The company is creating a new composites centre where the advanced carbon fibre chassis for its super cars will be built. The AMRC will use its expertise to develop advanced manufacturing processes that will allow McLaren Automotive to produce the chassis for its future sports cars. The new processes will be proven at the AMRC, in readiness to transfer them to a full-scale manufacturing environment inside McLaren Automotive’s new Composites Technology Centre in Sheffield. McLaren Automotive’s centre will host more than 200 hi-tech automotive jobs and will be in the vicinity of the AMRC’s hi-tech Factory 2050 development; where a new Lightweighting Centre will also be built to house the AMRC’s existing Composite Centre.
AMRC Executive Dean, Prof Keith Ridgway CBE, said: “This is a tremendous piece of news for the Sheffield City Region and a boost for its future as the UK’s centre for advanced manufacturing. In many respects it represents a new model that repositions manufacturing in Sheffield, taking it on from coal and steel to high performance components for the automotive, as well as the aerospace, sector. We will be working with McLaren Automotive on the construction of the carbon fibre chassis and further research, and we are talking with the supply chain. It is our ambition that supply chain companies will start to build factories here to supply the chassis plant.”
Prof Ridgway praised the University of Sheffield, Sheffield City Region Local Enterprise Partnership, Sheffield City Council and its inward investment arm, Creative Sheffield, for their part in helping to clinch the deal.
The University’s on-going investments in facilities and developing capabilities had been a catalyst to attract McLaren. These investments had further enabled the AMRC’s Composite Centre to push the boundaries of manufacturing capabilities across all market sectors.
“The LEP, Creative Sheffield and the Council were very supportive. It was probably the best coordinated activity we have seen and enabled us to put together a strong case for McLaren to come here – Prof Ridgway added -. For the AMRC this is confirmation of the growing expertise of our composites research team and their ability to meet the needs of industrial partners.”
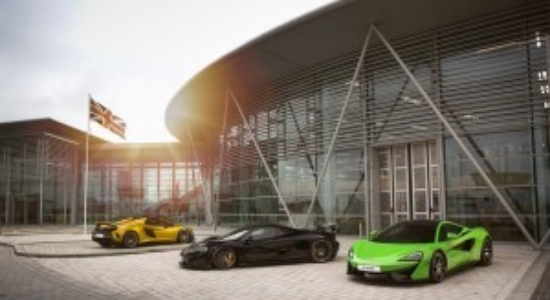