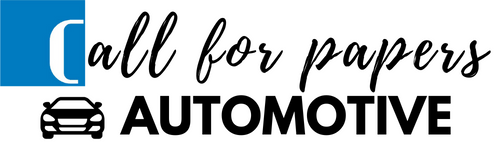
R. Dotoli, A. Gerardi, M. Arganese, F. Fontò – CETMA
G. Savino, D. Cafagna, C. De Luca – Base Protection
Il sistema di riciclo per gli scarti industriali dei prepregs in fibra di carbonio diventa realtà; è quanto merge dai risultati a conclusione del progetto europeo CIRCE (Circular Economy Model for Carbon Fibre Prepregs), nato dalla collaborazione di cinque aziende italiane (HP Composites S.p.A., Alci s.r.l., Base Protection s.r.l., Cetma organizzazione di ricerca e tecnologia, Petroceramics S.p.A.) e finanziato nell’ambito del programma LIFE (LIFE ENV/IT/00155).
La partnership tra le aziende coinvolte ha dimostrato che è possibile riutilizzare gli sfridi dei prepreg in fibra di carbonio per produrre componenti strutturali come parti auto, dischi freno, puntali per scarpe antinfortunistiche e non solo. L’obiettivo comune era di incoraggiare il riutilizzo dei materiali compositi attraverso il paradigma dell’economia circolare dimostrando la validità ed applicabilità strutturale del materiale di scarto in vari settori. Oltre all’applicabilità per le prestazioni strutturali, è stato dimostrato anche il contributo allo sviluppo sostenibile e la convenienza economica [1.][2.].
Durante la fase di taglio dei prepreg per la realizzazione di un componente in composito si genera uno scarto compreso tra il 20% e il 50% del materiale vergine come indicato in figura 1. Questo scarto di materia prima viene tipicamente smaltito in discarica o in inceneritori poiché ritenuto, sinora, non utilizzabile. I partners coinvolti nel progetto hanno sviluppato un processo industriale per selezionare, recuperare e utilizzare il 100% degli sfridi della lavorazione di taglio. A fine progetto si è calcolato che un’azienda di medie dimensioni può arrivare a recuperare circa 10t/anno di materiale dal conferimento in discarica.
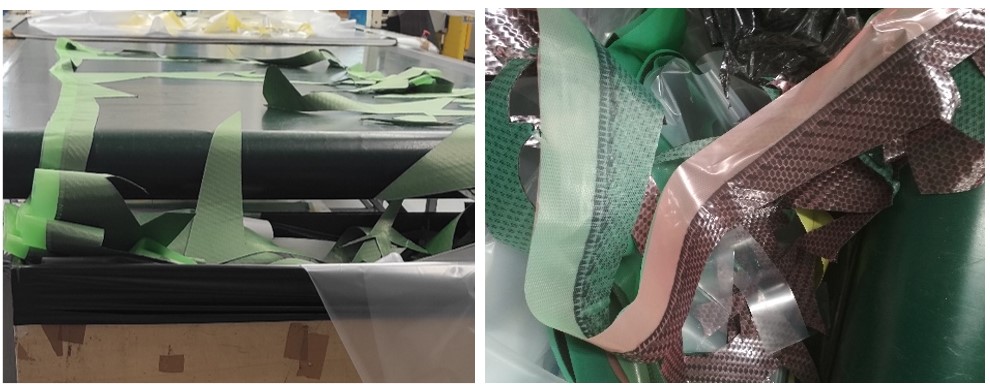
Il progetto mira ad innescare un modello di economia circolare in cui, oltre alla selezione del materiale per dimensioni e forma, è previsto il suo confezionamento e conservazione fino alla disponibilità di reinserimento in nuovo ciclo produttivo. I costi stimati, suscettibili di ulteriore rimodulazione al ribasso, sono di circa 5-7 €/Kg per il tessuto pre-impregnato proveniente dal riciclo contro i circa 20-30€/kg dello stesso materiale vergine. Le proprietà meccaniche del materiale composito ottenuto con prepreg riciclato si conservano, restando strutturalmente confrontabili alle proprietà di una lega di alluminio.
Gli ambiti applicativi sono stati individuati con l’intento di sfruttare le peculiarità del tessuto preimpregnato da riciclo, come la quasi isotropia dal punto di vista delle prestazioni meccaniche.
Tra gli utilizzi strutturali analizzati, è stato possibile realizzare puntali per calzature da lavoro sostituendo completamente il materiale tradizionalmente utilizzato. In particolare, Cetma ha supportato l’azienda Base Protection nella progettazione del nuovo puntale eco sostenibile attraverso un approccio numerico sperimentale. Entrambi i partner hanno lavorato sinergicamente con la finalità di validare e certificare l’impiego dello scarto dei tessuti pre-impregnati in fibra di carbonio per la produzione dei puntali per calzature antinfortunistiche.
Nella prima fase Cetma si è occupato dello studio sperimentale del processo di stampaggio a compressione del prepreg riciclato. I parametri del processo sono stati ottimizzati allo scopo di minimizzare i vuoti (fig.2) e massimizzare le proprietà meccaniche del materiale.
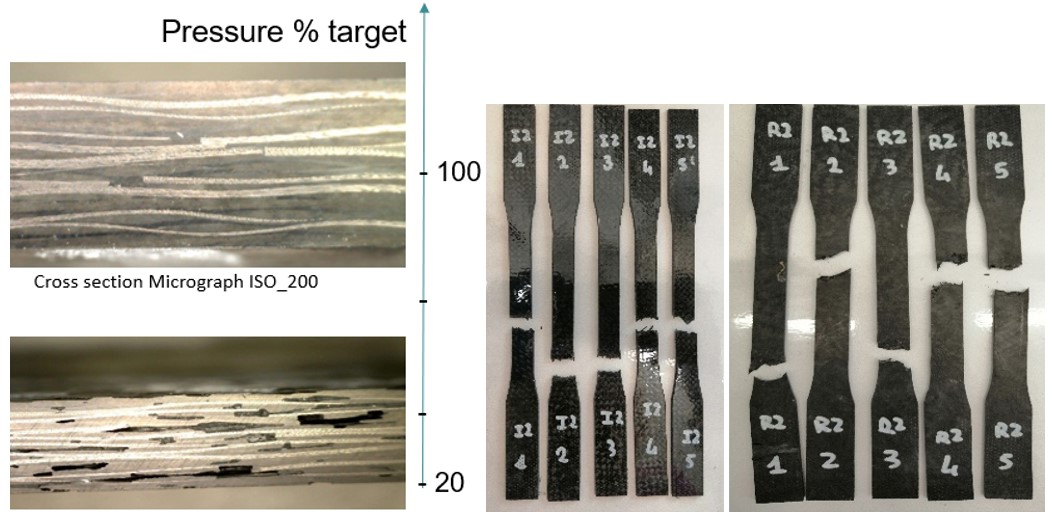
Per la progettazione del puntale sono stati effettuati, in particolare, test di caratterizzazione meccanica a trazione e ad impatto. La verifica dell’idoneità del prepreg riciclato per la produzione dei puntali è stata effettuata avvalendosi degli strumenti di virtual testing e simulazione agli elementi finiti. Ė stato validato un modello numerico del materiale, applicato al prototipo di puntale, in grado di prevedere le prestazioni ad impatto del componente con il 100% di materiale da riciclo. Il modello numerico validato, come riportato in figura 3, ha permesso di condurre virtualmente le verifiche strutturali rispetto ai test previsti dalla norma per ognuna delle possibili geometrie proposte.

Attraverso un’intensa campagna di analisi dei test virtuali, Cetma ha definito lo spessore e la stratificazione del materiale composito in grado di resistere ai test di omologazione del puntale. È stata effettuata anche una successiva fase di ottimizzazione strutturale che ha consentito di mettere a punto le zone di accoppiamento del puntale con la geometria di calzatura, in particolare, la calzatura da lavoro della linea Kaptive di Base Protection. I risultati ottenuti dai test virtuali hanno permesso di definire la geometria finale (fig.4) e giungere alla fase di realizzazione dello stampo.

Quindi, si è passati alla progettazione e realizzazione dello stampo per la produzione dei prototipi mediante il processo di stampaggio a compressione. I prototipi sono stati processati e realizzati dai tecnici del laboratorio materiali e processi di Cetma secondo i parametri e la stratificazione in precedenza individuati.
L’ultima attività è stata la validazione del modello di puntale secondo i test della normativa; presso il partner Base Protection sono stati testati i prototipi per verificare le capacità strutturali del puntale ottenuto dagli sfridi dei tessuti in fibra di carbonio (fig.5).
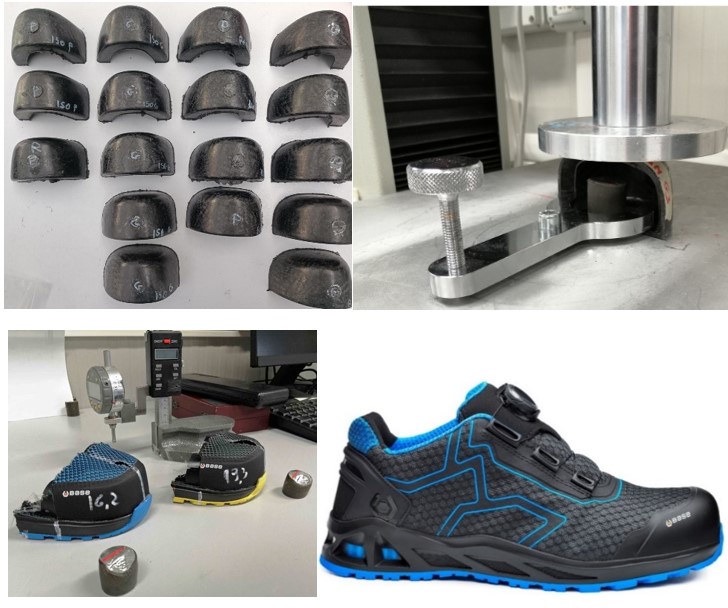
I risultati dei test di laboratorio hanno confermato la resistenza all’impatto della geometria realizzata con il 100% di materiale da riciclo come previsto dai test virtuali. L’azienda Base Protection ha effettuato ulteriori test specifici di prodotto con il puntale inserito nel modello di calzatura Kaptive. Anche in questo caso, i risultati ed il superamento dei test, con un margine di circa il 22% rispetto al target minimo previsto dalla normativa, hanno certificato l’impiego del puntale per calzature da lavoro.
Il processo di riciclo degli sfridi di prepreg ha dimostrato la riduzione dei costi e dell’impatto ambientale nella produzione di compositi rinforzati con fibra di carbonio. Il completo riutilizzo degli sfridi del prepreg ha evidenziato l’esistenza di ambiti applicativi dove è possibile sostituire il materiale vergine e abbattere la produzione di scarti industriali. Una fase cruciale dello sviluppo di componenti in prepreg da riciclo rimane quella della progettazione, che va effettuata tenendo conto delle peculiarità specifiche del materiale, per cui l’approccio numerico-sperimentale proposto da Cetma appare sicuramente imprescindibile.
Risulta evidente il contributo allo sviluppo sostenibile e le nuove prospettive di mercato per i produttori di componenti in materiale composito rinforzato con fibra di carbonio. Cetma continua ad investire sull’argomento; infatti, sono stati avviati due nuovi progetti, uno europeo in cui si sta sviluppando una procedura industriale per l’analisi dello stato della resina dei prepreg di scarto, ed uno nazionale in cui Cetma si doterà di una linea automatizzata per il riciclo dei prepreg.
Bibliografia
[1.] “Comparative life cycle assessment of safety shoes toe caps manufacturing processes” I. Bianchi, A. Forcellese, M. Simoncini, A. Vita, V. Castorani, D. Cafagna, G. Buccoliero; International Journal of Advanced Manufacturing Technology (2022).
[2.] “Life cycle impact assessment of safety shoes toe caps realized with reclaimed composite materials” I. Bianchi, A. Forcellese, M. Simoncini, A. Vita, V. Castorani, M. Arganese, C. De Luca; Journal of Cleaner Production (2022).