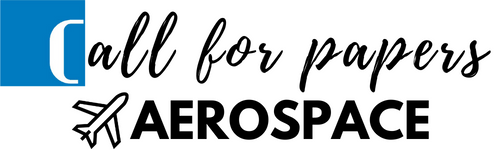
L’obiettivo di BAE System è ambizioso: implementare “La Fabbrica del Futuro”, un impianto all’avanguardia dotato di soluzioni tecnologiche e produttive di ultima generazione che operano integrandosi con l’elemento umano senza interruzioni, con una modalità di connessione integrata assolutamente inedita. Per realizzarlo, il gigante britannico del settore aerospaziale della difesa e della sicurezza ha selezionato le tecnologie più innovative, destinate allo stabilimento di Samlesbury (Lancashire, Regno Unito), la “Fabbrica del Futuro”.
Tra le soluzioni protagoniste di questa iniziativa straordinaria, la stampa 3D, il cui utilizzo è sempre più diffuso in ambito manifatturiero per la realizzazione di prototipi, attrezzaggi e parti finali a fronte di benefici quali riduzione di costi e tempi di consegna rispetto ai metodi tradizionali.
Recentemente, BAE System ha aggiunto una quarta stampante 3D F900 di Stratasys, a integrazione della serie di F900 già in utilizzo, destinata a operare 24/7 per contribuire a un’ulteriore ottimizzazione dei processi produttivi della Fabbrica del Futuro.
Ad oggi, la fabbricazione additiva FDM di livello industriale di Stratasys viene utilizzata a supporto delle operazioni di equipaggiamento a terra degli aeromobili, con un’ampia gamma di applicazioni che vanno dai modelli spaziali ai prototipi di verifica del progetto, dagli attrezzaggi di produzione come maschere e staffaggi alle parti di uso finale.
Secondo BAE Systems, l’uso della fabbricazione additiva in queste applicazioni apporta maggiore flessibilità e velocità alla produzione, contribuendo inoltre alla riduzione dei costi. Con l’utilizzo delle stampanti 3D F900, l’azienda ha infatti rilevato riduzioni significative dei costi e dei tempi di consegna nella realizzazione di strumenti di produzione rispetto ai metodi di produzione tradizionali.
I benefici della stampa 3D
Il programma “La fabbrica del futuro“ punta a guidare il futuro della produzione di aerei da combattimento con tecnologie dirompenti. La fabbricazione additiva FDM di Stratasys svolge un ruolo importante in questa iniziativa, perché aiuta a raggiungere gli obiettivi complessivi di riduzione dei costi e dei tempi di commercializzazione. Con il numero complessivo di stampanti Stratasys portato da tre a quattro, la capacità di stampa 3D viene sensibilmente aumentata. Questo acquisto, inoltre, consente a BAE System di sfruttare i nuovi materiali disponibili per questa tecnologia per applicazioni di attrezzaggio. Tra questi, il Nylon 12CF FDM in fibra di carbonio, usato per realizzare strumenti di riparazione e sviluppo robusti e al contempo leggeri per la linea di produzione.
Secondo fonti ufficiali di BAE Systems, questa tecnologia permette di rinnovare molti dei processi di produzione tradizionali. Altri benefici sono quelli di:
- stampare rapidamente in 3D pezzi unici per prodotti nuovi
- sostituire gli attrezzaggi in modo più semplice ed economico
- garantire l’operatività produttiva anche quando i componenti sono in ritardo.
In caso di interruzione della catena di approvvigionamento, la disponibilità interna di questa capacità produttiva permette all’azienda di essere più agile e di continuare a soddisfare al meglio le esigenze dei propri clienti.
Oltre la Fabbrica del Futuro
BAE Systems ha inoltre individuato con grande successo applicazioni di produzione tradizionali che possono essere migliorate o in alcuni casi sostituite con l’uso di materiali di stampa 3D ad alte prestazioni. Questo include l’utilizzo di materiali ABS e ASA durevoli per una serie di equipaggiamenti a terra dei velivoli, come le coperture del pavimento della cabina di pilotaggio per i caccia Typhoon.
Con la nuova F900, BAE Systems è in grado di realizzare le coperture termoplastiche molto più velocemente delle versioni prodotte con i metodi tradizionali, inoltre ora sono molto più leggere e facili da trasportare per il personale di terra, migliorando così l’efficienza delle procedure di manutenzione, riparazione e revisione. Un ulteriore vantaggio è che possono essere stampate in rosso, il colore che contrassegna tutti i componenti che vanno rimossi prima del volo.