Col supporto tecnico di GE Additive (divisione dell’americana General Electric), HRE ha creato il primo cerchio in titanio e fibra di carbonio prodotto mediante stampa tridimensionale: un procedimento che parte dalla polvere di titanio per arrivare alla realizzazione dei sei componenti che costituiscono le razze della ruota, nonché l’elemento centrale di fissaggio al mozzo.
La ruota così fabbricata, denominata HRE3D+, risulta essere più resistente delle fibre di carbonio attualmente presenti sul mercato. Inoltre, questa nuova tecnologia costruttiva consente di realizzare cerchi dal design fino ad ora impensabile, caratterizzati da proprietà meccaniche eccezionali e del tutto immuni ai fenomeni di corrosione.
La fusione di titanio è resa possibile mediante un procedimento che sfrutta un fascio di elettroni, usato anche per modellare le razze del cerchio secondo un disegno computerizzato prestabilito. Il fattore umano è focalizzato sulla finitura, rimozione dello scarto produttivo e assemblaggio dei pezzi stampati e successivamente uniti al cerchio in fibra di carbonio. L’obiettivo per il futuro? Passare dai sei elementi costruttivi a un cerchio monoblocco.
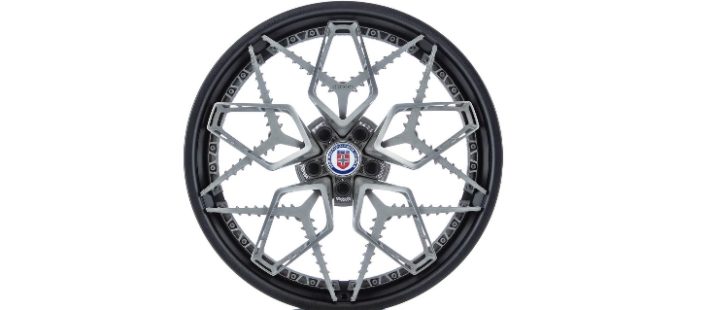