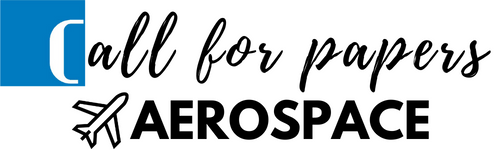
Giacomo Frulla1, Enrico Cestino1, Federico Cumino2, Alessio Piccolo3, Nicola Giulietti4, Eugenio Fossat4, Ehsan Kharrazi5
1 DIMEAS, Politecnico di Torino
2 Aerospace Consultant, Torino
3 DIMA, Facoltà di Ingegneria, Università degli Studi di Roma La Sapienza, Roma
4 Composite Research s.r.l. (Co.Re), Torino
5 Aerospace Consultant, Torino
Full article: DOI [10.1108/AEAT-06-2022-0170]
The concept of space as an inaccessible place, except for a few people, is rapidly changing, and the idea of commercial travel and space tourism are coming with their positive and negative aspects. The mission cost and the harsh space environment are the greatest obstacles to cope with, however, a lightweight and deployable habitat could be the first step making this new era of space exploration a possible opportunity. […] Numerous types of habitats have been presented in the literature for future Lunar and Martian settlements. […] Considering the structural design, a tentative classification indicates: rigid structure, inflatable and deployable structure, in-situ resources utilization (ISRU)-based structures.
[…] Terms “inflatable” and “deployable” do not have a standard use in the literature,
- preferably “inflatable” for soft and foldable materials that are balloon-like
- and “deployable” for rigid but storable components. […]
Inflatables are designed using fabrics or membranes including external primary structural elements and internal components made by aluminum or composite. Pressure inside inflatables is a fundamental component in maintaining their operative shape under loads and limited volume obtained in folded configuration at launch is of great interest for space missions.
[…] Useful in-situ resource is the regolith: a blanket of unconsolidated, loose, heterogeneous superficial deposits covering solid rock. It includes dust, broken rocks and other related materials present on Earth, Moon, Mars, some asteroids and other terrestrial planets and moons. […] A lightweight and deployable habitat design has been proposed in the following sections as a possible application of an innovative material ensuring long-duration missions on the lunar/planet surface. A new innovative sandwich configuration (MadFlex) has been proposed by Composite Research S.r.L. Co. Re (2020) to cope with requirement of good strength and foldable properties as requested by this type of structural system and alternative application as in Gili and Frulla (2016). The MadFlex has been designed to be crushproof if loaded on one side and flexible, even rollable, if loaded on the other side by means of selecting the right material for sandwich faces. This combination has been demonstrated to be very attractive in deployable habitat design.
General requirements and preliminary habitat configuration
The physical and psychological needs of humans in a confined environment must be balanced against the physical limitations of a pneumatic structure […]. These factors can be summarized as follows: habitable volume per person excluding volume occupied by equipment and other items, height of the habitat, total floor area per person. […] Preliminary habitat shape definition can be assessed assuming a deployable configuration.
The external and internal geometry of the module coupled with the material chosen for the primary structure allows the folding and deploying process with the ability to withstand the regolith cover and minimize the structural mass. Extensive MadFlex application […] empirically demonstrated two more convenient configurations for deployable habitats: cylinder (fig.1) and dome (fig.2).
Innovative material characterization and properties
The innovative MadFlex material created by Composite Research (Co.Re.) is a sandwich-like structure with dual stiffness properties when loaded along one side or along the opposite side with interesting folding properties as pointed out in figure 3.
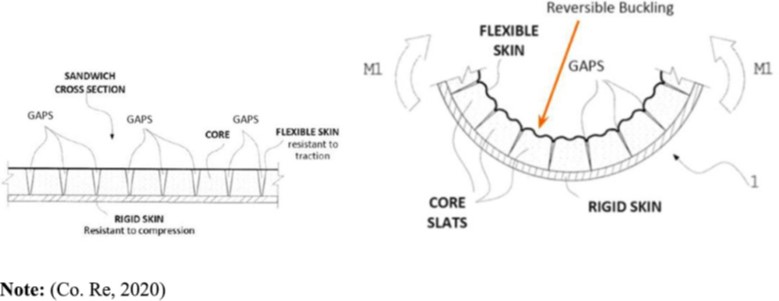
Rigid skin (n.1 in figure 3) is commonly made by carbon, glass or aramid laminates while Dyneema high density polyethylene fibers is used for the flexible one […]. Compared to the conventional aluminum scheme a similar stiffness response is demonstrated but with a weight saving of about four times.
[…] A Numerical FEM […] model has been prepared to investigate the MadFlex preliminary stiffness behavior and compare it with an analytical/ experimental one. […] The flexible layer is described as an “equivalent quasi-isotropic” material […] with non-linear characteristics (bi-modulus) […], while the rigid skin is instead made by a carbon fiber laminate [0°/90°] […] with similar tension-compression performance […].
Finally, the core foam is modeled as an “equivalent isotropic” elastic material […]. The loading and boundary condition scheme is specified […] referring to the “fourth point bending test” according to ASTM D7250/ D7250M (2011) […]. A 2D finite element modeling has been considered for the thin faces while 3D elements have been considered for the core.
Proposed configuration for Lunar and Martian habitat
According to the initial design requirements […] both the case of external regolith shield and the inclusion of internal pressure are numerically evaluated and discussed. The selected configuration has to withstand the covering regolith shield also in emergency/failure situations of no internal pressure. An internal pressure of about 1 atm added to the external regolith load is assumed in “normal” operating conditions. The proposed cylindrical architecture or dome-shape architecture has been manufactured following a similar modular concept: a combination of internal structural arches connected by flexible envelope. Extensive application of MadFlex material is considered for the arches due to its specific properties (strength and folding capability) as previously presented. Flexible layered Dyneema or specific MadFlex material can be instead introduced for the connecting envelope.
The Dome-shape module design is selected as representative study case. It is composed by eight arch-branches made by MadFlex sandwich structural elements, interspersed with an envelope made by layered Dyneema. The arches are connected by hinges with the floor and the connecting upper plate in order to facilitate its folding characteristics. The structural scheme and loading conditions are presented in Figure 4 with specific configuration details.
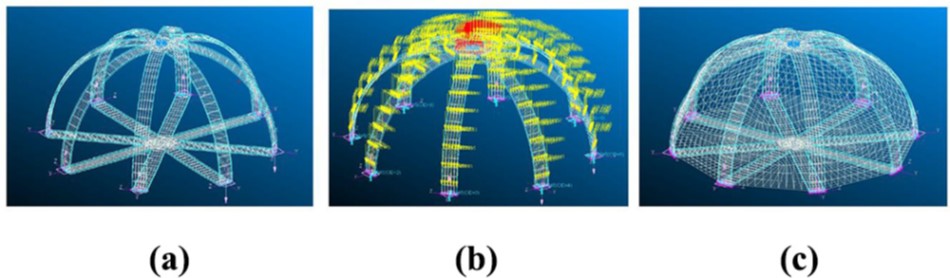
Figure 5 (a) and (b) show dome-shape displacements under emergency and operating conditions. Regolith load acts alone in emergency case withmaximum displacements of about 153mm in the envelope.
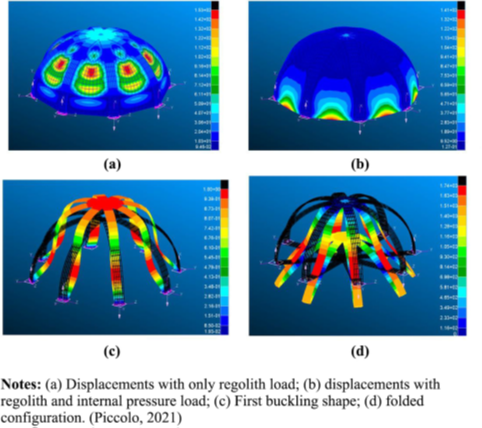
[…] Evaluation of critical condition under loads and wrinkling phenomenon completes this preliminary design step. Face wrinkling for the carbon skin provides a stress value of about 490 Mpa that is lower than the applied compressive load. Typical global buckling load factor according to SOL105 has been solved out of about 1.22 with a buckling shape according to Figure 5(c): no buckling condition within the operating load envelope has been demonstrated (Piccolo, 2021). Folding properties and folded shape have been determined.
The possibility of reducing its volume is given by the fact that the semi-arches of the dome are connected to the floor elements by means of hinges and the right positioning of the Dyneema skin in MadFlex enhance the folding curvature of arches. The closure procedure takes place by bringing the floor inward and the semi-arches almost touching each other without failure situation.
Figure 5(d) reports a step in the folding operation: the radius of the closed structure is about half the radius of the expanded structure, leading to a significant decrease in required volume than can be easily stored inside the cargo bay at launch. A weight of about 570 kg has been determined demonstrating its consistency to the requirement at launch for a typical launcher such as SLS block 1B. Feasibility of the proposed configuration is so demonstrated.
Conclusion
A preliminary evaluation of innovative material for habitat design has been performed. […] The selected configuration has been demonstrated to cope with the design requirements revealing a maximum dome deflection lower than 155 mm under critical operative condition without reaching a critical shape situation.
It also demonstrates to be consistent to the weight requirement of about 570 kg as referred to actual launcher SLS data. […] The proposed innovative material can be considered as one of the main candidates to be selected for space habitat design and space mission.