Secondo uno studio da poco pubblicato sulla rivista Nano Energy curato dai ricercatori dell’Institute of NBC Defence e della Tsinghua University in Cina, le batterie al litio possono emettere oltre 100 gas tossici che fanno male alla nostra salute, oltre a rovinarsi con il tempo. Questo accade perché le batterie agli ioni di litio possono essere ricaricate solo per un numero limitato di volte e a metà della loro vita iniziano a degradarsi.
Ma c’è anche un problema maggiore: il prezzo di questo elemento è aumentato del 60% in un anno in quanto l’estrazione richiede enormi volumi d’acqua e il catodo, che permette di far funzionare le batterie, è costituito da cobalto.
Le batterie al grafene invece vengono prodotte a partire dalla grafite. La produzione si basa su processi a basso costo e altamente scalabili (tecniche di filtrazione e stampa), compatibili con diversi materiali, dalle plastiche ai materiali tessili. E la più grande fabbrica d’Europa si trova a Como. Le batterie realizzate con questo materiale sono state realizzate producendo il grafene in forma di inchiostri, tramite un processo di esfoliazione della grafite brevettato dall’IIT e grazie alla sovrapposizione di strati flessibili successivi: due fogli di grafite, due membrane porose a base di grafene (che hanno lo spessore di un atomo e dunque sono sottilissime) e una membrana polimerica bagnata da un elettrolita.
A questo punto si ottiene un dispositivo facilmente integrabile negli indumenti, che può essere avvolto da un rivestimento esterno realizzato con materiali resistenti all’acqua e lavabili. Rispetto al litio, le batterie al grafene hanno la capacità di immagazzinare in tempi rapidissimi energia. Il che significa tempi di ricarica molto ridotti.
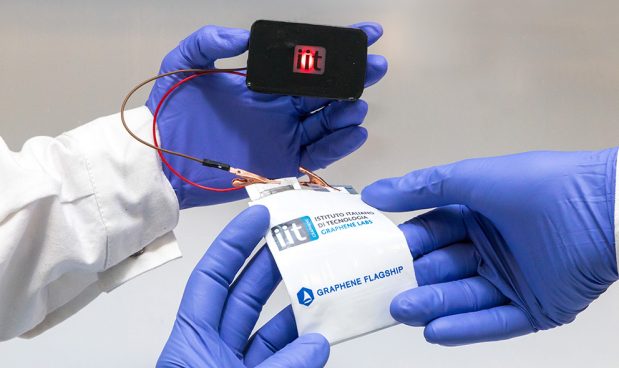