The €18 billion ITER (International Thermonuclear Experimental Reactor) under construction in Saint-Paul-lez-Durance, France, has been designed to demonstrate that fusion power can be produced on a commercial scale, providing a safe, environmentally sustainable energy source. The ITER will use hydrogen fusion, controlled by superconducting magnets, to produce massive heat energy.
Pultrusion company Exel Composites is collaborating with French industrial contractor CNIM to make glass fiber components for the magnet support structure of the International Thermonuclear Experimental Reactor (ITER), the world’s largest experimental fusion facility.
The composite pre-compression rings ensure the operation of the toroidal field coils that are employed to create a magnetic ‘cage’ to confine the 150 million°C plasma. To reduce fatigue and deformation of the coils resulting from the powerful magnetic fields, three pre-compression rings will be placed on top of them and three below, while an extra set of three will be manufactured in case replacement becomes necessary in future. The pre-compression rings are required to withstand maximum hoop stresses of up to 500 MPa at room temperature. Glass fiber epoxy composite with a high fiber content was selected as the most suitable material to withstand such extreme loads, avoid circulation of electromagnetic currents and deliver a long service life. The composite rings will have a diameter of approximately 5 m, a cross-section of nearly 30 cm x 30 cm and will weigh slightly more than 3 tons.
The process uses on pultruded composite profiles whereby each ring will be produced by winding a 2 mm thick, 2.8 km long, flat pultruded profile around a metal tool. A 0.12 mm thick epoxy adhesive tape is wound over each layer. The completed ring lay-up is cured and then machined to the required final dimensions.
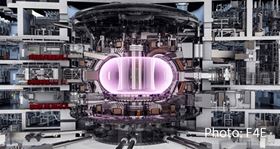