The investigation of novel materials and manufacturing processes is being carried out by the University’s Institute for Railway Research, which has been awarded funding of almost £300,000 as part of an EU-backed project to develop lighter, more reliable, more comfortable and quieter rolling stock. RUN2RAIL is the overall title of the new project. It is an element of the EU’s multi-faceted Shift2Rail programme, which fosters research and innovation in European railways. The Huddersfield Institute is participating in three of the packages, is the lead institution for the project to investigate optimised materials for running gear and it will work with the Politecnico di Milano (Milan, Italy). Professor Iwnicki explained that it was the Institute’s expert knowledge of the design of railway bogies and their dynamic behaviour that was being harnessed for the work package. At a kick-off meeting in Milan, it was decided to investigate the use of carbon fibre composites, which would enable bogie frames to be constructed layer-by-layer by robots. “You can have any number of curves or shapes and therefore build up the shape you actually want, whereas with a steel frame there are only a certain number of shapes you can make,” said Professor Iwnicki. “Also, carbon fibre is much lighter and you can put the material just where you want it, which makes it lighter still.” Another strand of investigation will be the use of additive manufacturing – or 3D printing – done with lasers and steel powders. This technology is becoming more mature and components, such as axle boxes and brackets for brakes are now candidates for this process. Although one engineering firm has produced a railway bogie that includes carbon fibre leaf springs, the RUN2RAIL project could lead to unprecedented usage of novel materials in rolling stock construction. For the moment, wheels will probably still be made from conventional steels, however. The RUN2RAIL project is now under way and is due to be completed by August 2019.
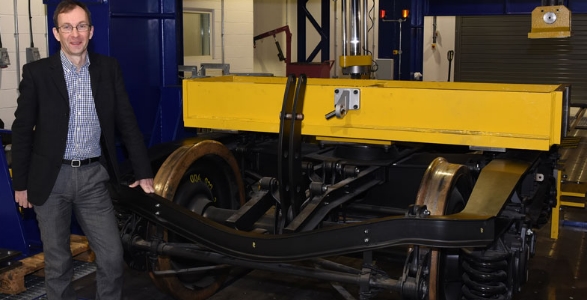