Glass fibre reinforced concrete (GRC) is widely used in the construction industry, providing a comparatively lightweight, strong and durable material that can be formed into attractive panels, cladding and rainscreens for building façades, tunnel wall coverings and other architectural structures. GRC panels can be as thin as 13 mm and yet can weigh up to a ton or more. Consequently mechanical fixing systems, which must almost always be unsighted, represent a challenge to the industry and bigHead® Bonding Fasteners has developed versatile and adaptable GRC embedding practises for its ‘bigHeads’ that enable panel designers and manufacturers many advantages – maximising design freedom without compromising strength or quality, and minimising on-site assembly effort and time.
Working closely with construction industry engineers and suppliers, bigHead offers prototyping, comprehensive testing and meticulous design development though its CE accreditation and compliance approved status for Construction Products Regulation. This certificate of conformity permits the Company to supply declarations of performance for its CE-marked stainless steel ‘bigHeads’ that meet stringent tests and the challenging standards for tensile and torque performance that the construction industry demands. At its Verwood manufacturing facility, bigHead’s unique weld technology, fully documented production testing and ISO 9001:2008 quality system ensures that every fastener produced is strong, safe and reliable.
The cross-sectional illustration below, courtesy of the Glass Fibre Composite Association (GRCA), compares a conventional stiffening GRC rib formed over a polystyrene former with a slightly thickened GRC facing panel and a reinforcing steel rib secured with bigHead anchors.
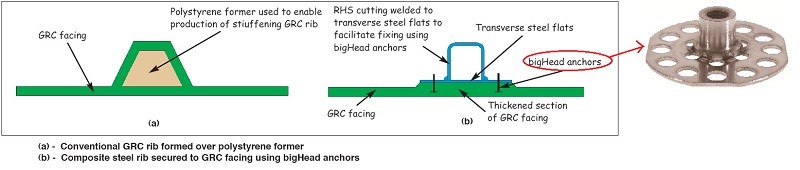
The general principle shown allows for minimum panel thickness with less additional GRC material required. This simpler and more cost effective manufacturing model removes the need for secondary fixing processes on-site, helping to prevent on-site assembly mistakes. Another concept shown below includes single (or could be multiple) embedded bigHeads used to secure channelled brackets.
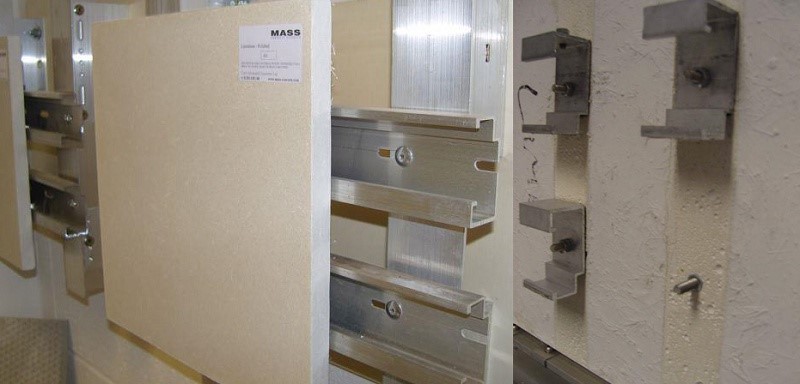
For both examples, by using a proprietary aluminium support framework and a simple template system, on-site façade assembly time is minimised, saving project costs. The 316 stainless steel bigHeads are corrosion resistant and, being completely discrete, allow full rear panel fixing with solid unencumbered front facings.
bigHead has developed a well proven success in this area through a number of applications over several years – including notable London-based construction and tunnelling projects – and has accumulated substantial technical data that demonstrates the fastener’s strength under tensile and shear loads. As well as extensive data with different material grades and panel thicknesses, minimum edge distances and recommended anchor depths can be provided. Furthermore, tensile load-to-failure test results shows that bigHeads can withstand very high loads that yield impressive safety margins. Increasing the size of the “Head” on the bigHead will increase the load values the panel can withstand.
Embedded bigHeads are also used to great advantage in plastics and other formed and moulded composite products and components, allowing complex fully sealed geometries with no secondary operations or final assembly. Alternatively bigHeads may be surface mounted with specialist adhesives to allow ultra-thin panels in materials like automotive carbon composites with no shadowing or holes. bigHeads are available as male studs, female collars and nuts, or pins and other fixings in a choice of mild steel BZP or stainless steel 316.
For further details, please visit the website at www.bighead.co.uk, call + 44 1202 583696 or email tech@bighead.co.uk.
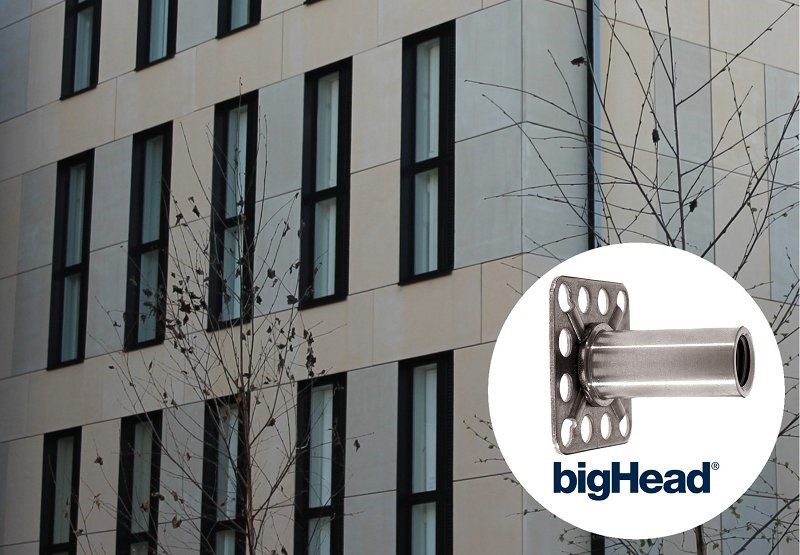
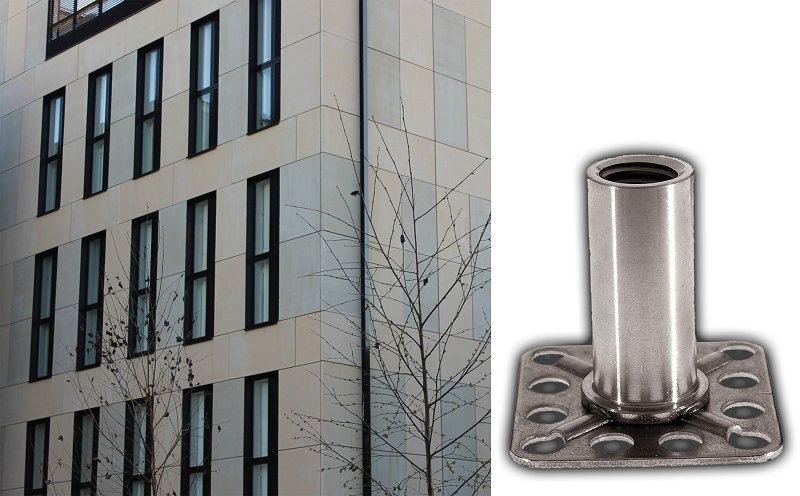