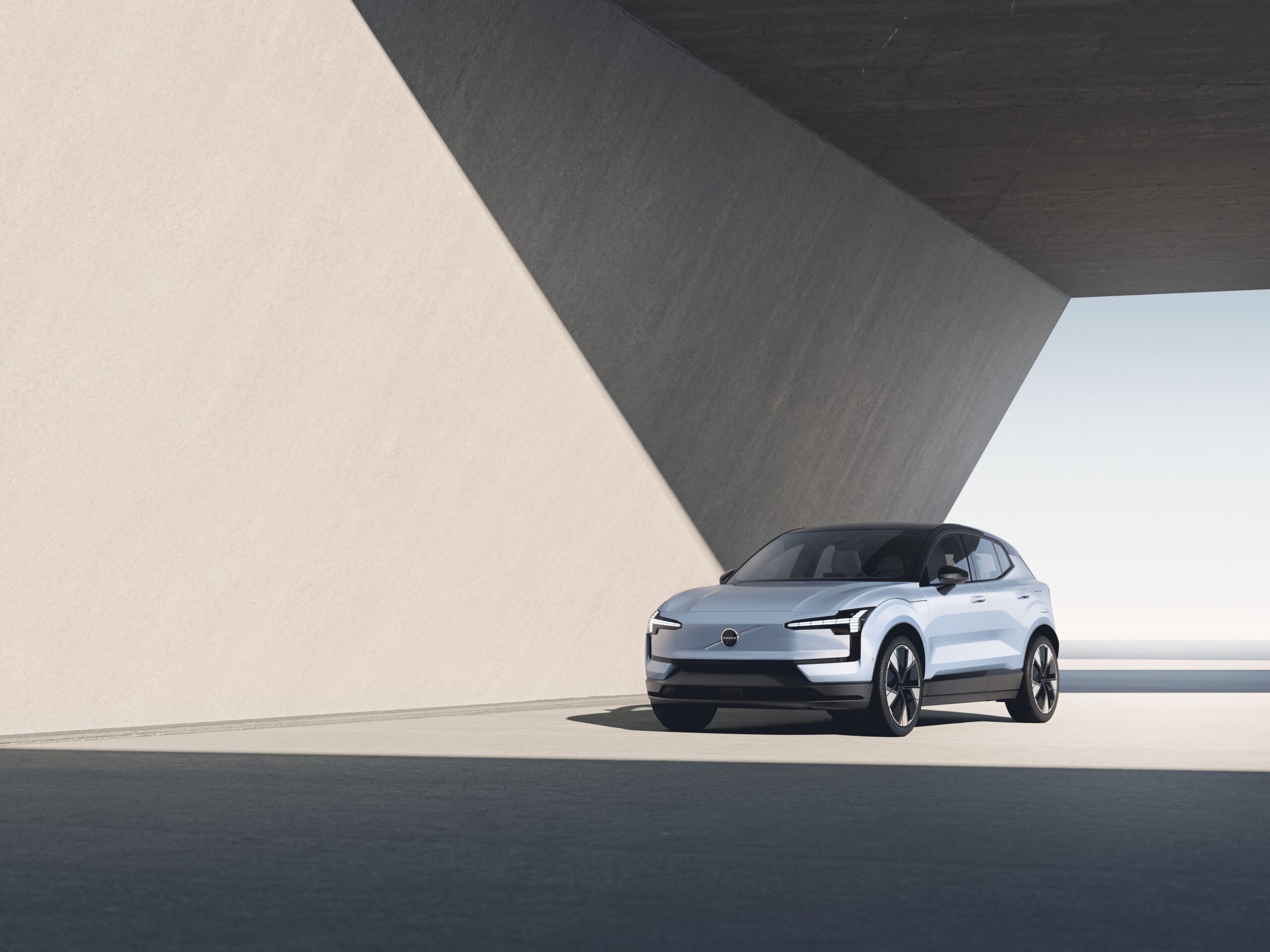
“Working with Volvo Cars to integrate our flax fibre-based composites into a global, serial production vehicle has been a milestone moment – explains Per Mårtensson – While we have harnessed our technologies to deliver a range of sustainable lightweighting solutions in industries like motorsport, marine, and sports equipment, inclusion in a large-scale automotive application is a hugely positive sign for us, our technology, and Volvo’s sustainability ambitions.”
The EX30 compact, all-electric SUV unites Scandinavian aesthetics, cutting-edge technology, and uncompromising safety standards. Above all, it represents a more sustainable future for personal automotive transport. The EX30 is offered with four distinct interior ‘rooms’, each presenting a different ambience for drivers to choose from and intended to reflect the harmony between personalised comfort and sustainable living. Two of these rooms include high-quality parts made from Bcomp’s ampliTex™ technical fabric, a woven flax textile designed specifically for use in composites.
“Our ampliTex™ technical reinforcement fabric is derived from renewable European-grown flax fibres – continued Mårtensson – Not only does it leverage the natural strength and stiffness characteristics of flax, but it allows to produce lightweight high-performance composites with a distinct aesthetic. With low weight, high stiffness, excellent vibration damping, and strength, ampliTex™ composites provide a unique material choice for a host of applications, including automotive interiors and bodywork.”
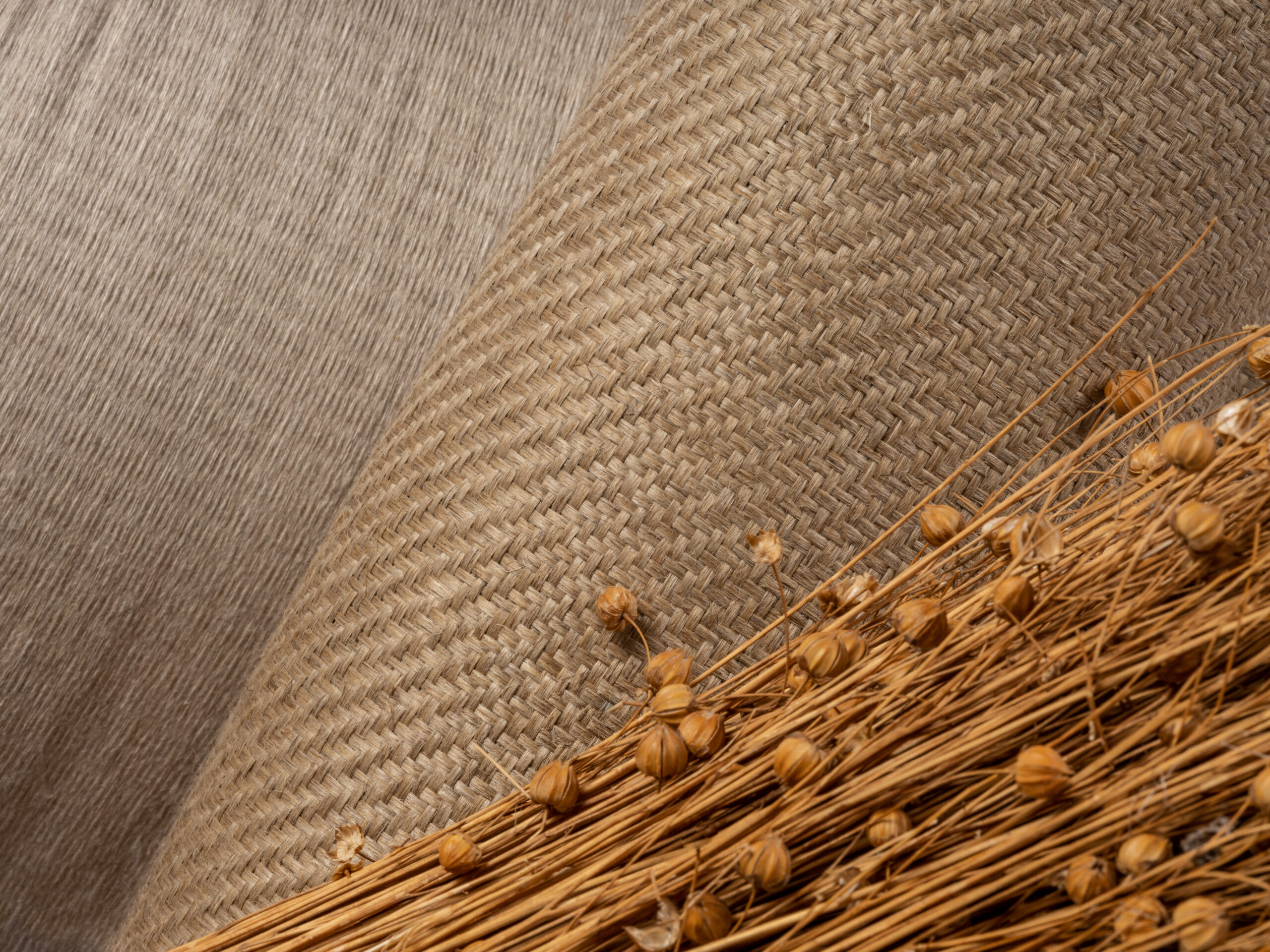
The relationship between Volvo Cars and Bcomp began in 2018 with the Volvo Ocean Race Recycled Plastics Demonstrator Vehicle, which focused on recycled and circular materials. This concept car used powerRibs™, another Bcomp flax composite technology, in several semi-structural interior components and highlighted the viability of the material to Volvo’s engineering team. This led to the inclusion of Bcomp technologies in the Volvo Cars Concept Recharge, a vehicle that demonstrated Volvo’s EV development aims and intentions to reduce its carbon footprint.
Revealed in the Summer of 2021, Concept Recharge used Bcomp’s natural fibre composites for the lower storage areas, the back of the headrest, and the footrest. They were also used extensively in the exterior, for both front and rear bumpers as well as the sill mouldings. Compared to regular plastic parts, the natural fibre-based composites enable parts to be up to 50 per cent lighter, use up to 70 per cent less plastic and generate up to 62 per cent lower CO2 emissions.
Soon after, the Volvo Cars Tech Fund decided to invest in the company, citing the immense potential for Bcomp technologies in the automotive sector. While not directly connected to Bcomp’s work with Volvo Cars, the investment did expand opportunities for future collaborations. The natural next step was to integrate Bcomp materials into a production car, and the highly ambitious EX30 programme was the perfect opportunity.
“By successfully integrating ampliTex™ into the EX30, a high-volume production vehicle, we have shown the world that it is possible to achieve outstanding quality, comfort, and performance without compromising on sustainability. – continued Mårtensson – This is particularly true for car interiors, where we can achieve a high level of visual finish and quality while also offering something different, attractive, and more sustainable. We have invested heavily in production capability; it is the next step in our plan to enable the large-scale mobility industry to use sustainable, circular solutions.”
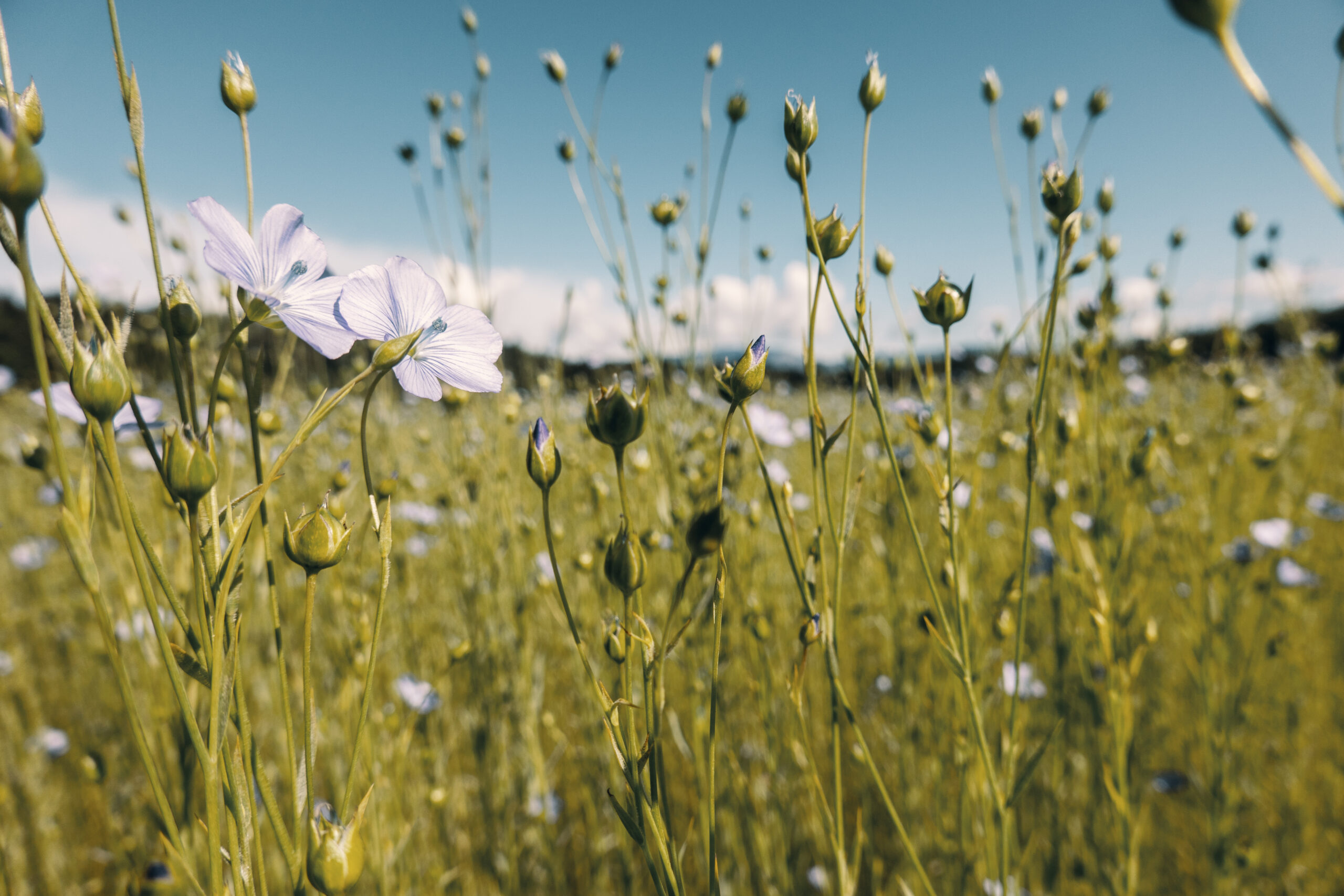
To date, Bcomp’s technologies have found their way into a variety of sectors and applications. They have been used extensively in sustainability-oriented motorsport programmes, replacing emission-intensive and infrequently recycled carbon fibre. With inherently better damping than conventional composites, ampliTex™ has been used in performance skis and other sports equipment. Its unique appearance and visual texture have also seen the material included in everything from high-value furniture to watches. When it comes to automotive, Bcomp is already working on its next project with Volvo Cars’ performance arm, Polestar. While the details remain a secret, for now, it is set to expand serial production applications further still.
“Application in the EX30 has been an exciting first step, but the potential for other interior applications is vast. – concluded Mårtensson – Essentially, our composites could be used to replace most injection-moulded components; entire door panels and seat backs are perfect examples. It is about moving beyond the special ‘visual’ parts (where you can see the weave) and into the non-visual, ‘everyday’ pieces of interior trim that could benefit from increased sustainability and more viable end-of-life options. While automotive is just one of many exciting applications for our technologies, it is an area that has demonstrated significant interest, expansion, and shows immense promise.”
As the journey towards sustainable automotive manufacturing gathers pace, pioneering collaborations such as the one between Volvo Cars and Bcomp are making impressive strides. The mainstream adoption of natural flax fibre composites, specifically Bcomp’s ampliTex™, in automotive interiors is a landmark moment in the industry’s history. These innovative materials offer not just a unique aesthetic, but also provide a practical solution to reduce the environmental impact of vehicle production, underlining the promise of a circular economy in the automotive landscape.