Marianne Clayton, Head of R&D at IsoTruss, Inc.
The patented IsoTruss® is an innovative composite lattice geometry named for its repeating pattern of isosceles triangles. The IsoTruss ® was originally invented by Dr. David W. Jensen, a professor at Brigham Young University (Provo, UT) in 1994. The IsoTruss® geometry reduces the amount of material needed to achieve excellent mechanical performance. The innovation comes from aligning the fiber in the composite material with the direction of forces in axial and circumferential directions. The structure can be optimized with material added or removed where needed to reduce product weight for a given application and prevent unnecessary material usage. IsoTruss Inc., founded in 2015 by Mr. Nathan D. Rich, developed the IsoTruss® Tower using the patented technology targeted at the global telecommunications market including cellular network towers, mobile cell sites, and wireless internet service provider infrastructure. The IsoTruss® Tower won the 2023 Global Innovation Award by JEC Composites in the Equipment, Machinery & Heavy Industries category.
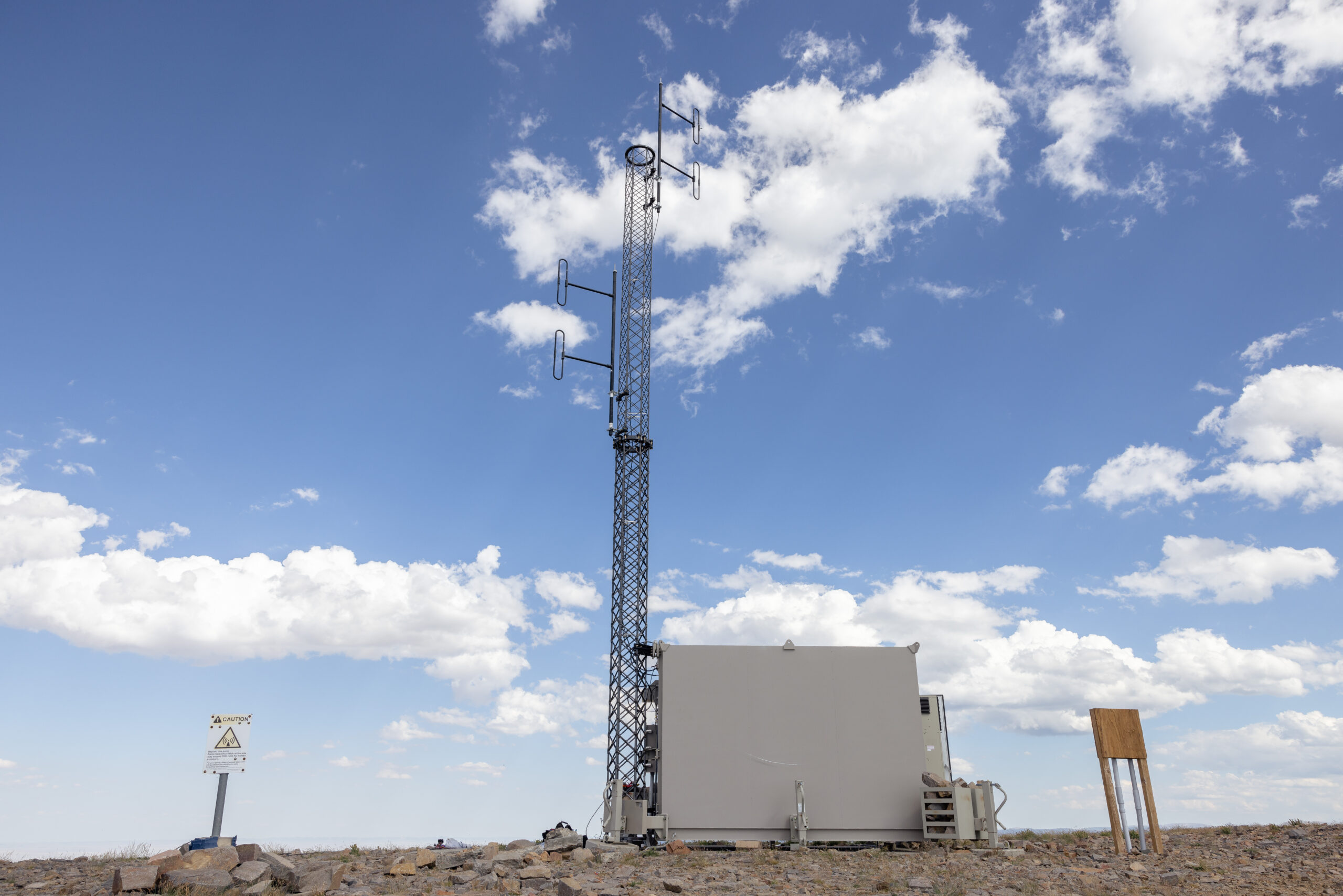
The Product
The attraction of composites in the concrete- and steel-heavy infrastructure and construction industries stems from lower weight, corrosion resistance, and resilience. Within the telecommunications industry specifically radio frequency transparency is also a draw. The IsoTruss® further amplifies the advantages of composite materials with its lattice geometry. The lattice pattern of the IsoTruss® geometry places the fibers in the direction of forces to withstand axial, bending, and torsional forces with less material. This minimizes the use of material while giving high strength and stiffness. Lighter weight, together with corrosion resistance and resilience, translate into distinct advantages in installation and performance.
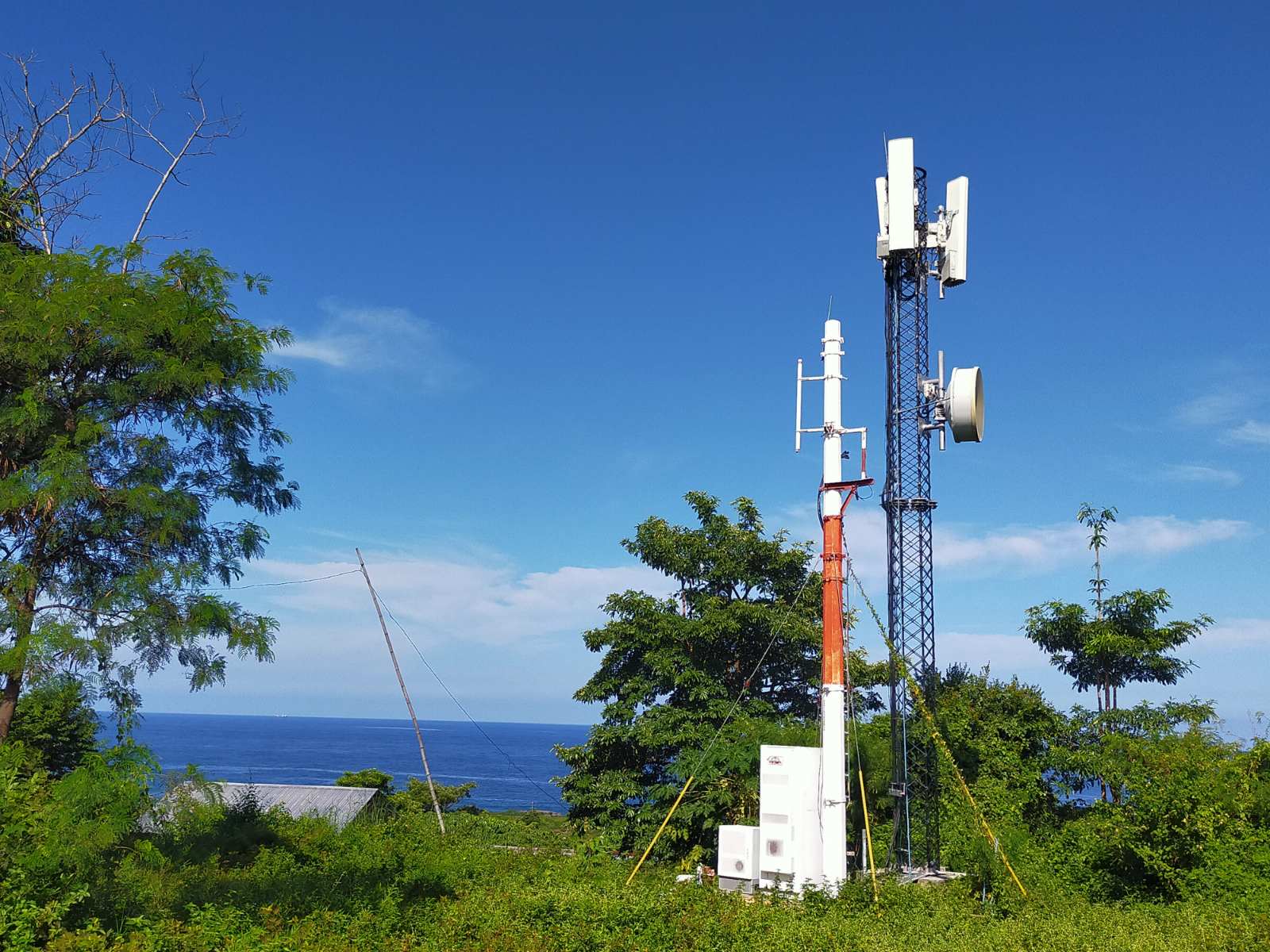
Installation Advantages
The lighter weight of IsoTruss® towers has significant advantages in installation from delivery to assembly. IsoTruss® towers are up to 1/12th the weight of a steel tower designed for the same load. For delivery, this means fewer loads with lighter vehicles to reach the deployment site. Unlike steel towers, IsoTruss® towers can be transported with light-duty trucks. For the installation itself, IsoTruss® towers require less equipment and less time. Smaller cranes can be used for assembly and the tower sections can also be maneuvered by hand into place if necessary. IsoTruss® towers transform installation from a multiple week process to a three-day long process.
IsoTruss® towers also open more potential deployment locations. Rooftop towers are important for signal coverage in urban areas, but it can be expensive and complicated to reinforce existing buildings to support steel towers. Lightweight IsoTruss® towers, on the other hand, require little to no reinforcement. Rural or difficult-to-access areas are also ideal locations for IsoTruss® towers because their lighter weight opens more options for delivery and installation methods.
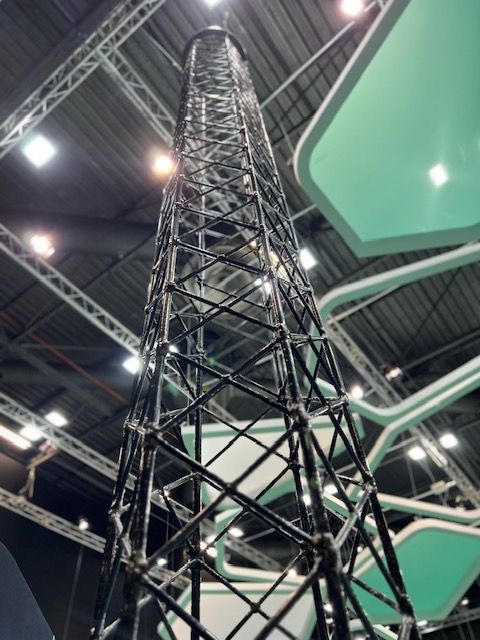
Performance Advantages
IsoTruss® towers also have important performance features. Corrosion can cause premature failure in steel towers, particularly in humid, coastal areas. Some customers have reported lifetimes as short as five years for towers in corrosive environments. Composite IsoTruss® towers are corrosion resistant, so the lifetime of the tower can be fifty years or longer regardless of the environmental conditions. Maintenance costs are also decreased with corrosion-resistant composites since there is no possibility of rot or rust.
IsoTruss® composite lattice towers are also more resilient than steel towers. The open lattice geometry reduces drag force such as the wind load. The reduced drag coupled with corrosion resistance makes IsoTruss® towers more resilient even in extreme environments. For example, IsoTruss® towers have stayed standing through hurricanes in the Southeast United States and typhoons in the Philippines. The lattice pattern also provides structural redundancy to IsoTruss® towers where damage in one part of the tower does not cause full structure failure.
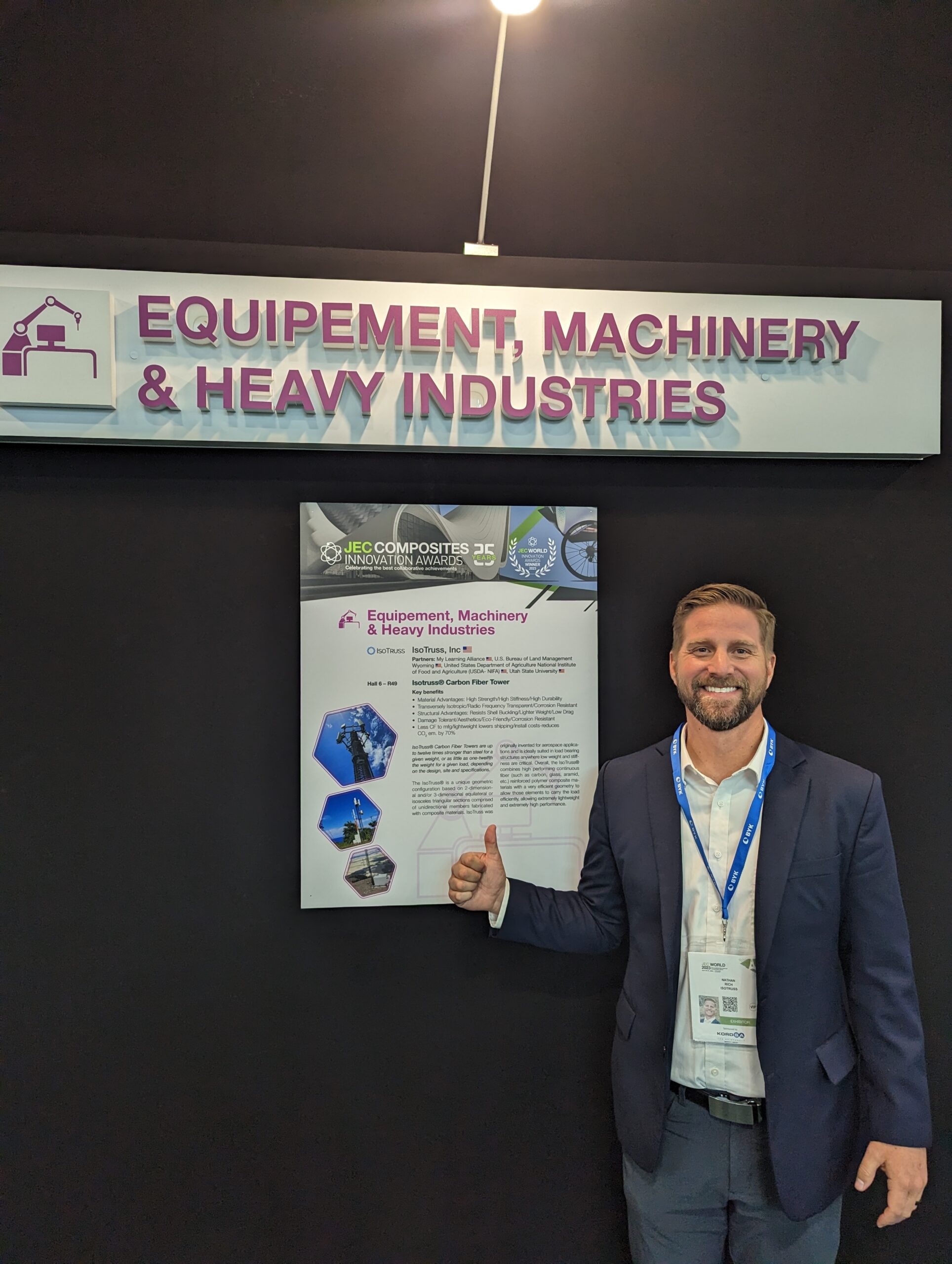
Applications
Philippines
Towers in the Philippines are exposed to humidity, salt water, and high winds. There is also a need for rooftop capable solutions to have network access in urban locations. IsoTruss® towers are an excellent fit for these constraints. The corrosion-resistant composite materials reduce the maintenance and shortened lifetime concerns related to the water and salt exposure. The lattice IsoTruss® pattern minimizes the effect of high winds. And lightweight IsoTruss® towers are the ideal solution for rooftop applications.
Elk Mountain
Elk Mountain in the Western United States hosts a communications tower to coordinate efforts of forest firefighters and to stay connected with field biologists in remote locations. At an elevation of over 3,300 meters, with no paved access roads, and significant snowfall and high winds, Elk Mountain is only accessible during the summer months with off-road vehicles. The communications site had multiple steel towers fail and turned to IsoTruss for a new solution. The IsoTruss® tower installed at the Elk Mountain site was delivered on a trailer with a light-duty truck. The tower was installed with manpower only. The tower was installed in August 2022 and is still working after a particularly heavy snowfall over the winter.
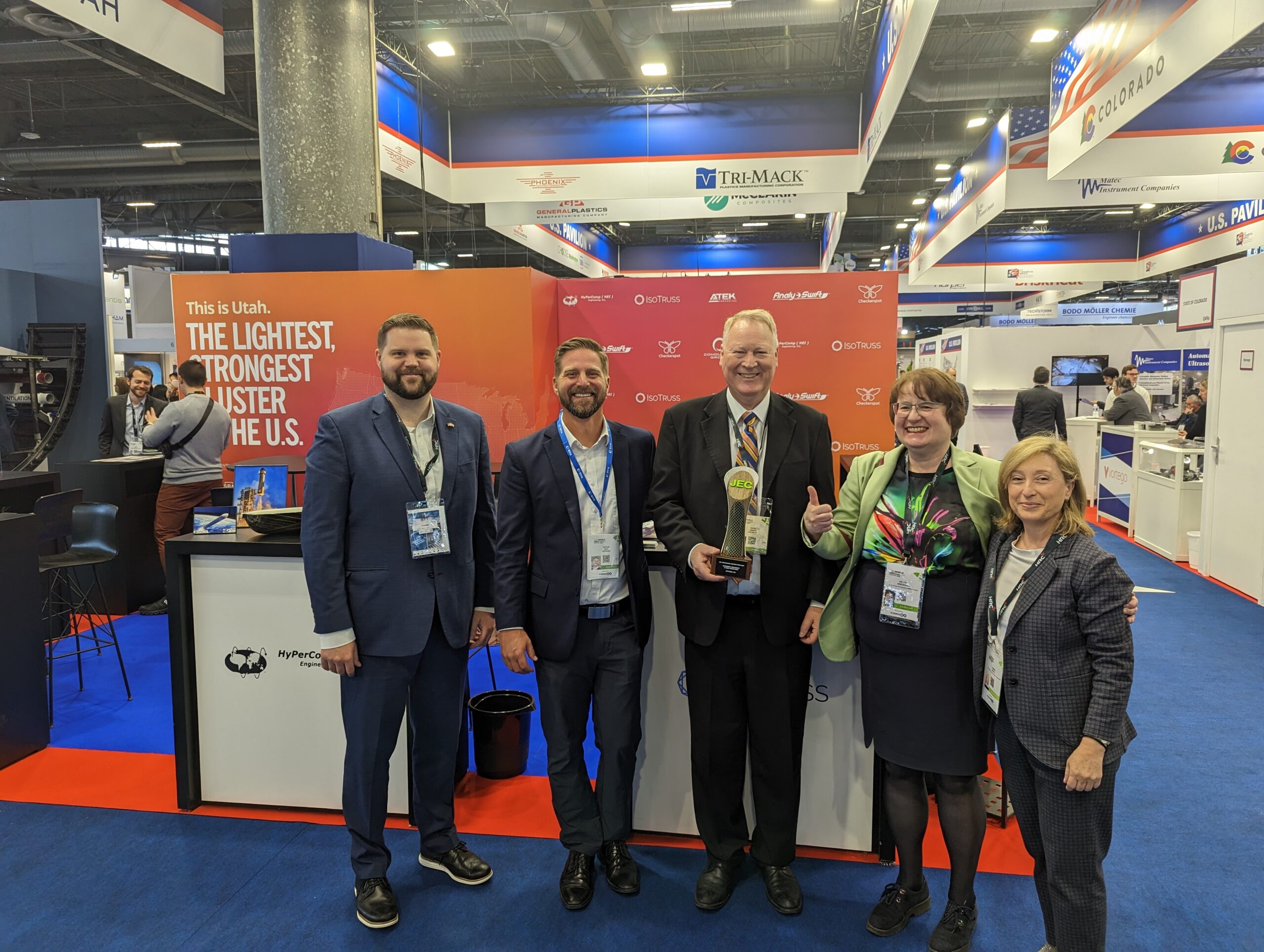
Conclusion
Composite solutions show promise in the telecommunications industry because they are lightweight, corrosion resistant, resilient, and can be radio frequency transparent. The IsoTruss® geometry further increases the inherent benefits of composite materials by aligning fibers in the direction of bending and axial forces resulting in even lighter structures. These attributes result in benefits to the customer in installation and performance.