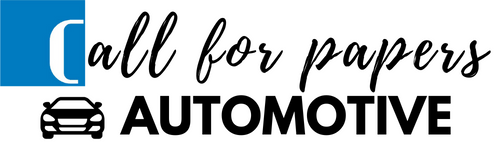
R. Dotoli, A. Gerardi, M. Arganese, F. Fontò – CETMA
G. Savino, D. Cafagna, C. De Luca – Base Protection
The recycling system for industrial waste of carbon fibre prepregs is becoming reality; these are the results at the end of the European project CIRCE (Circular Economy Model for Carbon Fibre Prepregs), developed with collaboration of five Italian companies (HP Composites S.p.A., Alci s.r.l., Base Protection s.r.l., Cetma research and technology organization, Petroceramics S.p.A.) and funded under the LIFE programme.
The partnership between the companies taking part in the research project has shown that prepreg scraps can be reused to produce structural parts as car components, brake disks, toe caps and so on.
The “green” objective is to encourage the reuse of composite materials through the setup of circular economy model proving the validity and structural applicability of the prepreg scraps in different sectors. In addition to the applicability for structural performance, the contribution to sustainable development and cost-effectiveness has also been demonstrated. [1.][2.].
During the cutting process of the prepreg for the realization of a composite component, the quantity of generated scraps ranges from 20% to 50% of the virgin material as shown in Figure 1. This discarded virgin material is typically disposed of in landfills or incinerators because it is considered, so far, not usable. The partners involved in the project have set up an industrial process to select, recover and use 100% of the scraps from the cutting process. At the end of the project, the quantity of uncured thermoset prepreg that a medium company can be able to recover is approximately 10t/year of materials from landfill.
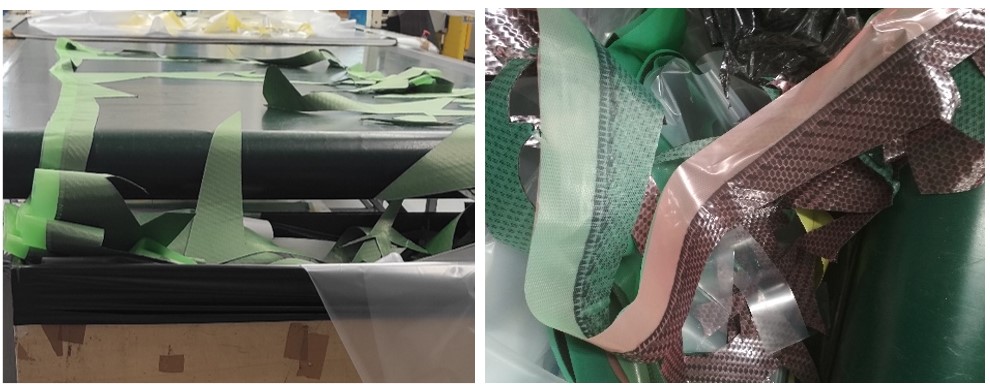
The aim of the project is to fulfil a circular economy model in which, in addition to the selection of the material for the size and shape, it is foreseen its packaging and storage for reintegration into a new production cycle. The estimated costs, which can be further reduced, are about 5-7 €/Kg for the pre-impregnated fabric coming from recycling versus about 20-30€/kg of the same virgin material. The mechanical properties of the composite material realized with recycled prepreg are preserved, remaining structurally comparable to the properties of an aluminium alloy.
The areas of application have been identified with the aim of exploiting the peculiarities of the pre-impregnated fabric, such as the quasi-isotropy in terms of mechanical performance.
Among the structural applications analysed, it was possible to make toe caps for safety footwear replacing completely the traditional material. In particular, Cetma has supported the company Base Protection in the design phase of the new eco-sustainable toe cap by means of experimental numerical approach. Both partners have worked in synergy with the aim of validating and certifying the use of prepreg scraps to produce toe caps for safety footwears.
In the first step, Cetma concentrated on the experimental study of the compression moulding process of the recycled prepreg. The process parameters have been optimized to minimise voids maximizing the mechanical properties of the composite material.
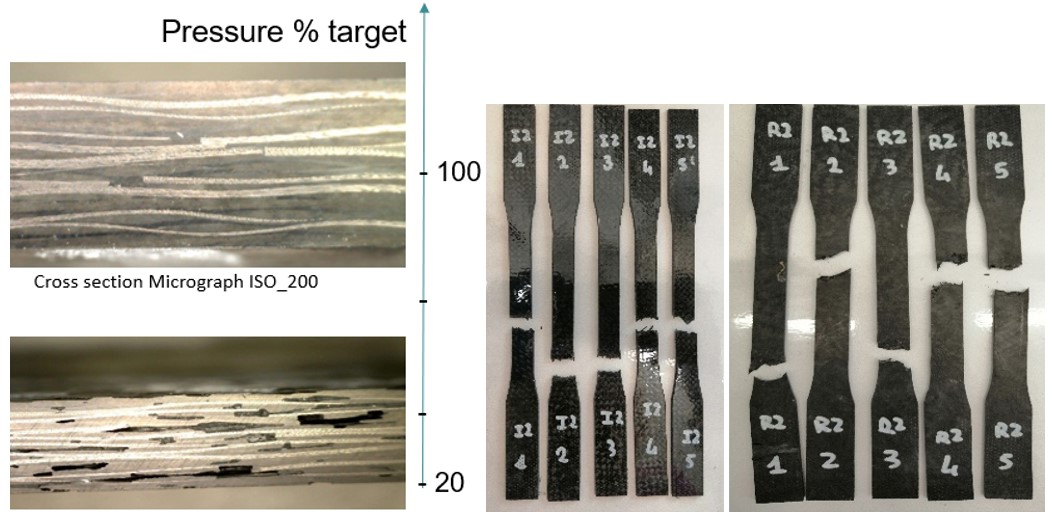
For the design of the toe cap, tensile and impact tests were carried out. The verification of the appropriateness of the recycled prepreg to produce the toecap was carried out using virtual testing and finite elements simulations. The numerical model of the material, applied to the toe cap prototype able to predict the impact performance of the component with 100% recycled material, has been validated. This validated numerical model, see Figure 3, allowed to virtually analyse according to the tests required by the standard, each of the possible geometries proposed.

By means of numerical simulation, Cetma has defined the thickness and the layup of the composite material able to pass the approval test for the toe cap. A structural optimization phase was carried out to improve the design and to reach the best fit between the toe cap and the selected safety footwear. The results of the virtual tests allowed the final geometry to be designed and the mould fabrication stage started.

Therefore, the focus of activities has been addressed to design and manufacture of the mould to produce the prototypes by compression moulding. The prototypes were processed and manufactured by Cetma’s materials and process laboratory according to the parameters and stratification previously identified.
The final activity was the validation of the toe cap model according to UNI standard test; prototypes were tested in the laboratory of Base Protection to verify the structural behaviour of the physical toe cap obtained from scraps of carbon fibre fabrics.
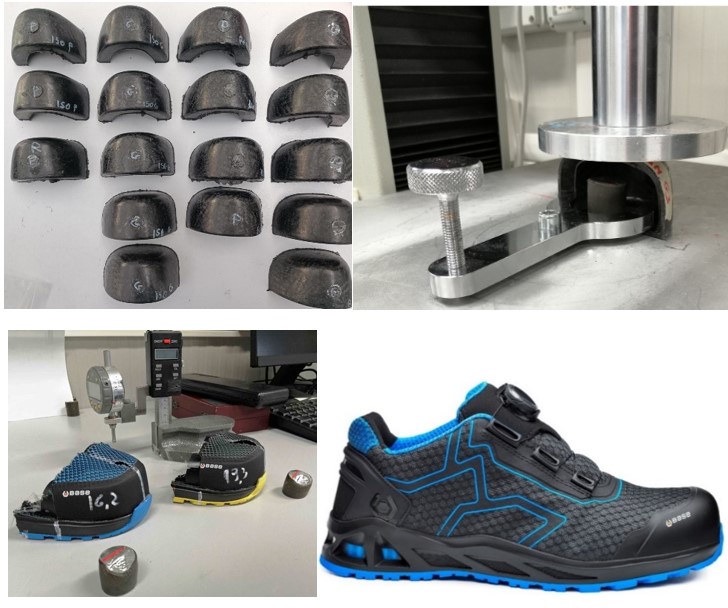
The results of the laboratory tests confirmed the resistance to the impact of the geometry made with 100% recycled material as predicted by the virtual tests. Base Protection has also produced some final safety footwear samples with the new eco-friendly toe cap mounted, in order to evaluate the performance of the complete Kaptive product. Also in this case, the results have certified the use of the toe cap for safety footwear, the tests have been passed with a margin of about 22% compared to the minimum target required by the Standards. The toe cap designed is suitable for safety shoes.
The process of recycling prepreg scraps has demonstrated the reduction of costs and environmental impact of producing carbon fibre reinforced composites. The full reuse of prepreg scraps has highlighted the prospective for applications where virgin materials can be replaced to minimize waste generation. The decisive phase in the development of components made from recycled prepregs is the design; this step must be carried out considering the specific characteristics of the material, so the numerical-experimental approach proposed by Cetma is certainly important.
The contribution to sustainable development and the new market scenarios for manufacturers of carbon fibre reinforced composite components are clear. Cetma continues to invest on the topic; in fact, two new projects have been started, European one regarding an industrial procedure for the analysis of the resin status of scraps, and another national project where Cetma will equip itself with an automated line for the recycling of prepregs.
Reference
[1.] “Comparative life cycle assessment of safety shoes toe caps manufacturing processes” I. Bianchi, A. Forcellese, M. Simoncini, A. Vita, V. Castorani, D. Cafagna, G. Buccoliero; International Journal of Advanced Manufacturing Technology (2022).
[2.] “Life cycle impact assessment of safety shoes toe caps realized with reclaimed composite materials” I. Bianchi, A. Forcellese, M. Simoncini, A. Vita, V. Castorani, M. Arganese, C. De Luca; Journal of Cleaner Production (2022).