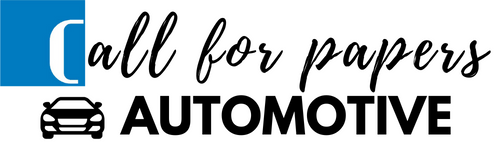
È in aumento la richiesta di componenti compositi e, allo stesso tempo, c’è una maggiore necessità di soluzioni di produzione più efficienti e convenienti. Massivit ha lanciato di recente l’unità 10000 e i suoi mandrini realizzati con produzione additiva sono ideali per formare componenti compositi cavi con superfici interne lisce e regolari. Discuteremo i vantaggi della stampa con materiale frangibile in acqua, così come i possibili risparmi economici.
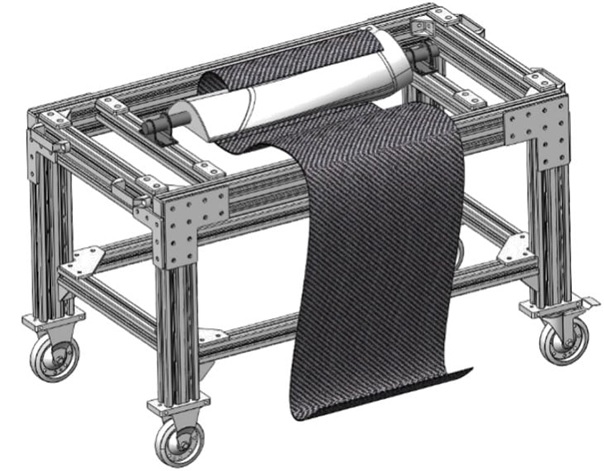
Mandrini e componenti compositi
I mandrini sono attrezzature o dispositivi cilindrici sui quali viene montato il pezzo da lavorare; sono particolarmente utili nella produzione di componenti compositi nella quale fungono da utensili sacrificali attorno a cui viene collocato e indurito il materiale composito prima di rimuovere i mandrini. Sono utilizzati nella produzione di componenti e pezzi tubolari come condutture generiche, telai di biciclette, tubi di scarico e condotti dell’aria per l’edilizia.
I mandrini possono essere realizzati in modi differenti, ma il più comune consiste nell’iniziare con un pezzo cilindrico tagliato alla lunghezza desiderata, il quale viene messo in un tornio e lavorato per ottenere la forma desiderata. In alcuni casi possono essere saldati più pezzi cilindrici per produrre un mandrino di maggiori dimensioni che, una volta lavorato sino alla forma corretta, può essere trattato termicamente per migliorarne la resistenza e la durata.
I tradizionali metodi di produzione dei mandrini sono relativamente problematici poiché richiedono molto tempo e impegno. Il processo è complicato e può essere difficile ottenere mandrini della forma e delle dimensioni esatte. I metodi convenzionali, inoltre, richiedono spesso una notevole quantità di lavoro manuale che può rendere molto lungo il processo e generare difformità tra i mandrini.
Vantaggi della stampa 3D
Massivit ha sviluppato un processo di stampa proprietario per la produzione di mandrini leggeri ma al tempo stesso resistenti e duraturi. Si tratta di una soluzione estremamente innovativa per la produzione di componenti compositi, che offre significativi vantaggi rispetto ai metodi tradizionali e che permette di produrre componenti compositi di qualità elevata riducendo i costi e i tempi di consegna.
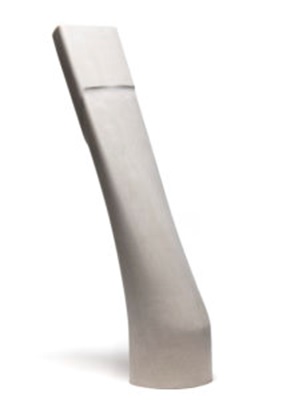
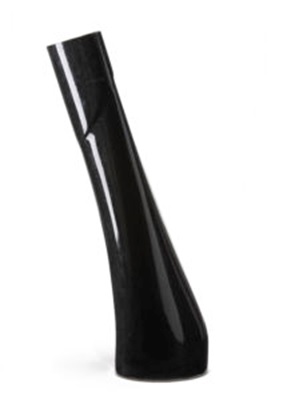
Uno dei principali vantaggi della stampa 3D o della produzione additiva (Additive Manufacturing – AM) è che, rispetto ai tradizionali metodi di lavorazione, permette di utilizzare design molto più complessi. Con l’AM, non ci sono limitazioni nelle forme geometriche che possono essere prodotte: in pratica, i mandrini possono essere realizzati con design della massima complessità. Inoltre, possiamo utilizzare l’AM per produrre mandrini con materiali che i metodi tradizionali non possono lavorare, o possono farlo con estrema difficoltà. Questo schiude un’intera gamma di nuove possibilità nel design dei mandrini e, di conseguenza, è possibile realizzarli su misura in base alle specifiche esigenze di una particolare applicazione.
In più, nella produzione tradizionale può essere necessario assemblare più componenti per ottenere la forma finale del mandrino; con la produzione additiva, invece, si realizza un’unica struttura monolitica, risparmiando tempo e denaro.
Massivit 10000
I mandrini possono essere creati digitalmente con il sistema Massivit 10000 AM, una stampante 3D di livello industriale per la produzione rapida ed efficiente di mandrini, stampi e utensili di grandi dimensioni. La macchina utilizza la tecnologia proprietaria CIM (Cast In Motion) e il metodo di erogazione del gel GDP (Gel Dispensing Printing) brevettato da Massivit, che permette di effettuare la colata dello stampo direttamente in un involucro stampato in 3D.
Per conseguire questo risultato, Massivit 10000 utilizza un sistema a due testine e una tecnologia velocissima brevettata; per i mandrini, utilizza materiale frangibile in acqua che si destruttura una volta immerso nel liquido. In questo modo, i produttori riescono a realizzare mandrini complessi in pochi giorni, invece che in settimane.
Materiale frangibile in acqua
Il fulcro del processo Massivit per la costruzione di mandrini con l’AM è il materiale frangibile in acqua, che si presta perfettamente a questo tipo di produzione. Questo si sbriciola senza disciogliersi, lasciando l’acqua incontaminata e pronta per essere riutilizzata. In questo modo, una volta terminata la produzione il mandrino è facilmente rimovibile dal prodotto finale; di conseguenza, anche la sformatura è molto veloce.
Inoltre, il materiale è leggero (facilmente gestibile e trasportabile durante il processo di produzione), resistente e duraturo (può essere utilizzato per una vasta gamma di applicazioni con i mandrini), facile da usare (è facilmente sagomabile nella forma e nelle dimensioni desiderate del mandrino), ecologico (non rilascia nell’ambiente sostanze chimiche pericolose o inquinanti) e veloce, dato che i mandrini sono stampati in poche ore.
E in più, non è un problema garantire l’alta qualità delle superfici interne di questi complessi componenti cavi. È possibile realizzare superfici interne eccezionalmente lisce e regolari per componenti come i condotti dell’aria.
Un’autentica rivoluzione
I mandrini realizzati con l’AM, e più in particolare con Massivit 10000, hanno il potenziale per rivoluzionare il modo di produrre componenti e pezzi compositi. I mandrini prodotti con l’AM offrono numerosi vantaggi rispetto a quelli prodotti con i metodi tradizionali. Sono più leggeri, più precisi e possono essere personalizzati per soddisfare le specifiche esigenze di ogni componente. Tutto questo garantisce tempi di produzione più rapidi e una riduzione degli scarti. Inoltre, i mandrini realizzati con l’AM possono essere prodotti con materiali avanzati che sono più resistenti, durano di più e sono in grado di resistere a temperature più alte; inoltre, la frangibilità in acqua semplifica la rimozione.
Ciò permette di produrre componenti compositi di maggiore qualità, più affidabili e di maggiore durata. Per la produzione di componenti compositi si prospetta un futuro roseo grazie all’avvento della produzione additiva di mandrini, una tecnologia pronta a rivoluzionare l’industria.