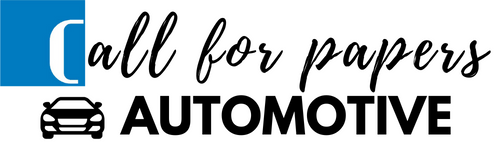
Ana Isabel Crespo, Technologies Manager
Lodovico Agostinis, Synthesis Leader
AIMPLAS, Plastics Technology Centre
The transport sector accounts for more than one-fifth of greenhouse gas emissions in Europe (nota 1) and has become a major target for decarbonisation. Fast-growing transport demand is also expected to generate a sharp increase in emissions if no action is taken (nota 2). Long-term low greenhouse gas emission development strategies are key enabling instruments to reconcile near-to-medium term action with the long-term European goal (nota 3) of becoming climate neutral by 2050 (nota 4). Increased global awareness of and concern about environmental issues such as non-renewable plastics and rapidly depleting fossil fuel reserves have focused attention on more “environmentally friendly and sustainable” products. In this context, environmental legislation is becoming more and more restrictive, and the EU directive (2000/53/EU) on end-of-life vehicles, which is connected to the EU Circular Economy Action Plan (CEAP) (nota 5), highlights the need to improve the economics and quality of biocomposites, which are defined as composite materials in which at least one of the constituents is derived from natural or recycled resources. This calls for more industrial involvement and solution upscaling to develop sustainable products like those addressed in the FOREST project.
The aim of FOREST (advanced lightweight materials FOR Energy-efficient STructures) is to provide new innovative green composites for safe, sustainable transport applications by combining the development of bio-based polymers and additives, recycled fibres with increased resource efficiency and particles to avoid EMI interferences in full alignment with the EU 2030 Climate and Energy Framework (nota 6) (fig.1).
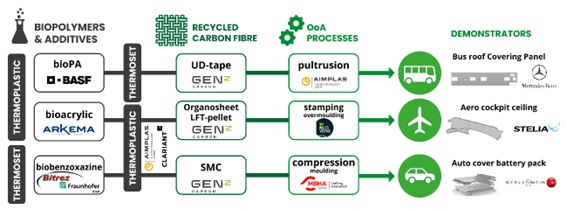
FOREST will spearhead a sustainable strategy for the development of bio-based and recycled materials.
However, one of the main drawbacks of biocomposites is their low fire-retardant properties. This technical article provides an overview of project developments in sustainable flame retardants (FRs).
The global flame retardant market is growing quickly and is expected to reach a CAGR of 8% by 2028 (nota 7). The market includes different types of solutions, the most common of which are inorganic additives such as aluminium trihydroxide (ATH), magnesium hydroxide and antimony oxides. They are added as a powder at around 50-60% w/w. However, these additives have a negative effect on polymer mechanical properties, including impact strength, spinnability and transparency.
An alternative to inorganic additives are halogenated compounds, but their application has been increasingly limited by the European Commission for reasons of toxicity (nota 8). Phosphorus- and nitrogen-based compounds are synergic materials that provide a valuable alternative to halogenated and inorganic flame retardants.
Phosphorus-based flame retardants and their combinations with nitrogen compounds to generate intumescent systems are among the most effective halogen-free solutions created to date and have addition ratios of 20-25% w/w. These flame-retardants may also be of interest for conventional oil-based polymers as an alternative to flame retardants obtained from fossil raw materials. Focus on fossil-based phosphorus as a flame retardant could become a problem for EU industry because it is considered a critical raw material (nota 9). The lack of phosphate rock increases the need to develop alternative bio-based flame retardants to increase Europe competitiveness. Due to the European Commission’s increased restrictions on the use of halogen-based flame retardants since 2002, organophosphate flame retardants (OPFRs) have become one of the most promising alternatives for plastic fireproofing in a wide range of applications.
Phosphorus-based compound 6H-dibenzo[c,e][1,2]oxaphosphinine 6-oxide (DOPO) and its derivatives are considered suitable alternatives to halogenated FRs due to their nontoxic proprieties and versatile flame extinguishing behaviour in the gas and condensed phases. However, modification of DOPO into its derivatives to prepare suitable flame retardant additives such as DOPO-EDA and DOPO-PEPA (fig.2) calls for time-consuming two-step synthesis with a significant toxicity level and environmental impact due to the use of chlorinating agents.
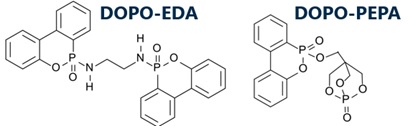
Moreover, dibenzo[d,f][1,3,2]dioxaphosphepine 6-oxide (BPPO) is a phosphonate compound only recently considered a candidate as a phosphorus-based flame retardant. For the most part, its derivatives have been investigated only in the form of PC compounds through phospha-Michael additions and Pudovik reactions to avoid the use of chlorinating agents. However, PC functionalisation is not as effective as the P-N synergic effect in flame retardancy.
AIMPLAS recently patented a new synthetic route to functionalise phosphorus-based compounds such as DOPO (9,10-dihydro-9-oxa-10-phosphaphenanthrene-10-oxide). This new chemical pathway is a one-step synthesis process that takes little time and can be performed without chlorinating agents. The resulting P-N or P-O compounds can be used as additives or included directly in the polymeric matrix, which makes it possible to further reduce the quantity of the FR used and its effects on the final material’s physico-mechanical properties. In the FOREST project, AIMPLAS is studying the development of intrinsically flame retardant resins through the modification of acrylates and benzoxazines with DOPO moiety to be cured in a standard industrial process to produce intrinsically flame retardant composite materials.
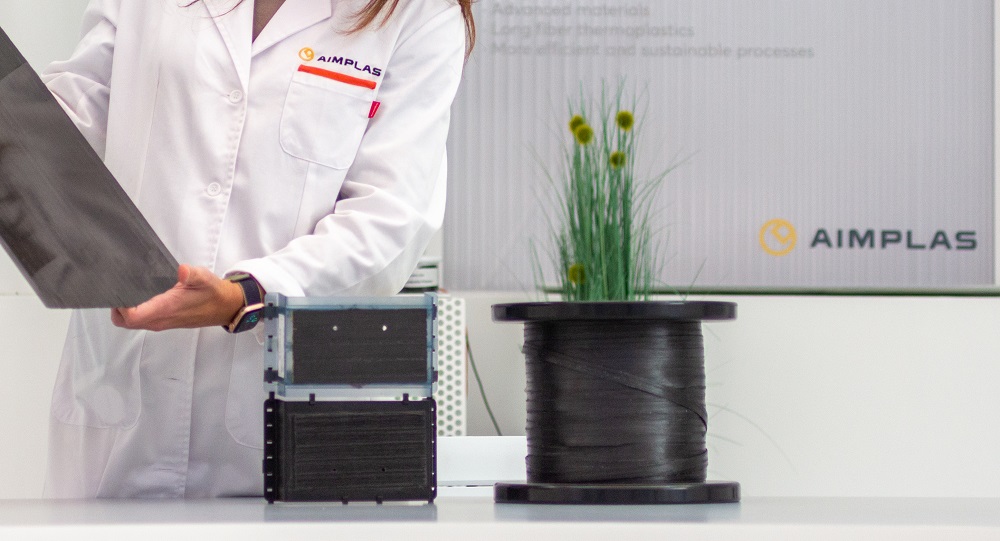
Moreover, the biomass chemical composition includes carbon, hydrogen, nitrogen and phosphorus, which can interact by improving the polymer’s flame-retardant effect. Four main families of compounds are candidates for flame retardant applications: carbohydrates, proteins, lipids and phenolic compounds. In terms of the state of art, some of the compounds of greatest interest are phytic acid from plant seeds (28% of phosphorus in the structure and reactive -OH groups), Chitosan from crustaceans (polysaccharide backbone with -OH and NH2 groups), deoxyribonucleic acid (DNA) (high content of nitrogen and phosphate groups) and phenolic compounds such as lignin and tannins. The basic criteria for selecting the right flame retardant material is (nota 10) thermal stability (the compound’s decomposition temperature must be high enough to withstand polymer processing temperatures), high charring ability, the presence of reactive chemical groups such as hydroxyl, carboxylic acid, amine or double bonds, and the presence of phosphorus, nitrogen or silicon with flame retardant properties. The FOREST project proposes phytic acid and chitosan for the creation of a bio-based flame retardant system. These molecules can create ionic interactions in water solution to produce a polyelectrolyte complex (PEC).
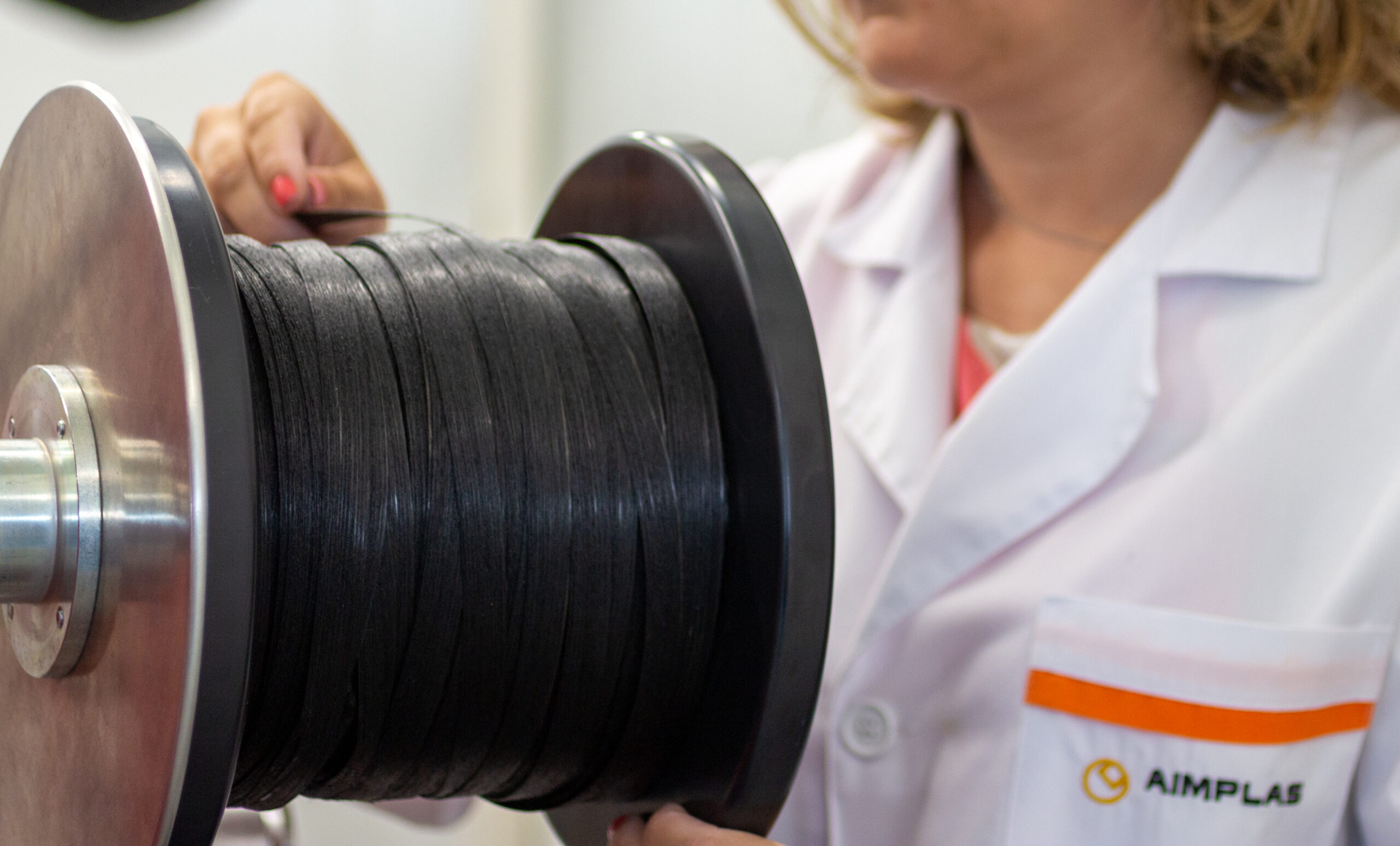
AIMPLAS recently patented a new solvent-free synthesis to produce PEC from chitosan and phytic acid and obtain a bio-based flame retardant material in a scalable, continuous, cost-effective process. Within the framework of the FOREST project, AIMPLAS is studying inclusion of the new bio-based additive in different polymeric matrices to improve the sustainability of the final materials, as well as their safety, by enhancing their fire resistance.
The FOREST project will develop novel lightweight multifunctional biocomposites as a competitive alternative to conventional composites. New chemistries will be developed based on bio-based materials (reactive and non-reactive polymeric system and fire-retardant additive) in combination with fully recycled carbon fibre and EMI particles. The FOREST project framework includes manufacturing and testing 3 prototypes for multifunctional material structures: a bus roof covering panel, an aero cockpit panel and a battery pack cover. In order to meet the transport challenge proposed, Smart, Green and Integrated Transport, an extensive ongoing research study will address the benefits of the biocomposite solutions provided within the FOREST project. Special focus will be put on reducing the environmental impact (efficiency in natural resources, recovery of fibre waste, weight reduction, energy efficiency, suitability for recycling, etc.). Moreover, the specifications will be established for future certification of FOREST biocomposite parts in the bio-based circular economy (BCE).
The FOREST project is funded by the European Union’s Horizon Europe research and innovation programme under Grant Agreement No. 101091790.
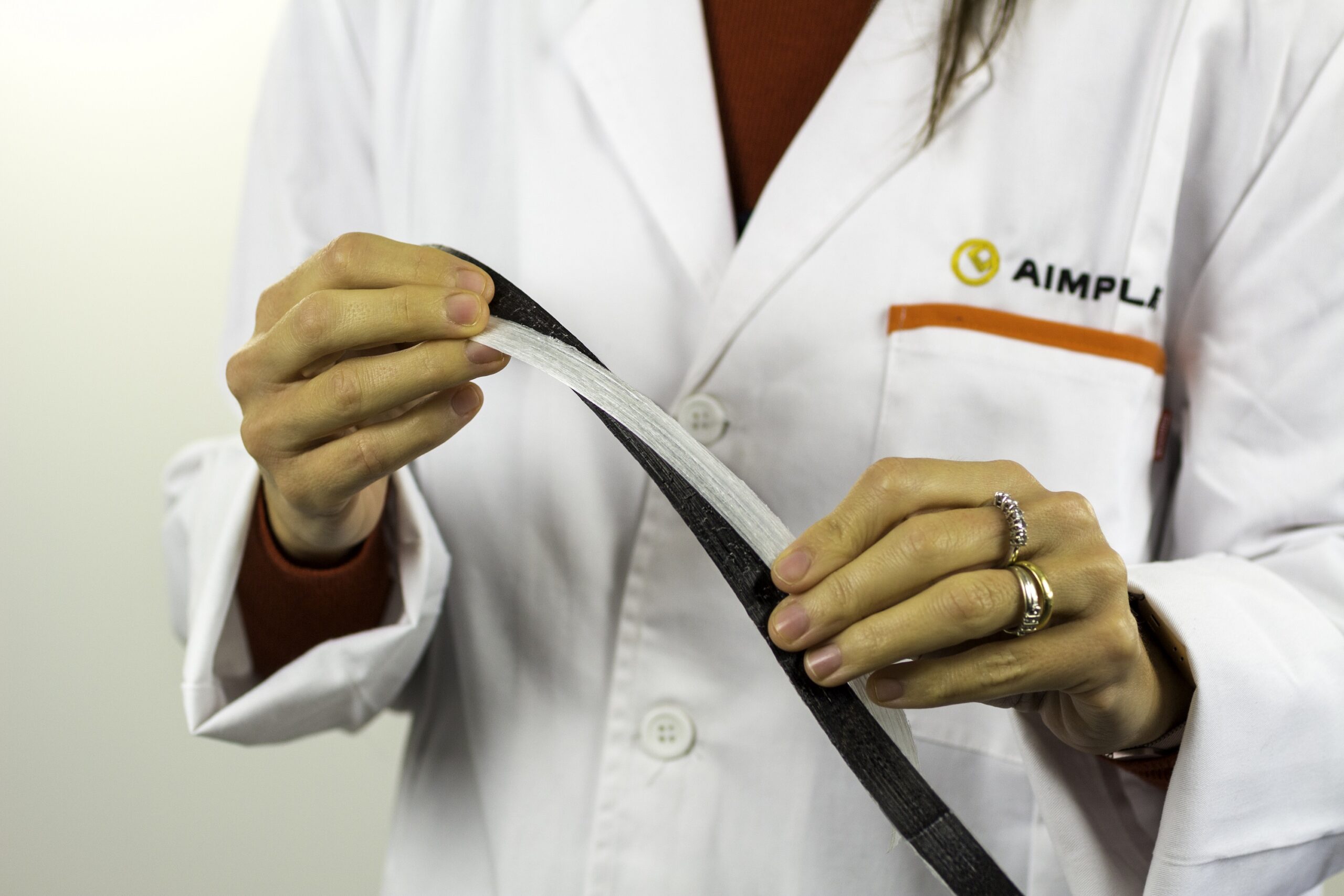
Nota 1: https://www.eea.europa.eu/themes/transport
Nota 3: https://hal.archives-ouvertes.fr/hal-02919192/document
Nota 4: https://www.consilium.europa.eu/en/policies/clean-and-sustainable-mobility/
Nota 5: European Commission, Directorate-General for Communication, Circular Economy Action Plan: the European Green Deal, Publications Office, 2020, https://data.europa.eu/doi/10.2775/855540
Nota 6: https://ec.europa.eu/clima/eu-action/climate-strategies-targets/2030-climate-energy-framework_en
Nota 7: https://www.researchandmarkets.com/reports/3972817/flame-retardant-market-size-share-and-trends
Nota 8: https://echa.europa.eu/documents/10162/2082415/flame_retardants_strategy_en.pdf/
Nota 9: European Commission, 2020, Raw Materials Information System https://rmis.jrc.ec.europa.eu/?page=crm-list-2020-e294f6