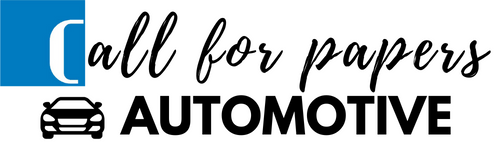
As the market sees a growing number of electric and hybrid electric vehicles, automotive OEMs are increasingly investigating into the utilization of composites. The aim is to reduce the weight of different components, ultimately boosting the vehicle’s range. An example of recent success in this attempt is the hybrid-electric 2022 Toyota Tundra pickup truck, which features an acclaimed second-row seat frame made entirely of composites.
When designing the 2022 Tundra pickup truck, Toyota’s engineering team in Ann Arbor, Mich., U.S., looked for ways to make the vehicle not only as lightweight and efficient to manufacture as possible, but also cost effective, design flexible and more storage space for the end user.
With these goals in mind, Toyota collaborated with several suppliers to make it happen. The main composite components were manufactured by injection molded, Flex-N-Gate. The composites material was developed in collaboration with BASF. And the pultruded system using Continuous Composite Systems™ (CCS™) was developed by L&L Products.
Developing the pultruded beam: stiffness and strength with less weight
L&L Products was contacted at an early stage of the process to explore if Continuous Composite Systems™ (CCS™) could be a solution. Although CCS™ had many applications previously, it had never been used for any type of interior automotive application before. Modeling and simulation played an imperative role in the design process to ensure all the goals would be met by implementing CCS™ into the seatback frame.
Hank Richardson, product engineering manager of L&L Products, explains what makes the pultruded beam crash resistant: “A combination of resin chemistry tuned for very high stiffness, continuous glass members for maximum flexural strength and optimized part geometry.”
Why pultrusion? He adds, “Pultrusion was the most cost-effective process to use. You get very high flexural strength because of the continuous fibers, but it’s lighter weight than aluminum or steel, so the strength-to-weight ratio is very high. And the pultrusion process itself is simple — you have one process, then machine a few holes, then it goes straight to over molding. It’s extremely efficient, which makes it cost-effective.”
“We continue to show how pultrusion can deliver lightweight, cost-effective solutions as well as integrated functionality,” said Kipp Grumm, Technology Leader for Thermoplastic Composites, Performance Materials, BASF Corporation. “The unique design of the injection over molded pultruded beam in the seat structure also passed all relevant crash test requirements and opens the door for more adoption of composites in automotive applications.”
One resulting innovation is a composite second-row seat frame that saves significant weight versus a steel version and reduces the overall number of frame components from 60+ to just 4.
Finalists for the 2023 JEC Innovation Award for Composite Seatback Design
BASF, Flex-N-Gate, Toyota, and L&L Products were named as finalists for the 2023 JEC Innovation Award in the Automobile and Road Transportation – Design Part category with the composite seatback design on the 2022 Toyota Tundra™. This project has previously won the 2022 Altair Enlighten Award for achievements in weight savings and the 2022 SPE Automotive Innovation Award.