La casa svedese di hypercar ha deciso di fornire, per chi lo desiderasse, la possibilità di avere le ultime Regera con un corpo vettura denominato Naked Carbon: in pratica con la fibra di carbonio a vista senza strato di trasparente, una livrea molto particolare che non ha bisogno di finiture a parte quelle effettuate a mano. Un processo di lucidatura a mano, molto delicato. Koenigsegg ha infatti sottolineato che anche un solo passaggio in più avrebbe potuto rovinare la superficie liscia. La carrozzeria viene lasciata allo stato puro, privata di ogni strato e di ogni resina che normalmente la rivestono e proteggono. Si potranno così accarezzare i pannelli in fibra di carbonio senza filtri alcuni ed ottenere nel contempo una livrea che non ha paragoni a livello di fascino.
Koenigsegg assicura che la carrozzeria è resistente e meno soggetto a graffi o segni prodotti da elementi atmosferici e ghiaia. Sono stati effettuati numerosi test su diversi campioni, lasciati esposti al caldo estivo o al freddo e alla pioggia invernale. Per anni questi campioni sono stati lasciati all’aperto e nessuno ha mostrato segni di cedimento. Gli ottimi risultati permettono quindi di utilizzare questa tecnica per un’intera vettura.
La mancanza dei rivestimenti alla carrozzeria in fibra di carbonio ha consentito alla Regera di risparmiare 20 kg, rispetto al modello standard, così adesso fa segnare 1.400 kg tondi tondi sulla bilancia. Una cifra che, per una sportiva spinta da un V8 5.0 più tre motori elettrici e capace di erogare qualcosa come 1.500 CV e 2.000 Nm di coppia massima, risulta decisamente contenuta. Sempre spettacolari le prestazioni che garantiscono uno scatto da 0 a 100 km/h in appena 2,8 secondi ed una velocità massima di oltre 400 km/h.
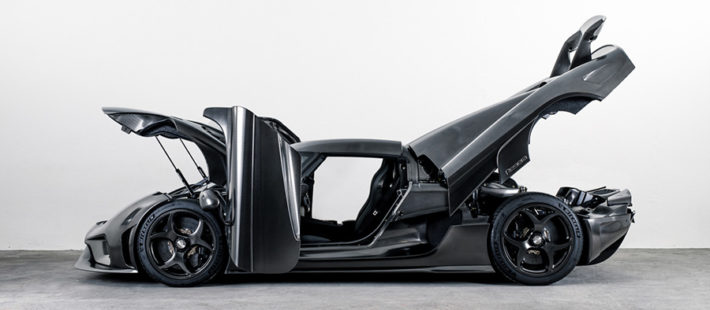