Il team Dynamis PRC
Il Team Dynamis PRC è il Reparto Corse del Politecnico di Milano ed è stato fondato nel 2004 da un piccolo gruppo di dottorandi del Dipartimento di Meccanica. Dalla sua nascita il Team ha subito molti sviluppi: ora è composto da più di 100 studenti di tutte le facoltà di ingegneria del Politecnico che ogni anno progettano e costruiscono un’auto da corsa per competere con altri atenei di tutti il mondo. Per portare a termine il progetto, gli ingegneri del Dynamis puntano sull’innovazione tecnologica e sul continuo passaggio di conoscenze e competenze all’interno del Team stesso. Grazie a questa filosofia, il Team ha acquisito molta esperienza nell’ambito della lavorazione dei materiali compositi, in particolare della fibra di carbonio.
Processo di laminazione della fibra di carbonio
Fino alla scorsa stagione il processo di laminazione della fibra di carbonio è rimasto pressoché uguale alle stagioni precedenti. In primo luogo, venivano fresati i modelli, tipicamente realizzati in resina. Questi erano poi rifiniti in tre passaggi:
- Il primo prevedeva un lavoro di finitura superficiale attraverso l’utilizzo di carta vetrata, salendo da una grana più grossa a una più fine
- Si procedeva poi con l’applicazione di un prodotto turaportante per sigillare le asperità superficiali
- Infine, si applicava il distaccante per favorire la separazione dello stampo dal modello.
Successivamente si procedeva con la laminazione dello stampo, tipicamente realizzato con fibra di carbonio di grammatura elevata (pari o superiore a 600 g/m^2). Una volta curati, gli stampi subivano un trattamento simile a quello dei modelli. Ultimata la preparazione si procedeva con la realizzazione del pezzo.
Novità di quest’anno
Per rendere il pacchetto aerodinamico più leggero quest’anno sono state introdotte per la prima volta nella storia del Team le laminazioni cave. Fino alla stagione precedente tutti i componenti di questa tipologia erano composti da pelli di carbonio più il core, tipicamente Nomex o Rohacell. Per ridurre significativamente il peso, l’utilizzo dei core è stato ridotto alle sole aree in cui è strettamente necessario per rispettare i vincoli sulle rigidezze imposti dal regolamento. In questo modo i componenti hanno assunto una configurazione simile a quella aeronautica in cui sono presenti centine e longheroni per rinforzare le strutture delle ali e della fusoliera.
Questo nuovo processo ha introdotto varie complicazioni
La progettazione e la realizzazione degli stampi e dei modelli è rimasta pressoché inalterata rispetto all’anno scorso; infatti, sono realizzati sempre in una resina ad elevata densità e ridotto coefficiente di dilatazione termica.
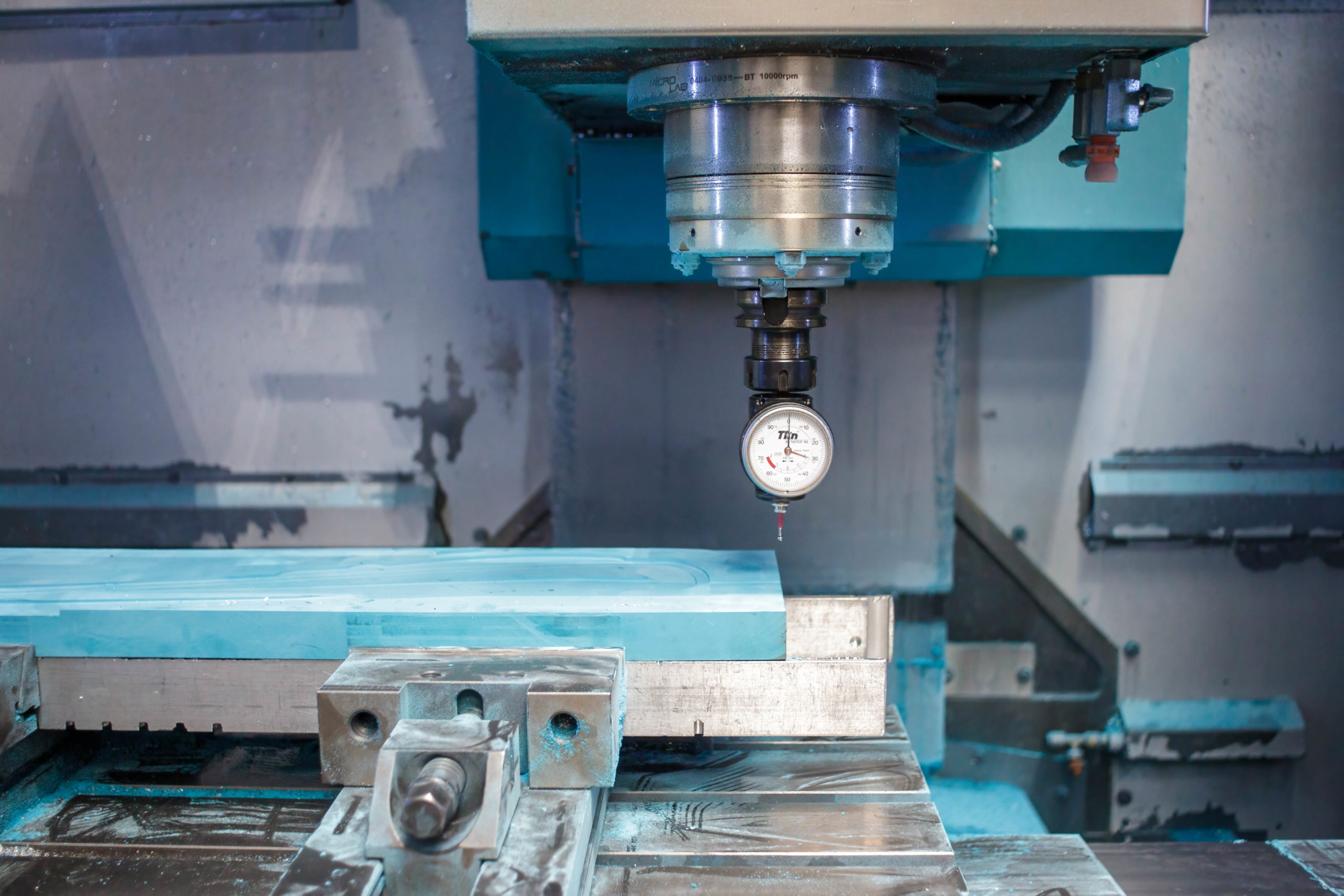
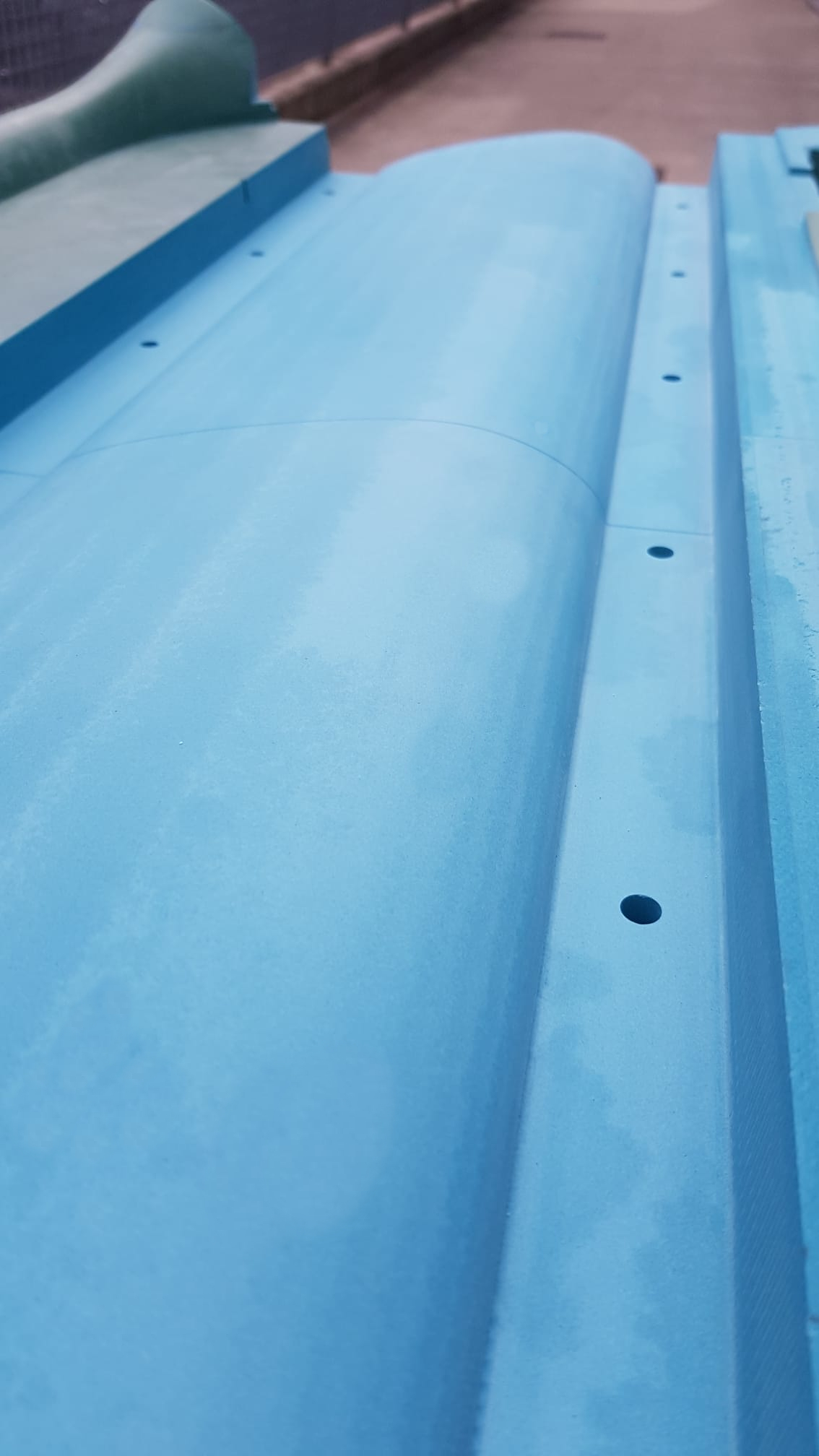
L’unica accortezza in più è stata quella di lasciare i lati aperti, condizione necessaria per far sì che fosse possibile far passare il sacco tubolare, essenziale per laminazioni di questo tipo.
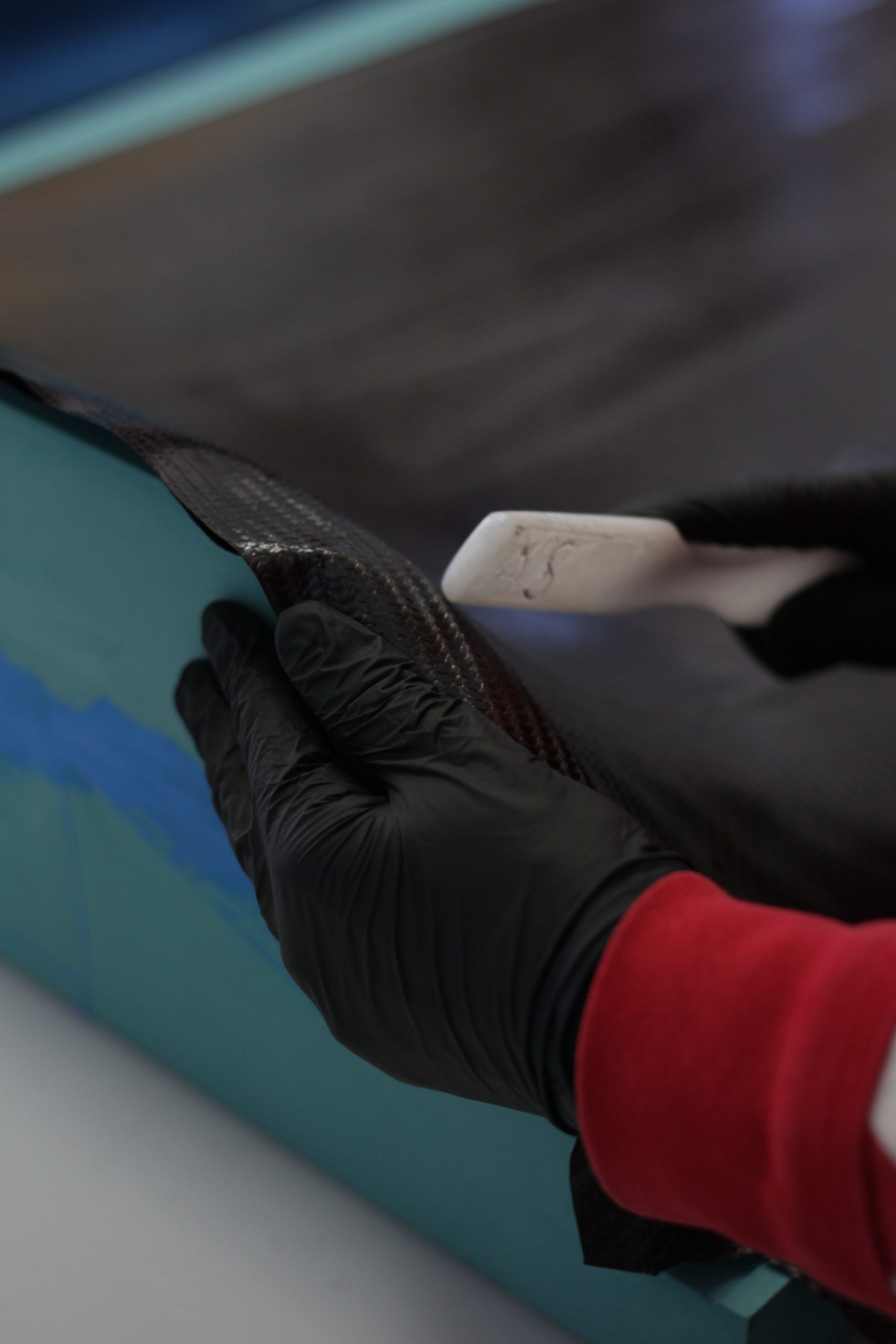
La laminazione (fig 3, fig 4) e l’insaccamento sono i due processi che hanno richiesto maggiore attenzione rispetto alla stagione passata. In primo luogo, si stendono le pelli sui due semi stampi (fig 5): esse formeranno il guscio rigido esterno del profilo e ne conferiranno la rigidezza adeguata. Successivamente si vanno a deporre i longheroni. Terminata la laminazione (fig 6), vengono assemblati i due semi stampi e si procede con il sacco da vuoto.
A differenza del sacco da vuoto tradizionale in cui viene semplicemente ricoperto il pezzo, le laminazioni cave richiedono anche un sacco tubolare interno. Tirando il vuoto questo va a schiacciare le pelli contro lo stampo dall’interno permettendo quindi la realizzazione di tale pezzo.
Per poter funzionare, si deve chiudere il mastice sopra al sacco tubolare. In questo modo, una volta fatto il vuoto, questo viene tirato contro la parete interna del componente da produrre. Nel caso dell’ala anteriore in cui sono presenti due longheroni sono necessari tre sacchi tubolari, rendendo il processo notevolmente più complicato.
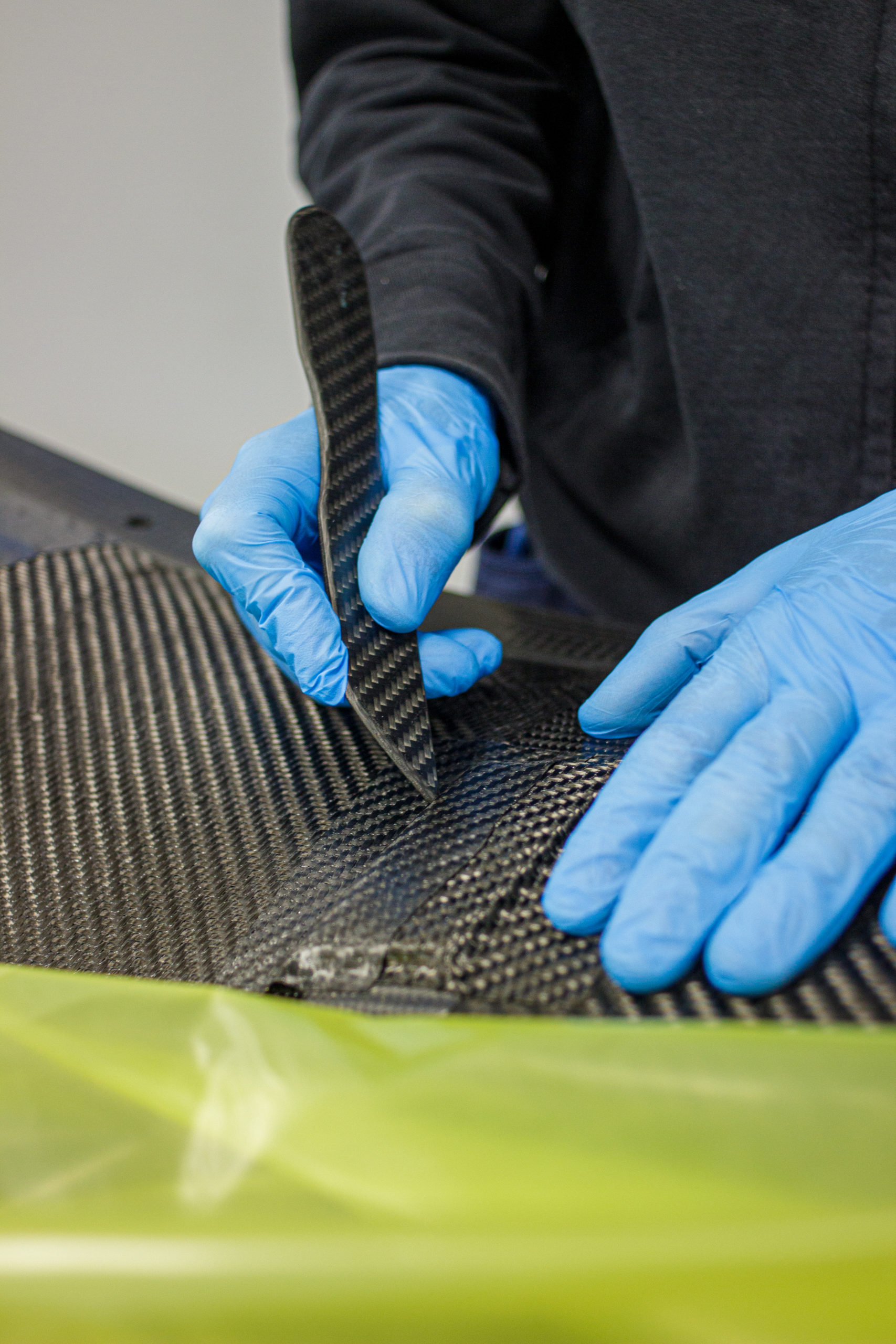
Criticità
Le principali criticità riguardano la non ispezionabilità. Infatti, poiché i componenti hanno lunghezze oltre il metro, risulta difficile notare la creazione di ponti e grinze che possono causare problemi durante la cottura in autoclave. Per questo motivo bisogna assicurarsi di disporre il sacco tubolare in maniera corretta prima di assemblare i due semi stampi, assicurandosi che ve ne sia abbastanza per andare a ricalcare tutte le curvature e i dettagli del pezzo.
A questo punto si può procedere con la cura del pezzo in autoclave.