Soft materials, such as rubber or polymers that can endure drastic changes to their shape, are promising for applications where flexibility and shapeshifting abilities are paramount.
For example, these materials can be used to create soft robots suited for specialized tasks, ranging from medical devices that could navigate around inside the body to robots for search-and-rescue missions that can squeeze through small openings.
How to cut the connection?
But to power a soft robot’s movement or transformations, researchers often use actuators that need to be physically connected to the robot, which limits its usefulness.
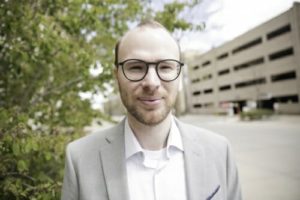
“These actuators are usually much larger than the robot itself,” says Stephan Rudykh, a University of Wisconsin–Madison mechanical engineering professor.
“For example, you might have a huge tank of compressed air that’s attached to the robot by a cable and used to inflate the soft materials and power the robot.”
The effects of magnetic fields on the internal structure of soft composite materials
A team led by Rudykh has devised a way to cut that cord. In a paper published in the journal Physical Review Letters, the researchers demonstrated a method for using magnetic fields to remotely induce soft composite materials to rearrange their internal structure into a variety of new patterns.
“We showed that in a relatively simple system, we could get a very wide spectrum of different patterns that were controlled by the level of the magnetic field, including patterns that would be impossible to achieve by applying mechanical loading alone,” Rudykh says. “This advance could enable us to design new soft materials with enhanced performance and functionality.”
The ability to tweak a material’s fine internal structure in this way allows researchers to tailor its physical properties and to even switch different properties on and off as desired. And since harnessing magnetic fields eliminates the need for direct contact or pesky cables, new soft materials could be useful for applications such as medical implants, Rudykh says.
Analysis of the new patterns and results
In collaboration with researchers from the Air Force Research Laboratory, the team demonstrated and analysed the newly formed patterns using a soft elastomeric material. Inside the soft material, the team embedded small particles of stiff, magnetizable material in a simple periodic pattern.
Then, the researchers applied different levels of magnetic fields to the material, which caused the magnetized particles to rearrange and create forces and stresses within the soft material.
Rudykh says the new patterns that emerged from the rearranged particles varied from highly organized and repeating patterns to unique patterns that seemingly have large-scale order but are disorganized at the local level. “Notably, we can tune the magnetic field to produce a desired pattern and switch the material’s properties,” Rudykh says. “I’m excited to further explore this phenomenon in more complex material systems.”
This research is supported in part by a Cooperative Research and Development Agreement between the Air Force Research Laboratory Materials & Manufacturing Directorate and UW–Madison.
Featured image: An applied magnetic field (in blue) can cause magnetized particles embedded in a soft material to rearrange themselves into new patterns. By harnessing this phenomenon, researchers can fine-tune the soft material’s properties. Image courtesy Xin Zou, Grainger Institute for engineering