Just as other major global industries, mass transit continuously strives to improve manufacturing efficiency and reduce running costs. For rail vehicle and passenger coach designers this has meant embracing new materials and production techniques, and one area that continues to thrive is the use of fibre-reinforced polymer composites (FRP) materials to produce structures and parts that are lightweight, have high strength and offer design flexibility. bigHead – the British manufacturer synonymous with the bonding fastener – supports such innovation in the rail industry, supplying expertise and a wide range of standard or customised product solutions that enable the safe, secure and discrete fixing of individual panels or complete modular sub-assemblies.
bigHead has 50 years of experience supplying major rolling stock and infrastructure engineering companies and prides itself on an ‘engineer to engineer’ specialism where prototyping and thorough testing forms a strong part of its comprehensive project development service. Working with Tier 1 suppliers to UK and European train builders, bigHeads have been used to fasten everything from simple components to complete ‘pods’ that have been manufactured separately and then assembled into the vehicle structure and connected to its internal services. These include front cabs, passenger and bathroom modules which are secured in position utilising various male or female threaded fasteners that allow fixing without the need to drill through or provide access apertures in the composite material – saving time in assembly and preserving a smart and attractive finish. Similarly, bigHeads are used on inside of the pods and structures to fix internal panels, flooring, signage and trim components in position.
bigHead fasteners can be embedded in the composite materials during the lay-up process or surface bonded with adhesive. Both of these discrete and secure solutions facilitate fast and trouble-free mounting and remove the need for secondary assembly processes – helping to reduce manufacturing costs for fabricating lightweight composites.
Demonstrating its commitment to the industry, bigHead exhibited at the recent Composites UK Trade Association’s Opportunities for Composites in Rail showcase event. Held in collaboration with the Rail Alliance, the event focussed on applications across rail infrastructure and rolling stock where composites are successfully applied and new challenges faced.
bigHeads are used across many other industries where plastics and other formed and moulded composite products and components require discrete fastening with no secondary operations or final assembly and to maintain waterproofing. Applications range from carbon fibre panel fixing solutions in specialist and luxury car production to marine & boatbuilding, building & construction, leisure vehicles, and many other general industries. bigHeads are available for small- to large-scale production as male studs, female collars and nuts, or pins and other fixings in a choice of BZP mild steel or 316 stainless steel.
For further details, please visit the website at www.bighead.co.uk, call + 44 1202 583696 or email tech@bighead.co.uk.
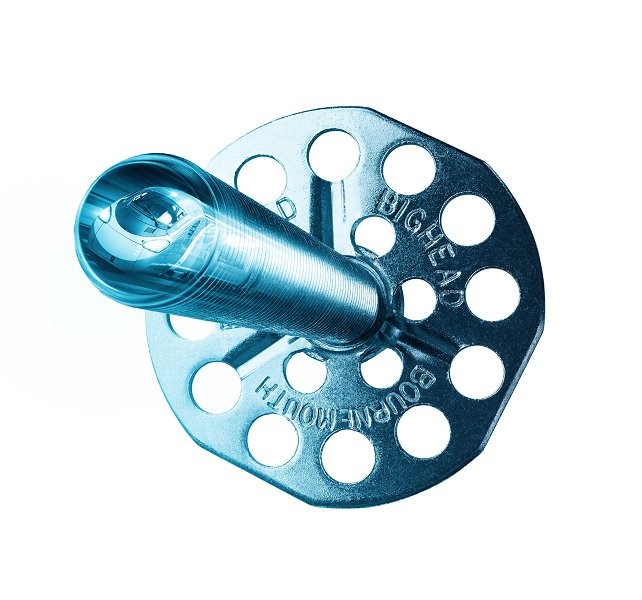