James Wilkinson, Carbo-Link
Carbo-Link, ‘sbp schlaich bergermann partner’ and ‘seele’ collaborated on an innovative CFRP cable-net structure for glass façades providing maximum transparency with no visible supporting structure, enabling a clear design language for building envelopes. Utilising high tensile strength and small cross-sections of CFRP tension members, an entire load-bearing cable net structure is prestressed and placed between the joints of individual glass panels to form structural glass ‘walls’ of unlimited size. The system has high corrosion resistance and no part replacement cycle, ensuring zero maintenance demands over near-infinite lifespans, combined with no stress relaxation over time, enabling a constant pre-stress level in the structure.
Description
The CFRP cable net is an evolution of steel glass design façades where the glass ‘wall’ and its supporting structure are two separate components. Combining seele’s innovative glass panels and vast engineering experience, sbp schlaich bergermann partner’s design creativity and vision, and Carbo-Link’s knowledge of structural CFRP solutions has created a new, more efficient and sustainable structural solution for large-scale glass façades.
A cable net glass façade is a pretensioned network of orthogonal loaded cables that impose a façades load into the main building structure. Various nodes attach glass panels to a horizontal and vertical cable-net structure, traditionally made from steel and formed externally. With the CFRP cable net innovation, CFRP tension members replace the traditional steel cable network, allowing full integration into the glass wall. The cable net consists of pultruded CFRP slats bonded into a resin/metallic cone engineered to carry the required tensile load whilst conforming to interface demands and introducing pre-tension load. The CFRP cable cross-sections derive from the pretension load requirements, maximum cable forces, and optimum integration with the glass panels, including surface area considerations for bonding nodes to carry the glass panels, combined with reduced gap widths between. The required cross-sectional area of the tension member was standardised, ensuring economic productivity and reduced overall project cost. The joints between the glass panes are filled with black silicone, encasing the CFRP tension members to protect the structural component and complete the seamless aesthetic whilst transmitting variable loads into the structure and glass panes. In the case of singular panel damage, the silicone joint can be removed, and new glass panels inserted without damaging the CFRP elements.
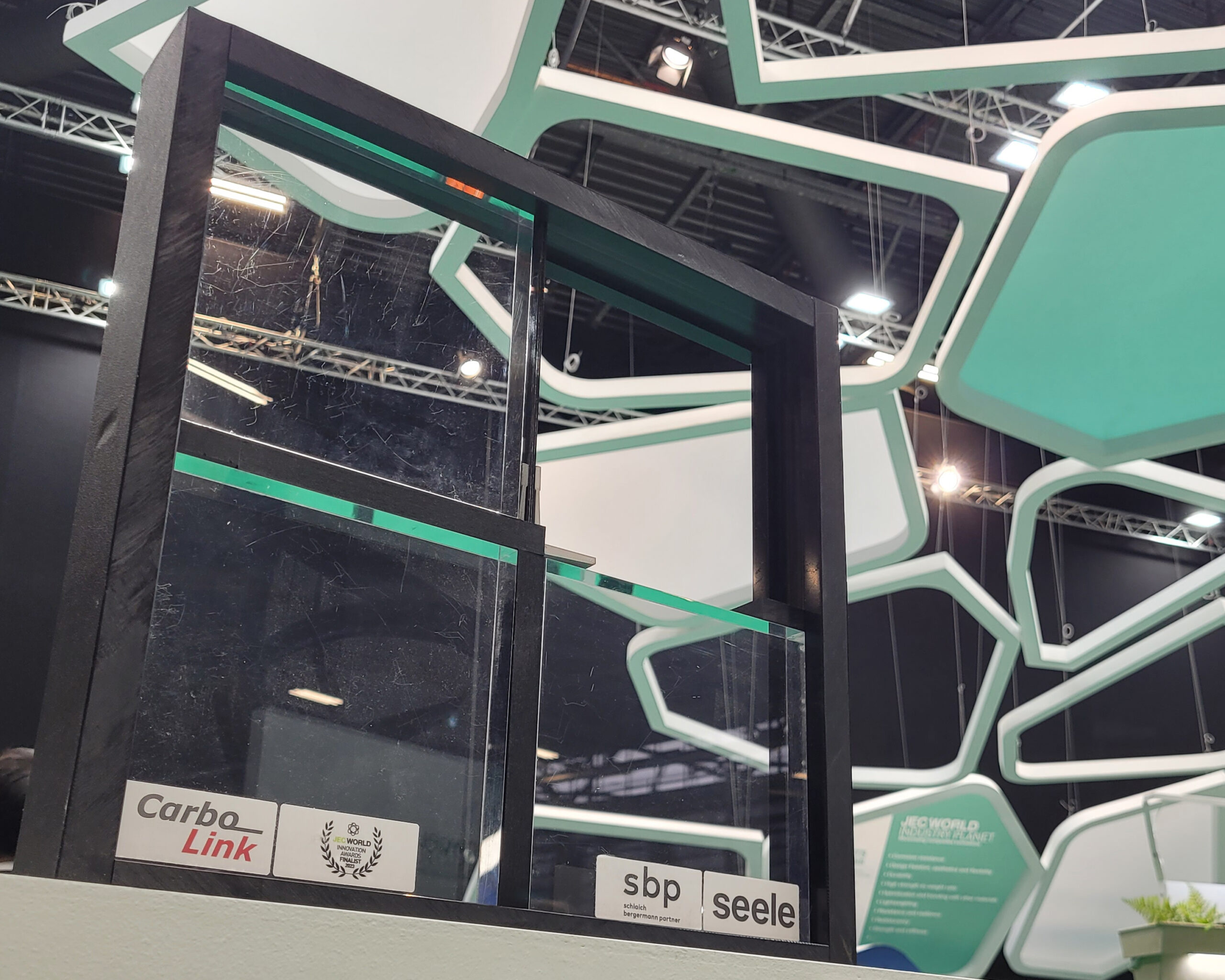
Carbo-Link’s role
Carbo-Link engineered and produced the entire CFRP element, including the lamellas and titanium interface components. All parts are produced at Carbo-Link’s AS9100D Aerospace-certified facility outside Zurich, Switzerland. Carbo-Link were also responsible for in-house load testing of the individual CFRP elements to verify the concept and prove prestressing without relaxation over time or failure. Carbo-Link also conducted ultimate tensile tests to verify design failure loads. Carbo-Link’s CEO and Founder played a critical role in the overall system testing at seele, providing immediate technical feedback and support onsite throughout the verification process.
Value created
Utilising the high tensile strength and small cross-sections of CFRP tension members, the entire load-bearing structure, or net, can be prestressed and placed between the joints of
individual glass instead of a completely separate structural component. Combining the load-bearing structure with the glass reduces build time and raw material requirements, increasing the structure’s sustainability at a reduced cost whilst improving aesthetic appeal and building transparency. In addition, the CFRP cable net has significantly higher tensile stress capacity at densities roughly five times lower than steel, ensuring the optimum balance between the structure’s stiffness and load-bearing capacity at a significantly lower overall weight. A further benefit of this balance is no relaxation under load, allowing the structure to maintain high pretension levels throughout the structure’s lifespan.
CFRP elements are highly resistant to corrosion and environmental influences. Therefore the cable-net structure requires no inspection, service or replacement over the lifespan of the glass facade. No service demands reduce ongoing maintenance costs to zero, increasing the structure’s sustainability through a prolonged active lifespan and no need for energy and cost-intensive human intervention.
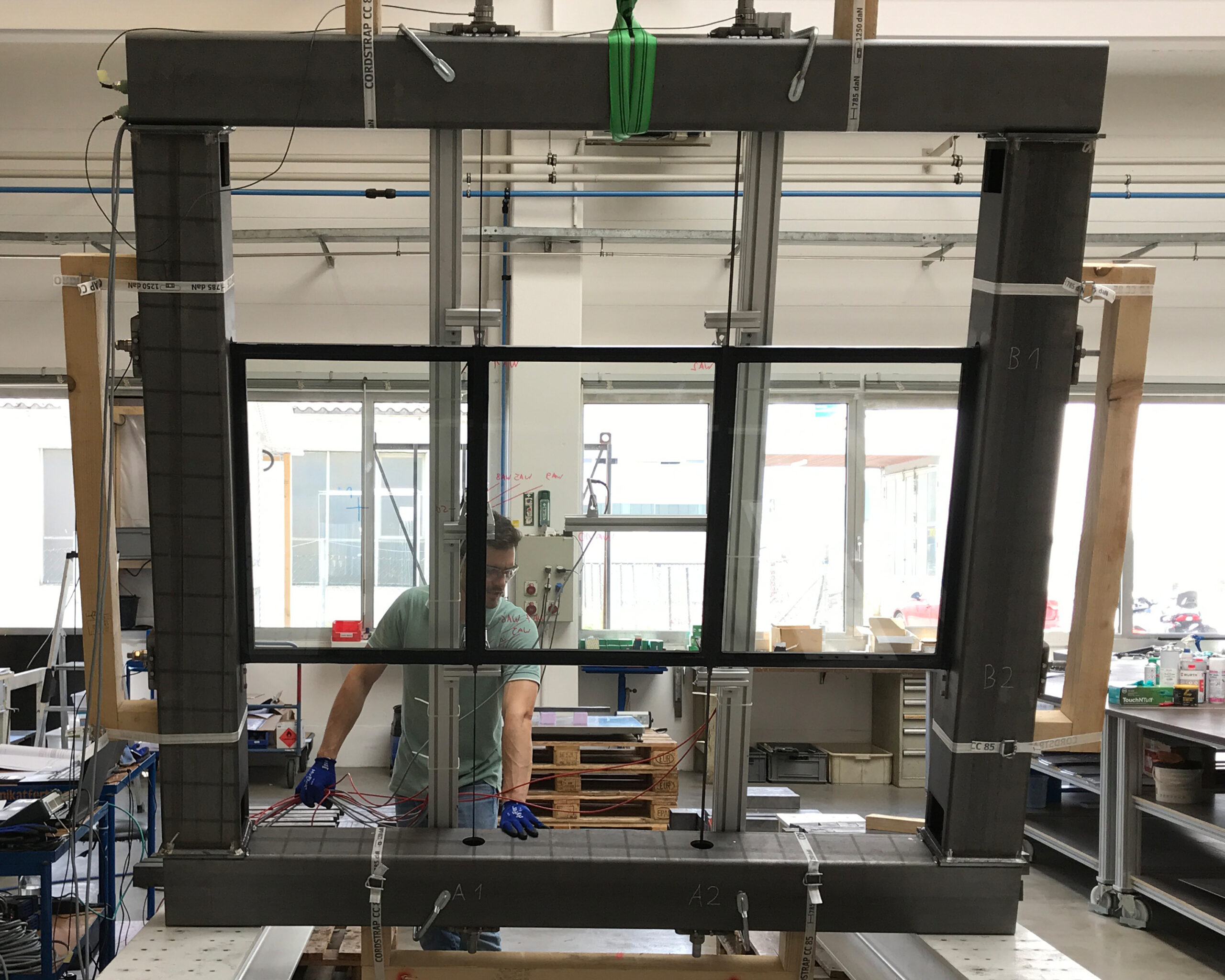
Key benefits
- High tensile strength capacity = increasing ability to carry structural load
- Super lightweight = less superstructure demand at a more extensive project scale
- No relaxation over lifespan = high level of pretension maintained over the life
- No service demands = increased active lifespan, reduced cost of ownership
- Small cross-section = hidden structural components for increased transparency.
Current innovation status
The project pushed the boundaries as far as possible to build a structural and transparent glass façade. The CFRP elements of the system were subjected to individual case approval by the German ZiE authorities. Although still considered a development project, the system is proven, approved (locally), and ready for market roll-out. The system is also patent protected. Under the supervision of Carbo-Link, sbp, and seele, together with the ZiE experts, several tests were executed to verify system critical components. These included the pre-stressing of CFRP elements, surface preparation of CFRP and silicone adhesion to CFRP, energy dissipation of CFRP “cable net” in case of impact load on glass panels, and orthogonal load transfer into the CFRP cables under dynamic loads. In addition, a large-scale mock-up was erected to test and verify the overall FE modelling, the expected load-carrying capacity, and the energy dissipation of the CFRP cable net. All testing was successful, and the ZiE has preliminarily approved the system, whilst several additional long-term tests remain underway for final approval.
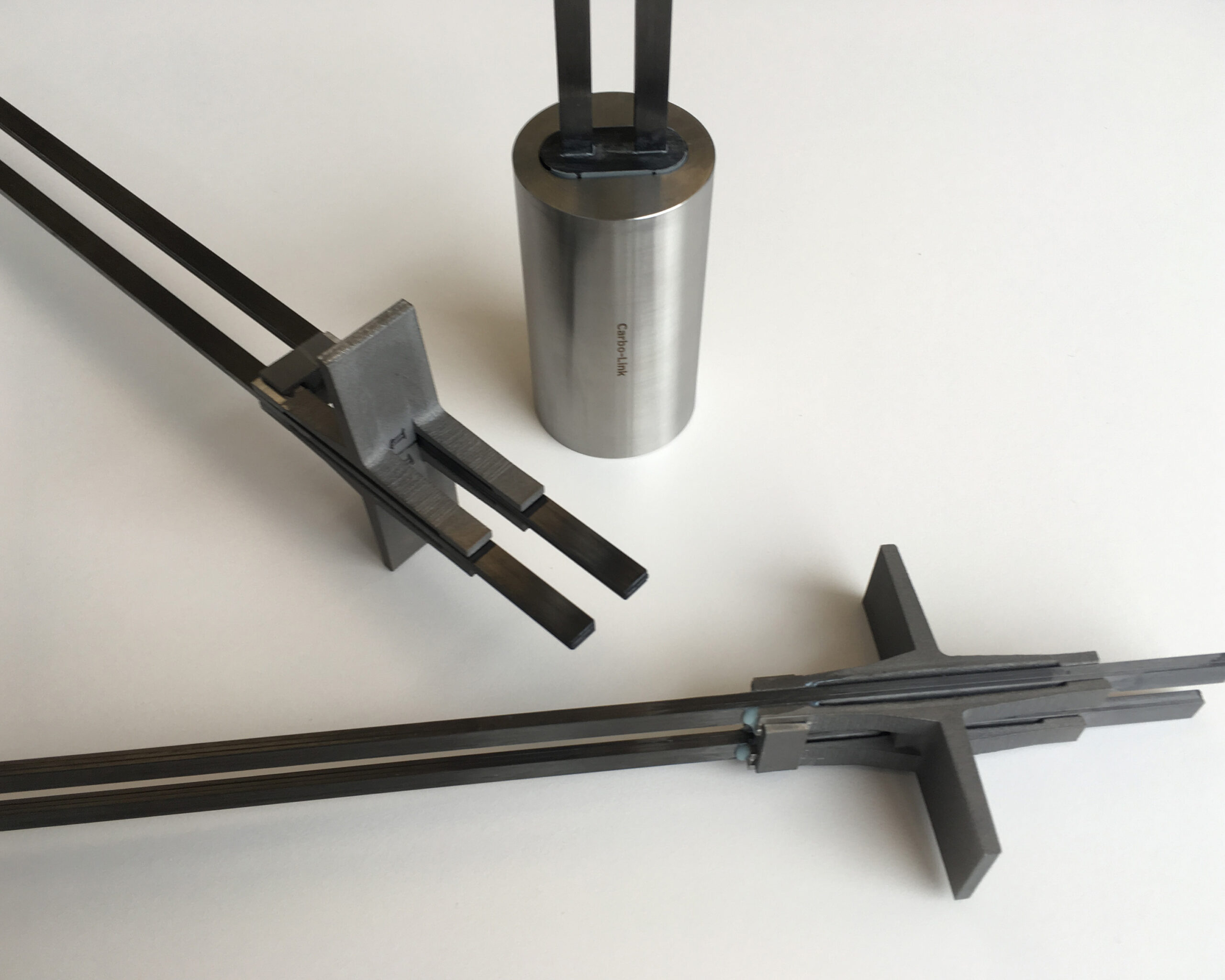
Contribution to the common good
Increasing emphasis on energy efficiency in building infrastructure aligns perfectly with the CFRP cable net glass façade. Driving energy consumption down is achieved during the construction and throughout the active lifecycle stages of any infrastructure utilising this innovation. Starting at the design stage, integrating CFRP elements into the façade significantly reduces weight, consequently reducing the dead load of the building as a whole. Therefore, the amount of concrete and steel superstructure needed is significantly less for the same load-bearing demands than a steel-net façade. This enables a higher percentage of a building envelope to be constructed with glass façades, further increasing the energy efficiency of the building. During the active phase of a building, glass façades, as a result of innovations in glass panel technology, better regulate building temperatures, reducing the energy power consumption needed for cooling or heating the building space. Moreover, the glass façade provides sound insulation to improve the acoustics of the building. The increased transparency afforded by the CFRP cable-net glass façade also contributes to improved user well-being, with increased exposure to natural daylight flowing into all areas exposed to the façade. The durability of the CFRP cable net also significantly contributes to the useability and longevity of infrastructure. The CFRP cable net is the perfect structural component, with minimal inspection requirements, no replacement demands, zero relaxation, and a non-corrosive nature.
Reduced environmental impact
A comparison between a steel and CFRP cable shifts heavily in favour of the CFRP option when an overall system or infrastructure is considered. Implementing lightweight, resilient and highly efficient CFRP cables can significantly reduce the amount of concrete and steel raw materials throughout a superstructure. Improved superstructure efficiency combined with the inherent advantages of CFRP elements results in considerably prolonged lifespans of infrastructure projects, further contributing to positive environmental impacts through longevity. In addition, there is a high savings potential during transport and installation since the lightweight elements can be easily transported, installed and prestressed quickly without fuel and labour-intensive heavy machinery. Comparable life-cycle analyses of the use of CFRP cables in bridge construction have recently shown that overall systems enable CO2 savings of more than 20% from concept to construction and throughout the active life. Today, carbon fibres are almost 100% recyclable and can be reused as 1:1 replacement in the same application or used as nonwovens in other applications. However, since Carbo-Link develops its products according to the premise of “sustainability through durability”, the question of recycling will only arise in many decades after the prolonged cycles reach their planned service life.