The automotive sector is facing a legislation more and more restrictive with respect to CO2 emissions, a context in which composite materials play a key role, since they allow obtaining products with a reduced weight, with high mechanical properties and rigidity. However, there are still some limitations related to costs and production ratio that avoid their presence in the market.
In order to overcome these obstacles, AIMPLAS coordinated the European project Ecogel Cronos. One of the objectives of this project is to develop a powder gelcoat coating with electrical conductivity properties obtained by incorporating carbonaceous fillers.
The conventional use of this kind of coatings has some important limitations, such as Volatile Organic Compounds (VOC) emission and long curing times. By applying this coating on the mould, a reduction of curing times has been achieved, from an hour to just a few minutes, as well as a reduction of VOC emissions (thus eliminating styrene emissions) during the coating’s polymerization. Furthermore, its electrical conductivity allows eliminating secondary painting stages for the final finish with electrostatic paint, thereby achieving a reduction of the manufacturing costs and raising the production ratio.
Another benefit of using powder coatings is the reduction of storage and energetic costs, given that it is not necessary to store catalytic systems in refrigeration, since its use is removed during the manufacturing process. Besides, it is a recyclable coating. The excess applied on the mould can be recovered by a vacuum system and reused for downstream uses.
In addition to the automotive sector, the application of these coatings is also interesting in other sectors, such as construction, leisure and sports and aviation and wind power industries.
Particularly, in the construction sector, the application of this coating allows giving antistatic properties to products such as fuel tanks and pipes.
The project, funded by the Seventh Framework Programme of the European Union (FP7/2007-2013), under grant agreement no. 609203, has the participation of other 12 European organization: ECOINNOVA and CIDETEC (Spain); Composite Integration, AXON, FAR- UK, and NetComposites (United Kingdom); CLERIUM (the Netherlands); Indupol International N.V. (Belgium); e-Xstream engineering (Luxembourg); University of Bielefeld (FHBI) (Germany); KETEK (Finland); Megara (Greece); and Steel Belt Systems Powder Coating Division (SBS) (Italy).
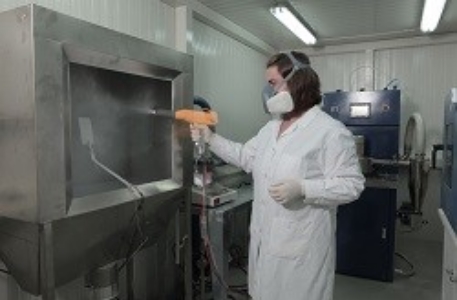