At the beginning of 2020 Hydrogen Council (Oslo, Norway) proclaimed the start of the “Decade of Hydrogen”. Through its participation in the BRYSON project, the Institute of Lightweight Engineering and Polymer Technology (ILK) at the TU Dresden is making significant progress towards emission-free road traffic.
The BRYSON project (BauRaumeffiziente HYdrogenSpeicher Optimierter Nutzbarkeit, “space-efficient hydrogen storage with optimized usability”) is funded by the German Federal Ministry of Economics and Energy. This project involves a consortium of German Research institutes and companies, included BMW AG (Munich), ILK, composite engineering and development firm Leichtbauzentrum Sachsen (LZS, Dresden), composites distributor WELA Handelsgesellschaft (Geesthacht) and Munich University of Applied Sciences.
The project aims to develop new types of hydrogen pressure storage systems. These should be designed in such a way that they can be easily integrated into universal vehicle architectures. The project therefore focuses on the development of tank container systems in flat design.
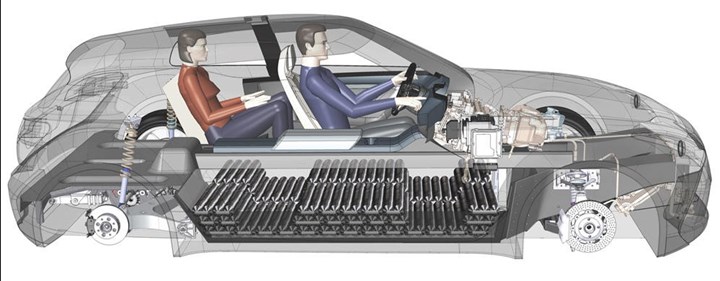
For this purpose, the ILK is developing chained tubular storage tanks in close cooperation with Leichtbauzentrum Sachsen GmbH and herone GmbH, which are manufactured from semi-finished thermoplastic fibre composite products using braiding processes. The use of highly productive braiding technology offers the possibility of reducing the manufacturing costs of hydrogen tanks for fuel cell vehicles and improving competitiveness compared to battery electric vehicles.
The use of semi-finished thermoplastics also allows easy recycling of the tank structures after their use, further improving the overall ecological balance of the Dresden approach.
Featured image: The multi-cell storage system enables efficient use of the limited space in modern vehicle designs.© TUD/ILK