“These bast fibres include flax, hemp and jute and are immediately attractive as they provide comparable or improved tensile strength and stiffness to that of E-glass fibre, as well as contain favourable vibration dampening and non-abrasive properties,” says Dr Collins. “The cost of bast fibres is not significantly higher than that of glass fibres, particularly for the short/chopped variants, but as with all materials, there are a few notable downsides including high levels of moisture absorption and poor matrix adhesion, as well as the potential impact on the land. “There are some key innovations for the fibre-matrix interface that will stop bast fibre composites from being held back, particularly surrounding the promising use of plasma treatment technologies.” Profitable bast fibres also give the opportunity for farmers to diversify, and hemp is particularly beneficial as it can grow effectively on unfavourable land, he adds. Legislation is changing around growth restrictions of hemp in North America and this makes it more attractive and therefore the market is expected to rise at a higher rate in the mid to long term as a result. “The main reason that bast fibres and natural resins are being talked about so much is due to the sustainability advantages, as industries look to improve their Life Cycle Assessments (LCA). Although the natural fibres are not biodegradable or reusable when embedded in synthetic resins – and many of the natural resins are also not biodegradable because of artificial catalysts used – they still deviate from (sometimes toxic) petrochemically sourced resin precursors. The main commercial applications have been in the automotive sector and in sports equipment. The automotive sector makes good use of short bast fibres for the interior of car doors to provide lightweight sound and vibration dampening. The main market is automotive interiors, these materials will soon be used for the trolleys on airplanes, having demonstrated they can withstand 9G acceleration testing. Continuous bast fibres are also gaining momentum, since they are used for trunk floors and have a very large demand from 2018 onwards. There are regular high-profile examples, extending from the hemp body car made by Henry Ford in 1941 through to the concept car with a flax roof and bonnet and the world’s first completely biocomposite car revealed earlier this year, which demonstrates the huge potential for biocomposites, it also helps dispel the myth that they cannot be used for structurally significant parts. As previously mentioned, there is an emerging interest in bioresins but many of the current solutions only contain a fraction of biosourced material within an otherwise synthetic material matrix, such as the starch-based bioresin that, due to favourable adhesion, removes the need for a binder when used with natural fibres. The removal of this binder negates the cost premium of the natural resin and improves the specific modulus by approximately twenty per cent. As a result, big volumes are just around the corner and IDTechEx has been informed that this resin will be used in an automotive interior part from as early as Q2 2018. IDTechEx views biocomposites as a key emerging area within the fibre composite world: many of the highest volume industries are circulating with intent and there is an increasing amount of funding programmes and anticipation arising in this field.
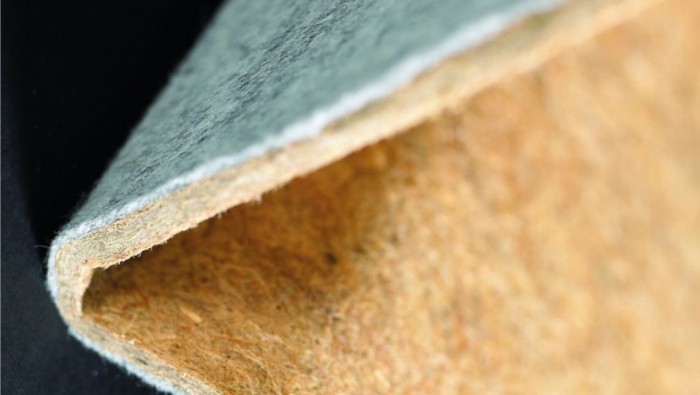