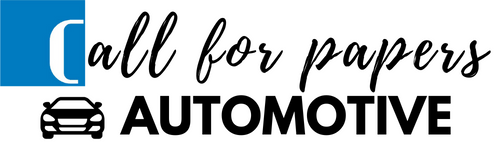
Daisuke Yoshimizu, Ryo Harada – Advanced Components Development Center, TOYOTA INDUSTRIES CORPORATION
Reducing CO2 emissions has become an important issue in the field of transportation, including airplanes and automobiles. It’s necessary to improve energy efficiency through weight reduction. CFRP, a lightweight material with high strength and elasticity, is gaining attention as a solution to this issue. Using CFRP can greatly reduce CO2 emissions compared to steel and aluminum during use. However, a lot of CO2 is released during CFRP production, and most used CFRP and leftover materials end up in landfills. With the growing CFRP market, there is a high demand for developing recycling technologies.
To meet these social needs, we’ve developed a technology that aligns recycled carbon fibers from used CFRP into uniform and consistent spun yarn. We achieved this by adapting our long-established cotton spinning methods for carbon fiber (Fig.1).
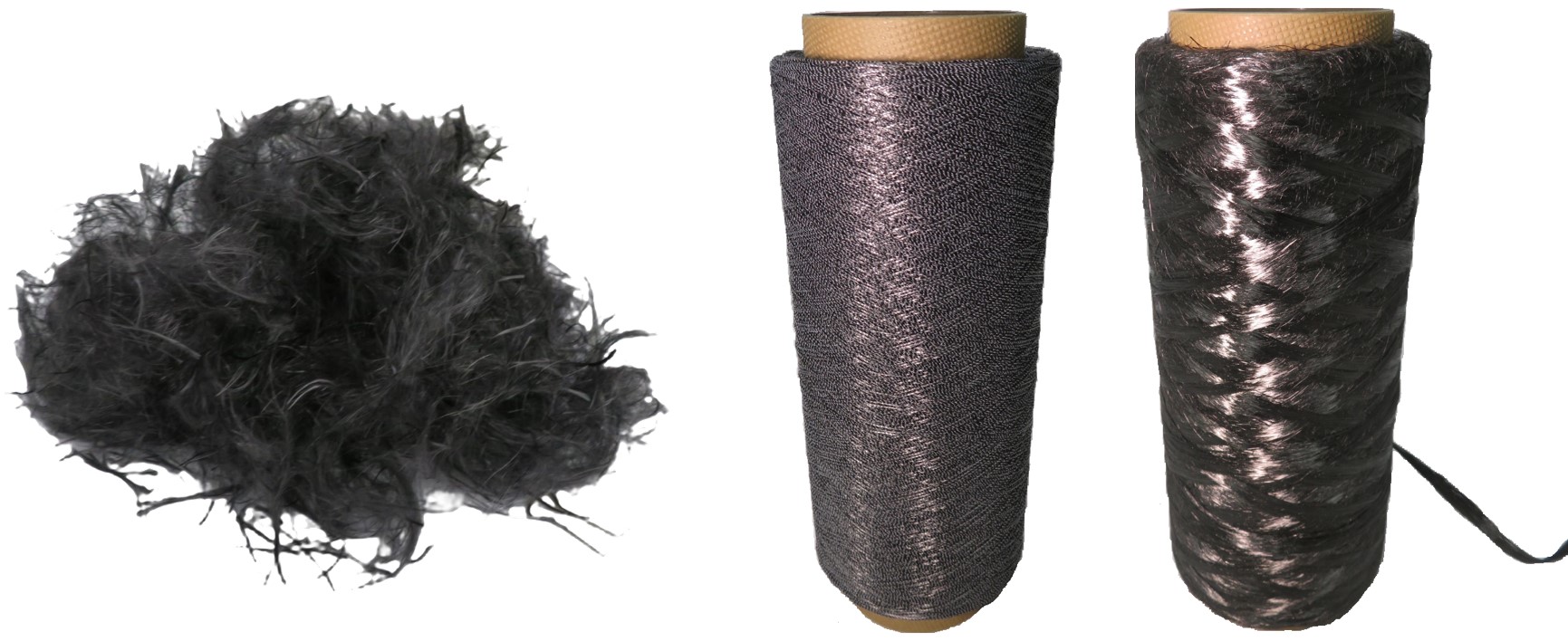
The majority of CO2 emissions in new carbon fiber production come from the calcination process. By using recycled materials, this process is no longer needed, resulting in a reduction of CO2 emissions by approx. 80%. However, traditional CFRP recycling methods involve using recycled CF as pellets for injection molding mixed with resin, or making nonwoven fabric by blending a large amount of chemical fiber with recycled CF. These methods face issues of poor performance and usability due to the low Vf and inconsistency in fiber direction.
In contrast, our technology creates non-twisted yarns made only of recycled carbon fibers with a consistent fiber direction. As a result, CFRP using our Recycled CF Spun yarn has properties similar to those of virgin materials. Although the number of flexural tests we conducted was not sufficient, the flexural strength was approximately 70% and the flexural modulus was approximately 90% of those using new material under the same test conditions. Another benefit of spun yarn is the ability to choose any yarn count freely. Currently, we can produce yarn counts in the range of 100-1600 tex. Commingled yarn can also be created by mixing synthetic fibers in any desired proportion, and it is anticipated for use in molding processes that don’t require resin infusion (Fig.2).
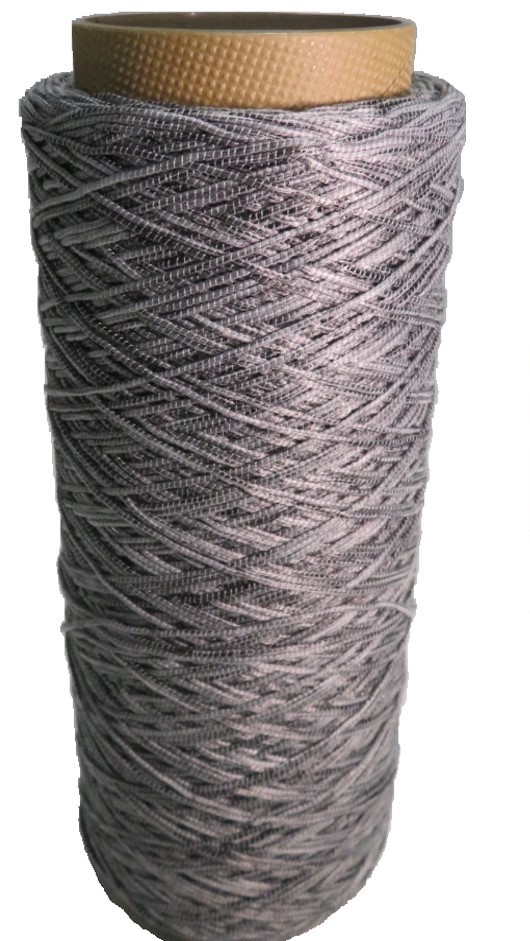
Since our recycled CF spun yarn is a “yarn”, it can be used with the same equipment and production methods as new materials without any new investment. For example, conventional rapier weaving machines and sequencing equipment can be used for weaving. Additionally, this technology might be used for air-jet weaving machines, which are now hard to use with carbon fiber weaving. As a result, weaving costs could be lowered. It can also be used as prepreg, and molding methods such as autoclave and press can be selected. In addition, it can be applied to RTM and pultrusion molding.
Toward the Realization of a Comprehensive CFRP Recycling System
Toward the development of the CFRP recycling market, we are aiming to establish a comprehensive CFRP recycling system (Fig.3). In this system, once the CFRP products made from virgin materials finish their job, they go through a process that separates the carbon fiber from the resin. Then, using our spinning technology, they become Recycled CF Spun yarn. After this, they are used again as recycled CFRP products through several processing step. This recycled CFRP product will be recycled again, and the circulation of CFRP will be realized. The system is designed to allow open participation by external companies and partners, aiming to expand the scale of the circulation system and promote innovation.
The comprehensive CF recycling system has a number of unique features, including in-line inspection and quality assurance of recycled CF, and unique design and CAE tools that enable more efficient product application. Currently, we are developing measurement equipment for inspection optimized for carbon fiber, as well as a high-precision multi-scale CAE that augments the capabilities of existing design and evaluation support tools by connecting the yarn – fabric – product scales with a unique material constitutive law constructed based on mathematical homogenization methods (Fig.4).
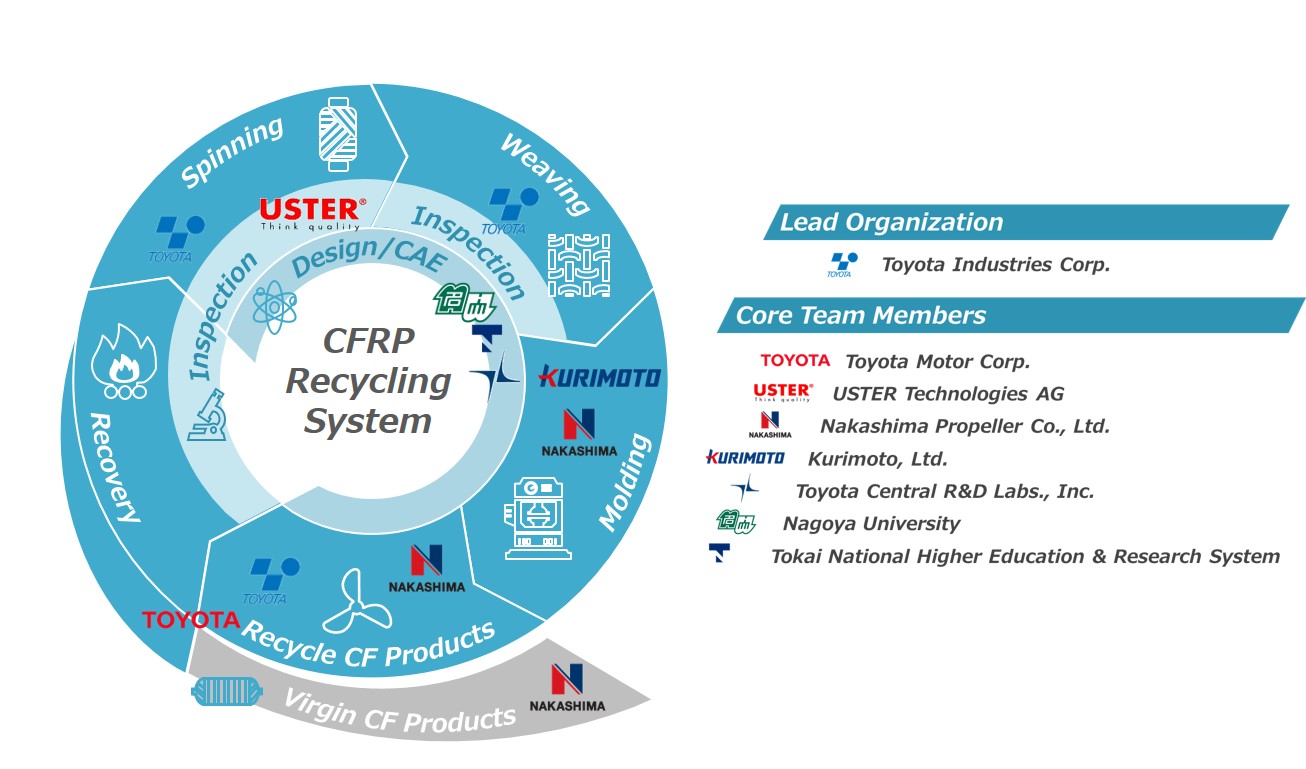
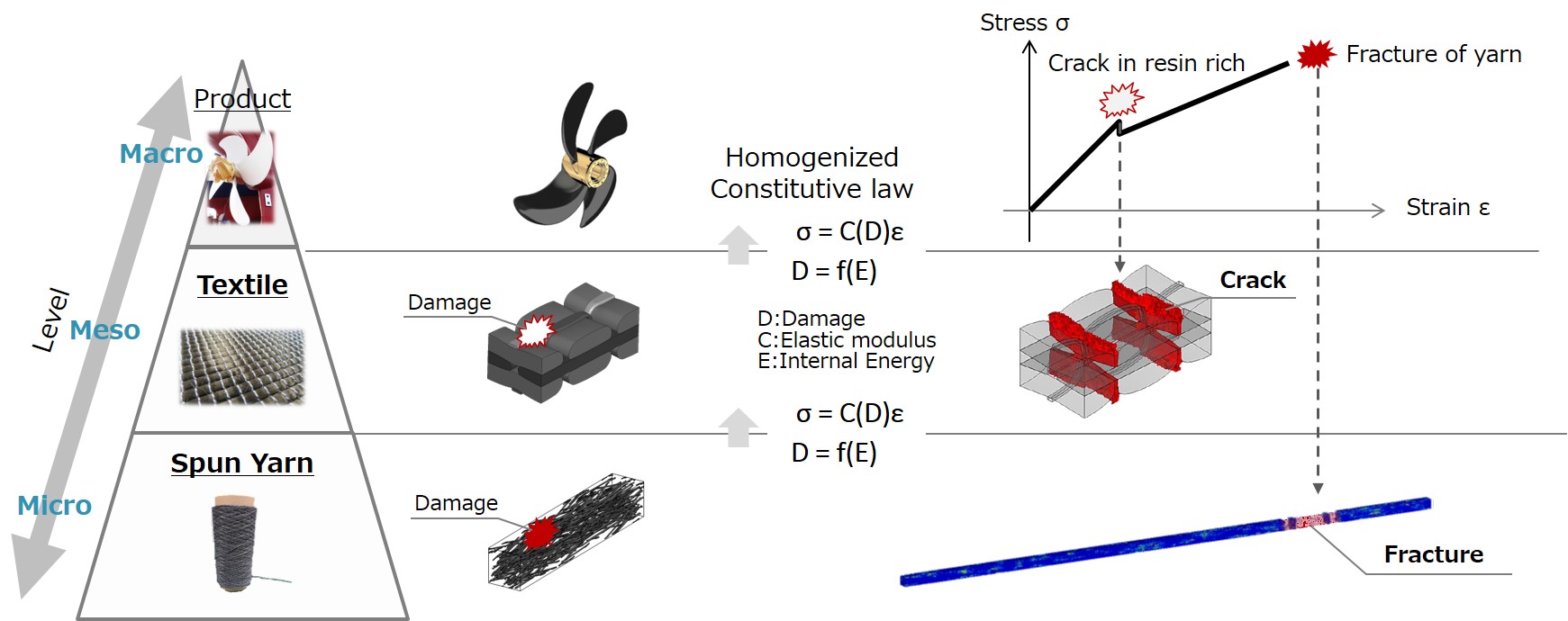
The comprehensive CFRP circulation system will be realized and expanded in three phases (Fig.5).
Phase 1: In-house circulation system
Establish spinning elements using scraps from the CFRP prototype manufacturing process.
Phase 2: Recycling system within the Toyota Group
Use spun yarn recycled from scraps and waste materials from the manufacturing process of high-pressure hydrogen tanks for Toyota Motor Corporation’s FCEVs and internal/external parts to commercialize CFRP parts for automobiles and our products.
Phase 3: Global cross-industrial recycling system
Secure reliable partners and establish commercial distribution in Europe and the United States, the major CFRP markets, to ensure stable quality and production consistency.
Phase 1 has already been completed, and now, in Phase 2, we are developing a heald frame made of recycled CFRP for air-jet looms (Fig.6). By being the first user of the spun yarn product, we plan to demonstrate its reliability to the public and move on to Phase 3. As a model demonstration for Phase 3, we have just started development of a marine propeller made of recycled CFRP for practical use within a few years. To install a new propeller on a ship, it must be approved by the International Bureau of Classification, which inspects the hull structure and propulsion engine in accordance with international conventions and the national laws of the ship’s country of registry to ensure the ship can be safely sailed. By commercializing propellers using recycled CF spun yarn, we hope to gain further trust and achievements in our yarn, significantly accelerating cross-industrialization and globalization of the circulation system.
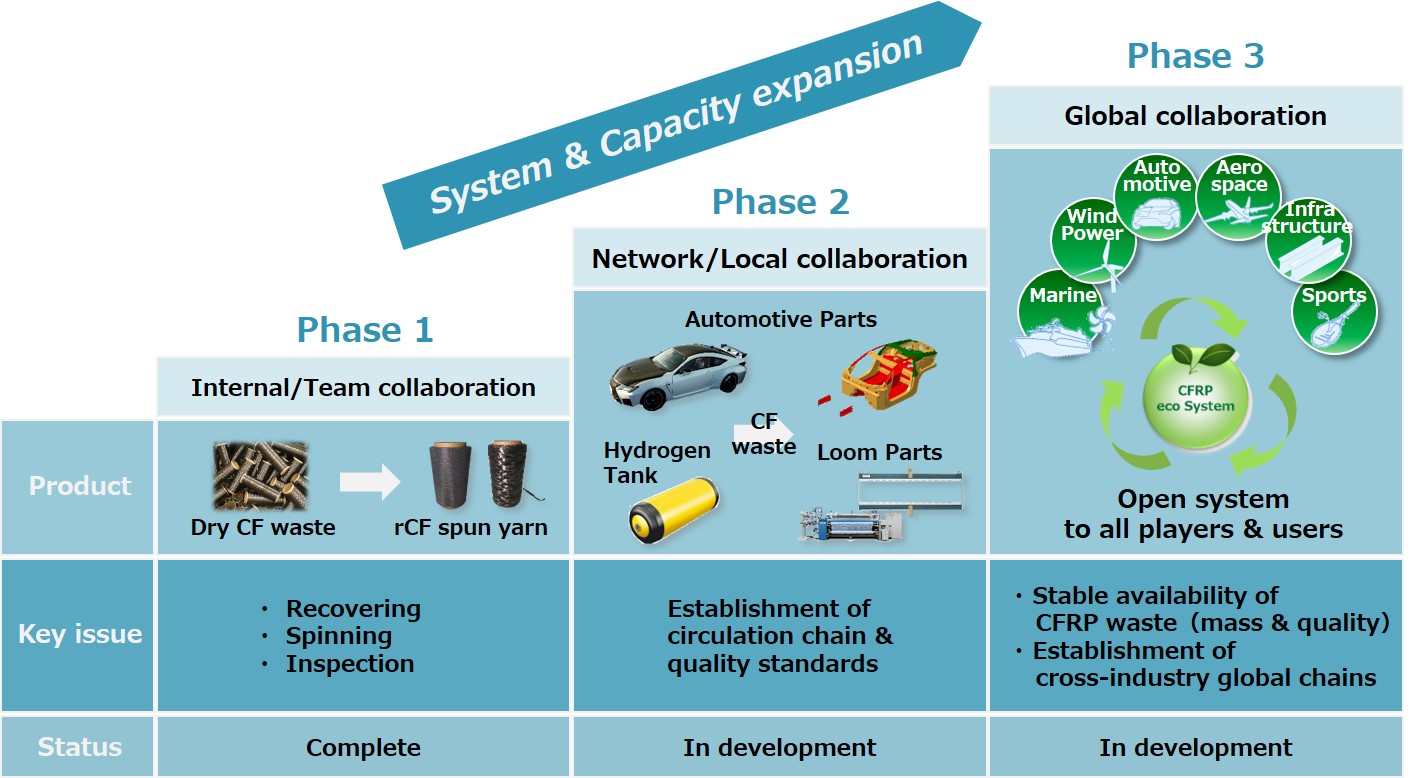
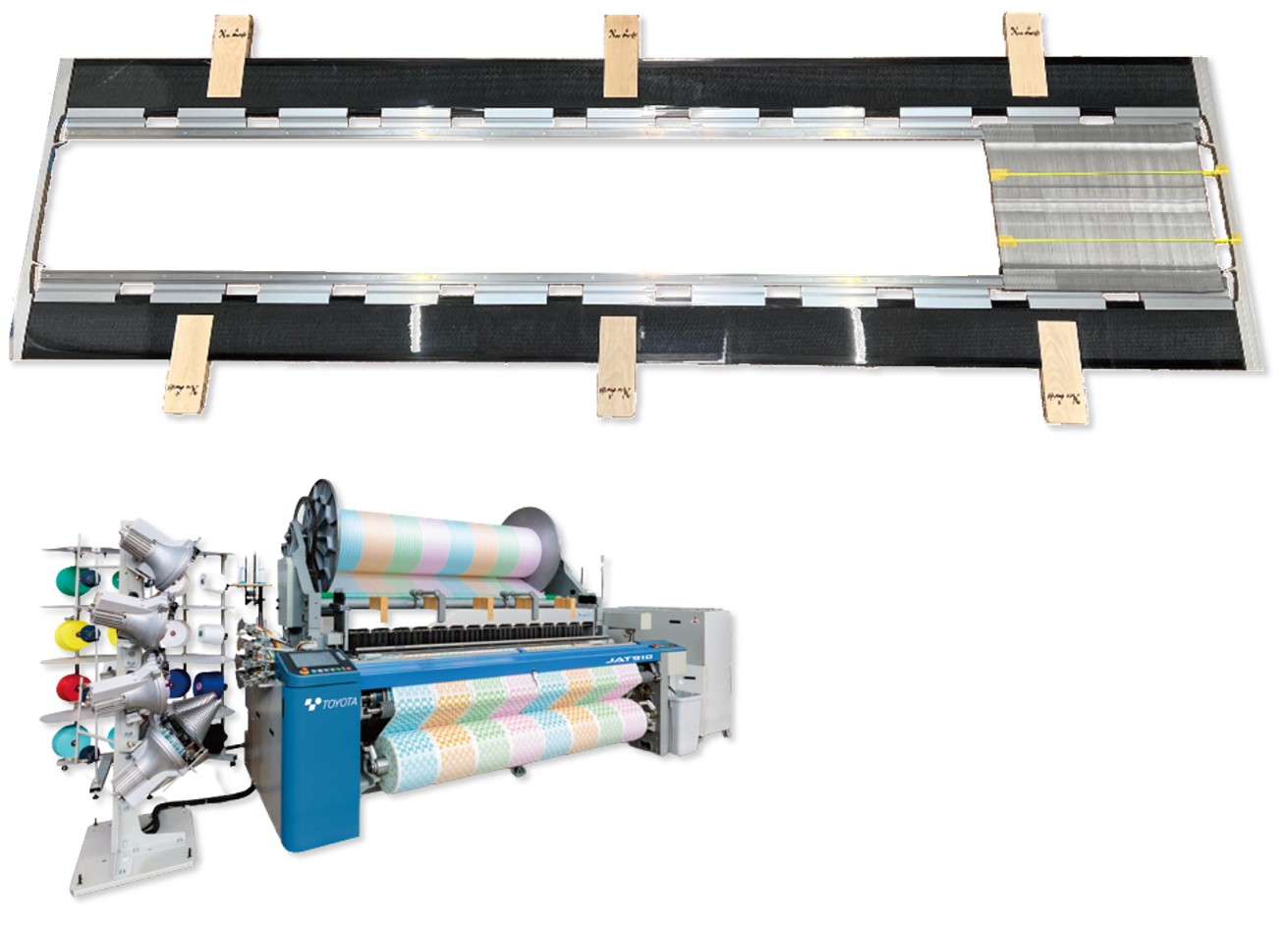
We would like to express our appreciation to Toyota Motor Corporation, USTER Technologies AG, Nakashima Propeller Co., Ltd. Kurimoto, Ltd., Toyota Central R&D Labs., Inc., Nagoya University, Tokai National Higher Education & Research System for their outstanding partnership and collaboration throughout this project. Their expertise and contributions have been instrumental in achieving the success of our study.