The Composites Institute and UK Research and Innovation’s (UKRI) Innovate UK have announced seven new research and innovation projects that will develop new composite materials that can advance component manufacture in a number of global industries, such as aerospace, automotive and renewable energy generation. Composite materials are important to advancements in these industries because they combine the strength of fibres with the resilience of plastics. Commonly used in the aerospace sector, composites are now becoming more widely used in areas like construction (to make whole bridges, for example) and for lighter, larger and stronger wind turbines. The projects are in collaboration with the Institute for Advanced Composites Manufacturing Innovation (IACMI) and their partner companies and universities in the US.
Innovate UK’s role: supporting companies to innovate composites sector
Simon Edmonds, Innovate UK’s, Deputy Executive Chair and Chief Business Officer, said: “Innovate UK has a long tradition of supporting companies to collaborate and innovate with international partners and we are supporting some really exciting projects between the UK and the US. We are pleased to be working with the Institute for Advanced Composites Manufacturing Innovation (IACMI) which is one of the institutes within the Manufacturing USA programme. The projects being funded are led by innovative UK composites producers, working in partnership with universities and leading research and technology organisations such as TWI and HVM Catapult Centres such as the National Composites Centre and the Advanced Manufacturing Research Centre.”
The projects are funded in the UK by the Fund for International Collaboration (FIC), which is designed to support the UK to form new, and strengthen existing, bilateral partnerships for research and innovation with leading nations with a reputation for excellence. US funding has been provided by US Department of Energy, State governments and private industry.
IACMI’s role: developing advanced manufacturing sectors
“We look forward to the opportunity to continue the progress of developing new processes and materials that are driving the adoption of advanced composites into new, mainstream sectors,” said Dale Brosius, IACMI Chief Commercialization Officer. “Through the partnership with Innovate UK, we are able to leverage expertise and thought-leadership internationally to continue to make a global impact in advanced manufacturing sectors and create new manufacturing opportunities in the U.S.”
The projects
The seven projects, including their respective UK and USA partners are, in brief:
- CADFEC: Fibre Engineered Composites, for car components: Aston Martin and Expert Tooling and Automation, based in Coventry. U.S. partners include DowAksa, Dow Chemical, and Purdue University
- TACOMA: X-ray scanning for high speed inspection of Automotive composite parts: TWI, Cambridge. U.S. partners include American Chemistry Council and Michigan State University
- HIPPAC: Advanced composites for stronger, lighter wind-turbine blades: Fibreforce Composites, Runcorn; Brunel University. U.S. partners include National Renewable Energy Laboratory, Oak Ridge National Laboratory, GE Energy, and Montefibre
- FibreSteer: Fibre shaping for stronger aerospace components: iComat (a University of Bristol spin out company), National Composites Centre (part of HVM Catapult) and Airbus. U.S. partners include Airbus Americas and University of Dayton Research Institute
- FibreLoop: Re-cycling carbon fibre production waste into new high-value components: NetComposites, Chesterfield; Far-UK, Nottingham and the Advanced Materials Research Centre (part of HVM Catapult). U.S. partners include Vartega, BASF, Michelman, and Michigan State University
- ENACT: Polymer layering for ‘overmoulding’, allowing more sophisticated design for complex parts: Surface Generation, Rutland, and Nottingham University. U.S. partner is Michigan State University
- TexTape: Trying to substantially reduce the costs of carbon fibre thermoplastics : Composites Evolution, Chesterfield, and National Composites. US partner is Oak Ridge National Laboratory.
About UKRI – UK Research and Innovation
UK Research and Innovation works in partnership with universities, research organisations, businesses, charities, and government to create the best possible environment for research and innovation to flourish. We aim to maximise the contribution of each of our component parts, working individually and collectively. We work with our many partners to benefit everyone through knowledge, talent and ideas. Operating across the whole of the UK with a combined budget of more than £7 billion, UK Research and Innovation brings together the seven research councils, Innovate UK and Research England.
About IACMI – The Composites Institute 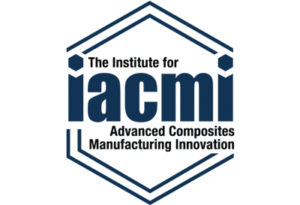
The Institute for Advanced Composites Manufacturing Innovation (IACMI), managed by the Collaborative Composite Solutions Corporation (CCS), is a partnership of industry, universities, national laboratories, and federal, state and local governments working together to benefit the nation’s energy and economic security by sharing existing resources and co-inves
ting to accelerate innovative research and development in the advanced composites field. CCS is a not-for-profit organization established by The University of Tennessee Research Foundation. The national Manufacturing USA institute is supported by a $70 million commitment from the U.S. Department of Energy’s Advanced Manufacturing Office, and over $180 million committed from IACMI’s partners.