Take a minimal design that merges elegance and sports performance and add innovation and thirty years’ experience of Bucci Composites, leader in the design, development and manufacturing of structural and aesthetic components in composite materials for the automotive, aerospace, industrial and marine sectors.
This is the winning recipe that has led to the completion of a 22” full carbon wheel rim with features unlike any currently found on the market.
The omologation process
After years of development, in conjunction with a prestigious world-class OEM, the Bucci Composites wheel has finished the rigorous TÜV (Technischer Überwachungsverein/Technical Inspection Association) test procedure. This made the product one step closer to its imminent market launch.
No carbon fibre wheel rim manufacturer had ever managed to complete the programme of the renowned German testing organisation. For this reason the omologation process enables Bucci Composites to set a new world record.
With safety guaranteed, the Made in Italy wheel sets the benchmark in the carbon fibre rim market.
Not only are the rim’s technical features outstanding, but it also offers an unprecedented driving experience. To verify this, in the final test stage, the wheel was put through its paces on one of the most famous tracks in the world, the Nürburgring.

Compared to the equivalent forged aluminium wheel
The Bucci Composites full composite wheel achieved 6kg weight saving per corner. This appreciably improved steering agility through the significantly reduced rotational inertia and enabled an unparalleled suspension tuning setup with less unsprung mass.
Onboard comfort was also greatly improved, thanks to reduced rim deflection when going round bends and tyre wear was correspondingly reduced.
The innovative manufacturing process
One of the main innovations of this wheel is its manufacturing process, which applies innovative concepts (covered by patents) together with high-pressure resin transfer moulding (HP-RTM) technology. The production materials and parameters were carefully studied by the R&D team to ensure product repeatability and quality.
The optimisation of the process and the high standard of the technology used have led to considerable cost reductions, while still meeting the production rates demanded by the automotive industry.
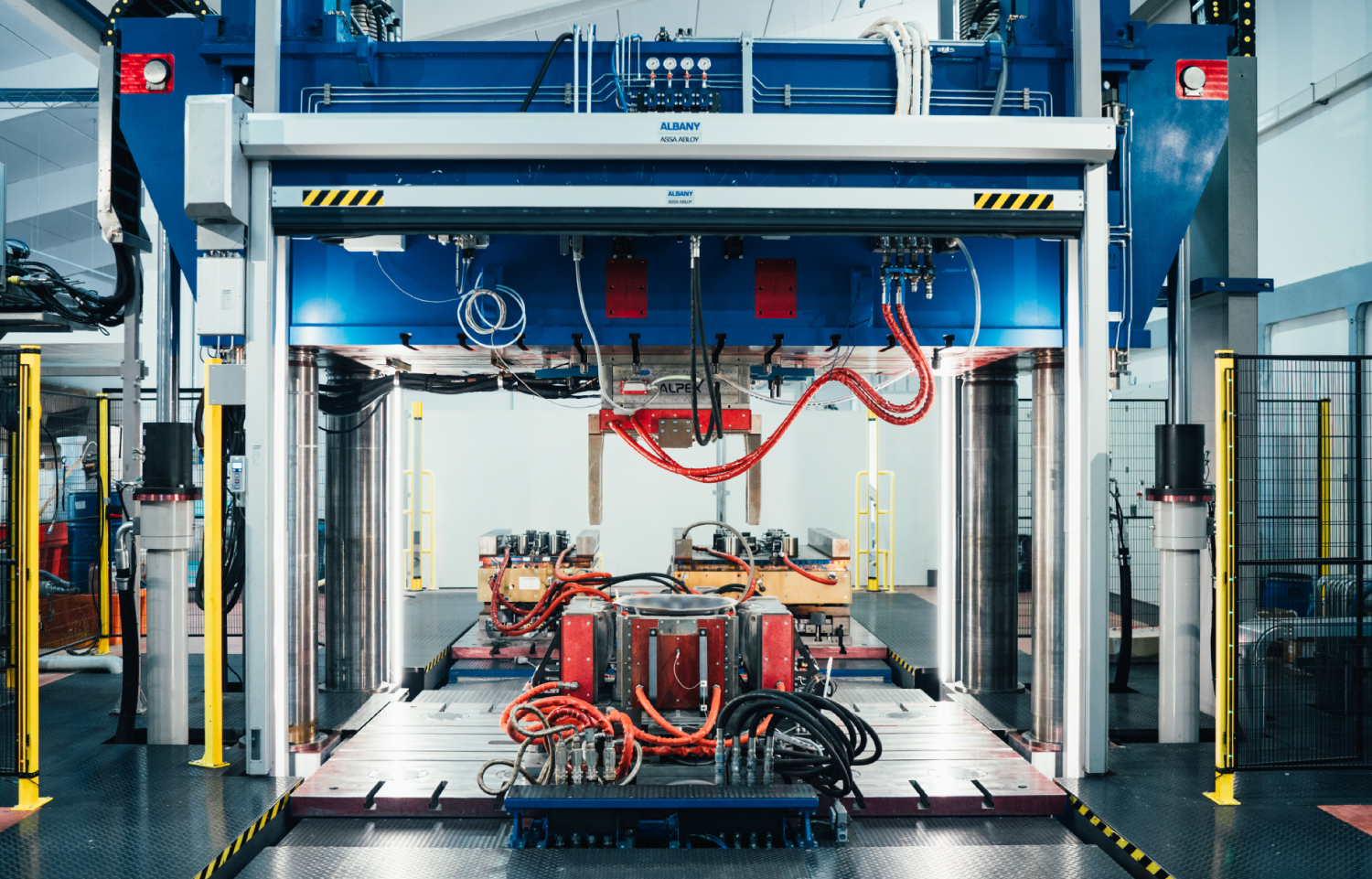
For more details: wheel.bucci-composites.com
![]() |
SUBSCRIBE NOW
|