Il pannello sandwich in composito ha già trovato larga applicazione sia nell’aeronautica che nell’aerospaziale, fino ad approdare al trasporto ferroviario, ma per la costruzione di casse ribaltabili le applicazioni immesse nel mercato ad oggi sono limitate e indirizzate a particolari non strutturali. Il pannello è composto da due skins in alluminio di piccolo spessore che fanno da involucro ad un core interno scelto tra nido d’ape in alluminio o in materiale polimerico schiumato espanso in Pet o Pvc. Nello specifico, il Pvc è molto resistente e durevole, mentre il Pet è riciclabile al 100% e riutilizzabile all’infinito. Il reparto Ricerca & Sviluppo – diretto da Pietro Menci – ha progettato un pannello rivisitando tutte le singole componenti con delle formule ad alto contenuto innovativo volte a ridurne il peso, pur migliorandone l’affidabilità in funzione della destinazione di uso del pannello stesso. Anche il processo produttivo del cassone è stato rivisto, dato che non è necessaria alcuna saldatura per la costruzione del pannello, innovazione che apre un nuovo corso in termini di soluzioni costruttive. I pannelli vengono infatti assemblati tra di loro per mezzo di adesivi strutturali scelti ad hoc per resistere ad un utilizzo intensivo in ambienti atmosferici gravosi e per il trasporto e il sollevamento di carichi di notevole entità (33 Tons).
I test hanno subito dato dei risultati promettenti, ma è dall’analisi agli elementi finiti FEM (insieme di simulazioni al computer per il calcolo delle tensioni e delle deformazioni) che ci si è resi conto di trovarsi davanti ad un prodotto affidabile e dalle prestazioni interessanti. Il prototipo è stato sottoposto ad ulteriori test su strada e crash test che hanno confermato le analisi teoriche. Se la diminuzione di tara di duecento chili (due quintali) può ritenersi un risultato esaltante, il know-how acquisito nella ricerca e studio di questi nuovi materiali lascia immaginare scenari ancora più interessanti. Al momento i primi veicoli in materiale composito sono destinati al trasporto di materiale sfuso (agrario o pallettizzato) di grande volume su grandi distanze. Successivamente si prevede l’applicazione di questi nuovi materiali su tutta la gamma delle casse Menci con pannelli in composito appositamente progettati per le varie tipologie di casse e di destinazione d’uso.
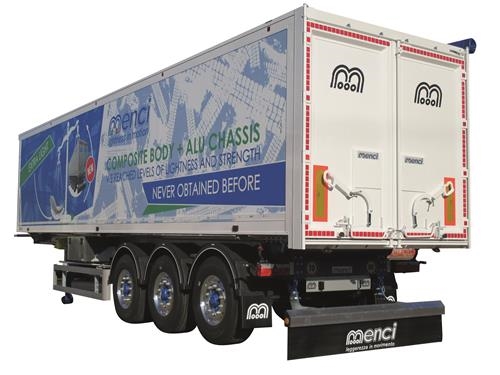