Carbon-ceramic brake discs are part of a special class of materials called ceramic matrix composites, often abbreviated with the acronym CMC. These innovative discs were born during the 1970s in the aerospace field. Only in the following decade, the first applications for motorsport arrived.
Then, starting from the 2000s, this technology also reached also the sports car sector, enjoying considerable success. The success was so significant that Brembo, a leading company in braking systems, opened a joint venture dedicated to the development and production of carbon-ceramic brake discs.
Nowadays many cars of famous brands such as Lamborghini, Ferrari, Porsche, and Maserati (and many others) are fitted with these latest generation braking systems to meet their performance and design needs.
Not surprisingly, carbon-ceramic discs are characterized by excessive costs that justify their presence only in the exclusive context of luxury sports cars. We must also consider that the production of a disc takes about twenty days because of the high-tech complex production process.
Why choose carbon-ceramic discs
Compared to traditional cast-iron brake discs, CMC ones are lighter in weight by up to 50%. In addition, the ceramic matrix has properties typical of advanced ceramic materials, such as:
- high hardness even at high temperatures
- greater wear resistance
- low deformation at high temperatures
- excellent resistance to corrosion
All these features make CMC brake discs ideal in:
- limiting the effect of fading, that is the loss of effectiveness of the braking system following long or repeated braking
- increasing the useful life of the discs
The last thing to consider, but no less important than the others, is the aesthetics which for luxury cars is often one of the most important elements of the product. The matte black design accompanied by the typical texture of the carbon fibers of these discs is no doubt attractive.
Advantages and disadvantages of ceramic materials
To better understand CMCs, we must first talk about their precursors: ceramic materials. Ceramics are a very broad class of materials, but we can distinguish essentially two main families based on the applications:
- Traditional ceramics that are used in less demanding applications, such as sanitary ware and tableware
- Advanced ceramic materials that are used in applications that require high-level performance. They have many advantages over their metal counterparts, including high hardness and elastic modulus, often even higher than those of steel
However, these materials also have a major flaw: very low fracture toughness values, i.e. the sensitivity of the material to the presence of defects. Materials with low fracture toughness are characterized by a higher chance of fracture, which occurs quickly and without warning. When we have critical elements carbon-ceramic brake discs, we can’t risk running into such this eventuality!
Composite materials with ceramic matrix
Ceramic matrix composite materials are a solution to the limit that advanced ceramics present for structural applications. Carbon-ceramic brake discs are made of a ceramic matrix (usually silicon carbide), and of high-strength carbon or silicon carbide fibers.
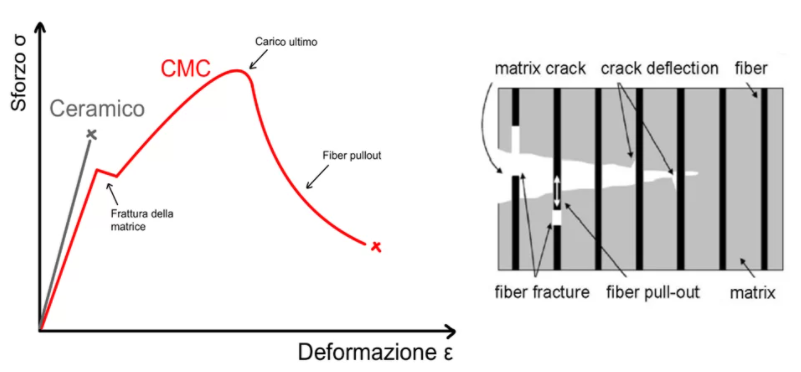
The fibers play an important role in improving the fracture toughness of the material. This one could indeed even reach values greater than 30 MPa m1 / 2 in the case of SiC-SiC CMCs. Not bad if we consider that the toughness of unreinforced silicon carbide is around 3-6 MPa m1 / 2, an improvement of about six times!
CMCs reinforcement mechanisms
The interaction between the fibers and the ceramic matrix makes CMC reinforcement possible. In technical jargon this is called the bridging mechanism. Basically, when the matrix yields under the external load, some microscopic fractures are formed. Normally, under the action of a critical load, these cracks would grow rapidly and without control fracturing a mechanical component.
However, in the presence of the fibers, the crack propagation is slowed down by a series of energy dissipation mechanisms:
- Forcing the branching of the crack along the fibers by previously weakening the fiber-matrix interface with a special coating. This mechanism is called debonding.
- Breaking of the fiber, which requires a significant amount of energy since the fibers have a very high mechanical strength even around 3-4 GPa (in the case of carbon or SiC fibers)
- Fiber pullout, i.e. the complete separation of fiber and matrix against the action of friction.
The final result is a material that combines the high mechanical properties of the ceramic matrix with similar pseudo-ductile behavior to metallic materials.
![]() |
Subscribe now to our quarterly Compositi newsletter
|
Source: Close-up Engineering