A team of engineers from the University of Delaware (US) has developed a novel 3D printing technology that enables low-cost, flexible production of items made of fiber-reinforced polymer composites using continuous carbon fibers and thermosetting polymers. Their results were recently published in the journal Matter.
Fiber-reinforced polymer composites and 3D printing
Fiber-reinforced polymer composites offer many advantages, but their big drawback is they are typically complex and expensive to manufacture. In recent years, 3D printing of composites has been successfully demonstrated using thermoplastic polymers and discontinuous fillers, but the resulting 3D-printed composites often have poor mechanical properties and low service temperature due to the limitations of the constituent properties. Consequently, 3D printing of composites using continuous carbon fibers and thermosetting polymers is expected to offer exceptional mechanical properties and thermal stability as well as featured design flexibility, low cost, reliability, and repeatability. However, no additive manufacturing technique has ever been reported to process continuous carbon fibers and thermosetting polymers for direct 3D printing of the finished composite.
A novel technology
“This is believed to be the first time anyone has achieved such 3D printing of continuous carbon fiber and thermosetting composite,” said Kun (Kelvin) Fu, an assistant professor of mechanical engineering at the University of Delaware, the corresponding author of this work. Kun (Kelvin) Fu runs a Composite and Additive Manufacturing Lab at University of Delaware, and his lab is focusing on additive manufacturing and processing of materials, structures, and devices across multiple length scales for applications in energy, environment, and health.
“Continuous carbon fibers and thermosetting resins are very important to make strong and light-weight composites, and they are widely used in many applications, such as aerospace, automotive, and sports products,” continued Fu, “3D printing could reduce labor and tooling cost, and fabricate composite in a more energy-efficient, rapid, and reliable way with minimum defects.”
Fu and the other researchers of the team developed an approach called localized in-plane thermal assisted (LITA) 3D printing, which allows the user to control the thickness and degree of curing of liquid polymer that solidifies into the desired shape.
In LITA 3D printing, the researchers carefully manipulate the temperature of the carbon fibers, aiding the flow of liquid polymers into channels between the carbon fibers. Then, the polymers are cured, solidifying into a 3D structure. No post-curing is needed in LITA 3D printing, which could save a large amount of energy compared to the conventionally fabricated composites requiring tens of hours of post-curing.
The team developed a robotic system that includes a unique printing head and automated robot arm. This customized 3D printer allows the group to print a variety of shapes and structures.
LITA 3D printing could provide many industries with a rapid, energy-efficient method to make composite components in a variety of shapes using a variety of combinations of polymers and fibers.
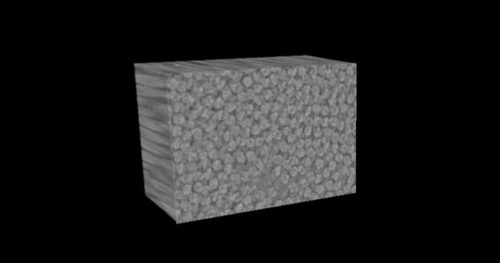
Featured image: This is a schematic of the new 3D-printing approach devised by UD researchers. “A heater touches and moves along the carbon fibers to generate a dynamic temperature gradient, triggering the dispensed liquid polymer to infuse and cure in the carbon fiber structures,” according to the recently published journal article. – Credit: University of Delaware
Source: University of Delaware