Fiber-reinforced composites are widely used in aerospace and other high-tech industries. Understanding how their microstructure and the strength of the fiber-matrix interfaces affect their failure properties can lead to manufacturing stronger materials. A recent study at the University of Illinois at Urbana-Champaign developed a model to identify the sensitivities of transverse cracking, one of the key failure processes present in composite laminates, on details of the composite microstructure.
Composite laminates used in aerospace application are typically made of layers of carbon fibers with varying orientations embedded in epoxy. For example, the composite laminate can be composed of a carbon/epoxy layer with the fibers oriented in the 90-degree direction sandwiched between two 0-degree plies. The fibers are each about seven microns in diameter, or about one-seventh of the thickness of a human hair.
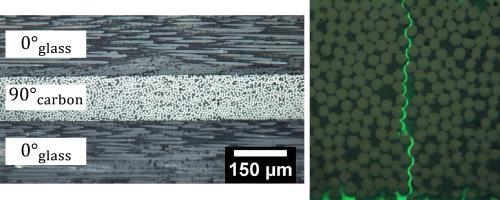
“We know from experiments that cracks propagate transversely across the 90-degree plane, then stop when they reach the interfaces with the 0-degree plies. So we developed a method that allows us to simulate hundreds of fibers in a realistic system and study how the failure response is affected if we change the location of a single fiber or of many fibers, or the strength of the interface,” said Philippe Geubelle, a professor in the Department of Aerospace Engineering.
In this new method, optical micrographs are taken of the 90-degree ply and the location of all of the fibers are extracted to construct a realistic computational model of the ply. Similar studies have been limited to tens of fibers.
“With the special finite element method we have developed to simulate the transverse cracking of the 90-degree ply, we can simulate hundreds of fibers,” Geubelle said. “The most we’ve done so far is close to 3,000 fibers. Because the crack propagates primarily along the fiber-matrix interfaces, our model emphasizes the cohesive failure of these interfaces,” he said. “In addition, we have developed the ability to extract efficiently the sensitivity of the failure event with respect to the properties of the microstructure. These properties include the location and size of the fibers, and the failure properties of the fiber-matrix interfaces. We can also compute the sensitivity of the failure event with respect to the parameters (average, standard deviation, etc.) that define the distribution of these microstructural parameters.”
The model is validated against experimental observations performed in Prof. Nancy Sottos’s group in the Department of Materials Science and Engineering at the University of Illinois.
“Of course, you could get these sensitivities experimentally, with every conceivable variation, to see what the effect is on the failure event,” Geubelle said. “To do this numerically is much more efficient.”
The work is supported by a grant from the Center of Excellence on Integrated Multiscale Modeling with funds from the Air Force Research Laboratory and the Air Force Office of Scientific Research, in collaboration with researchers from Johns Hopkins University and the University of California, Santa Barbara.