The GE9X will be the most fuel-efficient engine GE has ever produced on a per-pounds-of-thrust basis, designed to achieve a 10% improved aircraft fuel burn versus the GE90-115B-powered 777-300ER and a 5% improved specific fuel consumption versus any twin-aisle engine at service entry. In addition, the engine will deliver an approximate 10-to-1 bypass ratio, a 60-to-1 overall pressure ratio and margin to Stage 5 noise limits.
At nearly 13 feet in diameter, the GE9X is the largest jet engine ever built. It is wider than the fuselage of a Boeing 737.
The 20,000-pound turbojet that GE is testing at its proving ground in Ohio draws air faster, at greater volume, and with superior efficiency than the former top dog, the GE90-115B. A pair of them could suck all of the air out of a space the size of Yankee Stadium in 13 minutes flat.
GE designed the behemoth specifically for the Boeing 777X widebody airliner expected to take flight in 2020. The engine uses 3-D printed components, composite materials, and redesigned fan blades and air routing to deliver a staggering 10 percent increase in fuel efficiency without sacrificing power or reliability. That’s a Herculean feat in a field where engineers would step over their own mothers for a one percent bump.
This engine actually produces less power than the GE90-115B (105,000 pounds of thrust compared to 115,000 pounds). But it’s not only far more efficient, it’s the quietest engine GE’s ever made (measured per pound of thrust). The GE9X fits easily within the FAA’s “Stage 5” noise rules, which kick in next year.
“The GE90 helped enable Boeing’s 777-300ER to have a dominant international route market position for the past 15 years,” says Richard Aboulafia, an aviation analyst with the Teal Group. The GE9X will allow “the 777-X series to maintain that market dominance for another few decades. It will likely be the largest, most powerful, and most advanced large turbofan built for some time.”
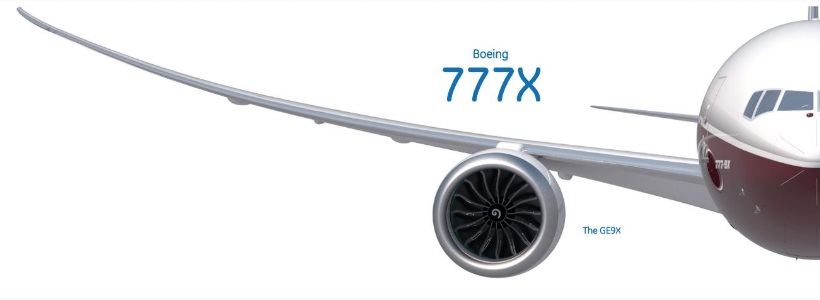