AVK, realtà tedesca di Francoforte, ha annunciato i vincitori dei suoi tre prestigiosi premi di innovazione alle istituzioni, alle aziende e ai loro partner. Tutte le organizzazioni partecipanti hanno presentato eccezionali innovazioni nel settore dei compositi rinforzati con fibre. I premi sono stati presentati durante il 3 ° Congresso Internazionale dei Compositi, il 18 settembre e il 19 settembre presso il Centro Congressi Internazionale di Stoccarda. I vincitori del premio hanno presentato le loro innovazioni al pubblico internazionale durante la fiera. Il Dottor Elmar Witten, amministratore delegato della AVK, si è detto soddisfatto del numero e della qualità dei contributi apportati: “Ogni anno siamo stupiti dal livello di innovazione dimostrato dai dipartimenti di ricerca e sviluppo all’interno delle aziende e delle istituzioni nel nostro settore. Questi dipartimenti stanno contribuendo significativamente al raggiungimento di una maggiore sostenibilità ed efficienza”. Quest’anno la giuria di esperti leader del settore ha selezionato i seguenti vincitori:
– Nella categoria “Prodotti e applicazioni innovative”: BASF SE, in partnership con l’azienda portoghese Sonae Arauco, per la stampa 3D MDF.
– Nella categoria “Processi innovativi”: Audi AG, in partnership con l’azienda austriaca Secar Technology, per una combinazione del processo di fibra continua e del processo di stampaggio a fibra corta per la produzione di componenti esclusivi CRP.
– Nella categoria “Scienza e Ricerca”: il Centro per la produzione leggera integrata (AZL), presso l’Università di Aquisgrana (RWTH), e le sue società partner, per il processo fotonico di produzione di componenti ibridi termoindurenti e termoplastici funzionalmente integrati nell’ automotive.
Quest’ultimo porta avanti dal 2014 uno studio sulla capacità di combinare componenti ibridi termoindurenti e termoplastici, utilizzando una tecnica adatta per la produzione di automobili di grandi dimensioni. La catena di processo sviluppata dalle aziende partner consente di produrre componenti in plastica ibrida continua e in fibra rinforzata per il settore automobilistico. L’innovazione consiste nella comprensione delle complesse interazioni esistenti tra le varie parti del sistema, dei processi e dei loro parametri, nonché dello sviluppo della soluzione integrativa finale. La capacità di combinare diverse materie plastiche in un componente unico apre nuove possibilità e scenari per adattare le proprietà in modo più efficace ai requisiti di una specifica area di applicazione, per esempio quella dei singoli componenti del corpo auto. L’intera catena di processo è, così, integrata in una singola cellula di produzione basata su una macchina per stampaggio ad iniezione. I risparmi potenziali nei costi dei singoli materiali e nei costi operativi dell’intero processo ammontano a circa il 20 per cento del totale. Questa nuova tecnologia può essere usata per svariati altri settori. Oltre alle applicazioni nel settore automobilistico, infatti, la tecnologia è anche adatta per la produzione di componenti per altri settori, ad esempio quello dell’ingegneria meccanica, della costruzione di impianti e delle tecnologie energetiche e ambientali.
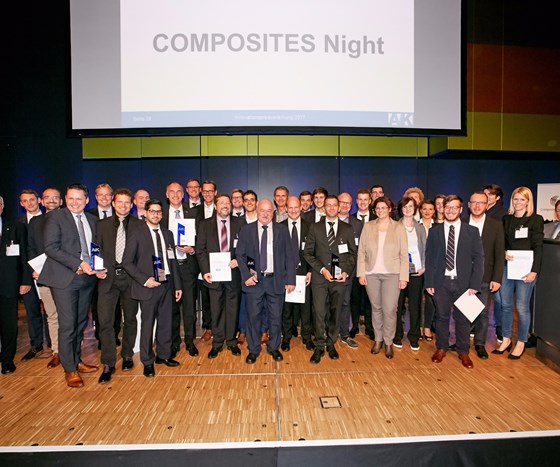