Wabash National Corporation (NYSE: WNC), a diversified industrial manufacturer and North America’s leading producer of semi-trailers and liquid transportation systems, today announced plans to invest more than $3 million for a manufacturing facility in Little Falls, Minnesota, as part of a $10M longer-term plan to expand production operations for molded structural composites (MSC).
“In support of the continued success of our strategic growth and diversification efforts in advanced composites, we’re making this next step in our multi-year development plan to commercialize molded structural composites for select parts of the trailer and truck body markets,” said Dick Giromini, chief executive officer. “We want to express our appreciation to Little Falls Mayor Zylka and city officials for their support on this project. We look forward to joining area businesses as an economic contributor and community supporter.”
After considerable evaluation of potential expansion opportunities across the United States, Wabash National is purchasing the Little Falls facility from Larson Boat Group. Wabash National selected the Little Falls location as the launch facility for MSC products because of the unique combination of an experienced and highly skilled workforce in composite manufacturing processes, along with a fully equipped and highly engineered facility capable of producing large-size parts at high rates of volume.
Combining this composites manufacturing capability with Wabash National’s R&D expertise in advanced composites will allow the company to begin scaling MSC technology across multiple product categories.
“We remain committed to transforming Wabash National into a more diversified industrial company with a broader array of products and services. Our expanding portfolio of composite offerings is instrumental to that goal,” explained Brent Yeagy, president and chief operating officer. “The expansion of our MSC manufacturing capabilities, as well as our new licensed ThermHex honeycomb core composite technology that we announced last year, highlight this growing competency in advanced composites.”
Wabash National expects to create more than 100 jobs in Little Falls over the next five years, while continuing to grow its other composites manufacturing operations in Lafayette and Frankfort, Indiana. The company expects to take ownership of the property in April 2017.
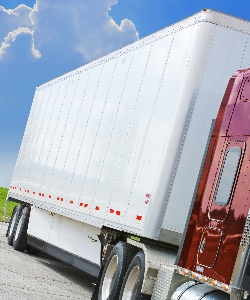