Tra gli obiettivi del reparto compositi del Dynamis PRC per la vettura del 2022 c’è quello di riprogettare l’Impact Attenuator (IA), ovvero la struttura di assorbimento degli impatti frontali da posizionare davanti alla macchina, appena dietro il musetto. È una struttura di fondamentale importanza perché permette di assorbire l’energia derivante da impatti. In particolare, questo componente deve essere in grado di fermare una massa di 300 kg che viaggia a 7 m/s, mantenendo una decelerazione controllata, il cui picco deve essere inferiore ai 40 g e la media minore ai 20 g.
La struttura standard fornita dall’organizzazione della Formula Student è un parallelepipedo delle dimensioni minime dell’IA, imposte dal regolamento, ed è realizzato in Honeycomb, un alveolare di alluminio che assorbe energia per deformazione plastica. La nostra sfida è stata quella di sviluppare una struttura sostitutiva in materiale composito con l’obiettivo di:
- minimizzare il peso
- arrivare nel tempo alla sostituzione dell’IA con un musetto che funzioni anche da struttura attenuatrice d’impatto
La progettazione è nata dall’idea di usare quattro tubi di fibra di carbonio come struttura di assorbimento, ma il regolamento richiede una sezione chiusa dell’Impact Attenuator. Abbiamo quindi pensato di:
- mantenere la forma di semi-tubo, che è adatta ad assorbire energia in maniera più stabile
- incorporare i semi-tubi all’interno di una struttura a sezione quadrata (figura 1).
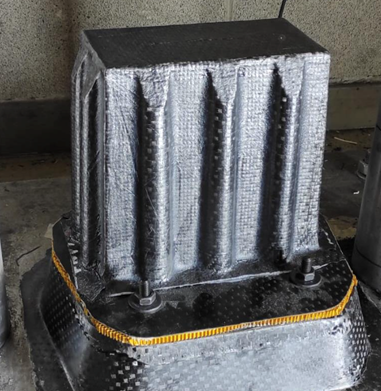
La struttura finale prevede quindi tre semi-tubi su ogni lato lungo (200 mm) e due su ogni lato corto (100 mm).
Sfruttando questa struttura di collegamento tra i semi-tubi siamo riusciti a ottenere una maggiore stabilità in modo che i tubi rimangano in posizione durante l’impatto e sia possibile fornire una buona performance anche in caso di impatto non perfettamente frontale.
Stabilita la forma geometrica dell’IA, abbiamo dovuto definire la laminazione. Il principale obiettivo è stato evitare una rottura della struttura nella zona più vicina alla base, dove gli sforzi si intensificano, producendo un collasso complessivo e un risultato fallimentare. Pertanto, abbiamo realizzato una laminazione progressiva in cui rigidezza e numero di pelli aumentassero dalla parte frontale (la prima a impattare) fino alla parte più vicina al supporto.
Per assicurarci che non ci fossero instabilità e non si staccassero delle zone ancora intere di materiale abbiamo eseguito analisi a elementi finiti (FEM), anche variando il numero di pelli di carbonio. Nelle analisi FEM esplicite eseguite abbiamo modellato la massa impattante come una lastra rigida con delle proprietà di massa di 300 kg e una velocità iniziale imposta di 7 m/s come nel test reale. Nella figura 2 si può vedere un confronto tra l’immagine della simulazione eseguita e il vero crash test. Da queste analisi abbiamo sviluppato una sequenza di laminazione sfruttando la fibra di carbonio a tessuto in tutta la struttura con rinforzi locali in unidirezionale.
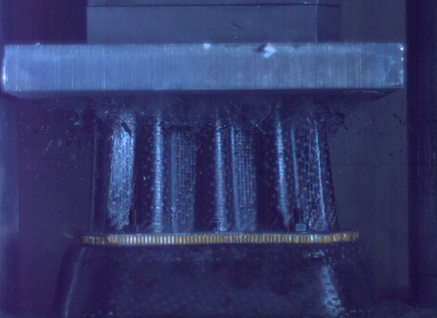
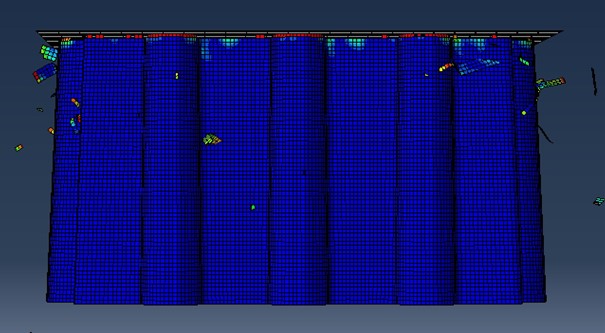
I risultati della simulazione sono stati sufficientemente attinenti a quelli reali. In particolare, la parte frontale e la zona iniziale con laminazione più leggera e maggiore inclinazione hanno dimostrato un comportamento più fragile con un distacco completo senza grande assorbimento di energia. Il vero e proprio assorbimento di energia inizia dopo circa 30 mm con una progressiva intensificazione.
Parallelamente al modello FEM, abbiamo sviluppato un modello analitico che tiene conto dell’energia assorbita per unità di massa così da poter calcolare il numero di pelli di carbonio e l’energia assorbita. I valori di energia sono stati ricavati da una serie di test sperimentali (figura 3) di compressione quasi-statica di tubi di fibra di carbonio.
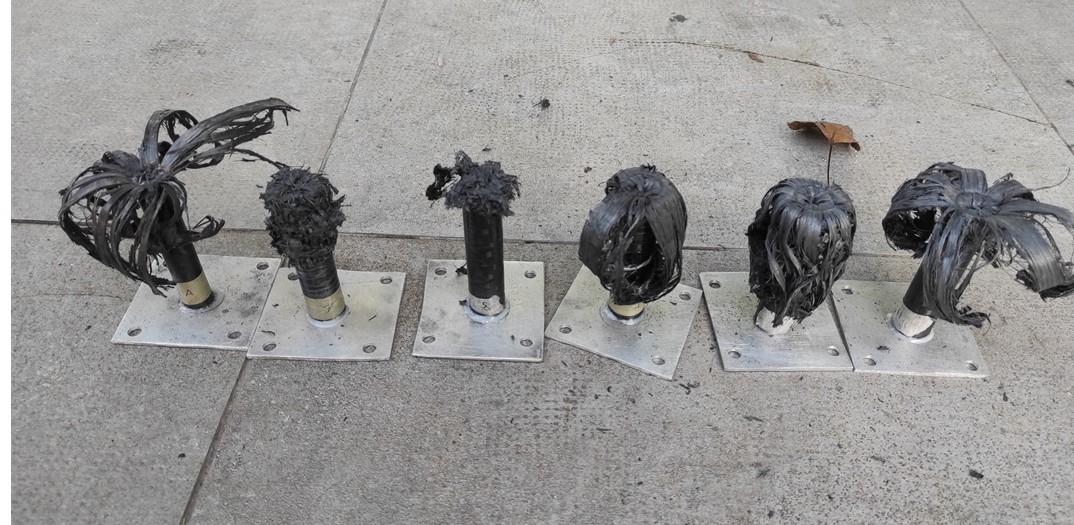
Oltre al modello analitico e numerico, per concludere la progettazione abbiamo eseguito dei test sperimentali ad impatto per selezionare la migliore di due versioni sviluppate e per realizzare il test richiesto dal regolamento della competizione. In questo caso abbiamo usato una massa di 306 kg ad una velocità di 7.2 m/s. Rispetto ai test quasi-statici il valore di energia assorbita è stato simile e leggermente superiore, ma le instabilità sono state più accentuate. Inoltre, rispetto alle simulazioni la lunghezza sfruttata per assorbire energia è stata inferiore: questo perché la struttura sottostante di supporto, richiesta dal regolamento e composta da un pannello in composito che collega l’IA alla monoscocca e dai primi 50 mm del telaio, hanno assorbito una parte dell’energia. Come nella simulazione numerica si può vedere dalla figura 4 che la zona frontale si è staccata interamente.

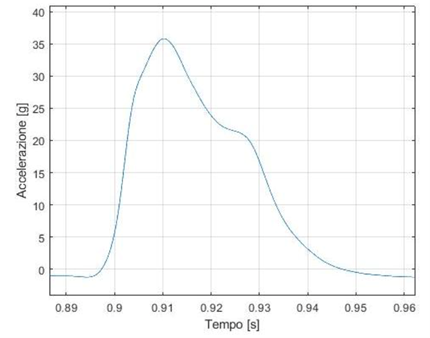
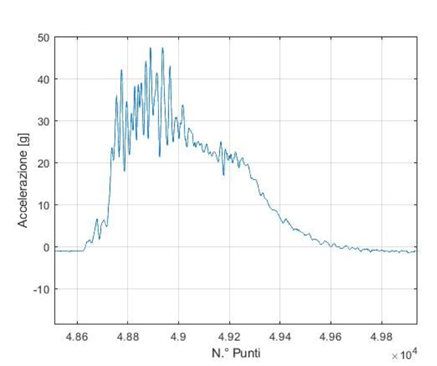
A conclusione del progetto siamo rimasti soddisfatti dei risultati ottenuti dallo sviluppo del primo Impact Attenuator in materiale composito. Ci sono margini di miglioramento per la prossima stagione, specialmente per ridurre ancora la massa e aumentare la lunghezza sfruttata per l’assorbimento di energia vero e proprio. Inoltre, riducendo la rigidezza dell’IA diminuirebbero le decelerazioni medie e la forza scambiata con il resto della struttura che può essere quindi ulteriormente alleggerita.
[Articolo a cura di Giovanni Gigliotti, Lucia Meregalli]