La Polestar 1 ha dimostrato un elevato grado di sicurezza e affidabilità dopo essere stata sottoposta a specifici crash test interni del marchio svedese che hanno messo alla prova la resistenza della fibra di carbonio in simulazioni di incidenti reali.
Rispetto al corpo auto in acciaio dove la flessione aiuta a ridurre le energie dell’impatto che raggiunge gli occupanti del veicolo, la fibra di carbonio dissipa le energie rompendosi e frantumandosi. Nello sviluppo della vettura, Polestar ha riservato particolare attenzione al modo in cui la fibra di carbonio ha reagito alle forze estreme nelle prove d’impatto.
Il prototipo della Polestar 1 è stato spinto contro una barriera a 56 km/h simulando una collisione frontale. La maggior parte dell’energia che è stata assorbita dalla struttura della vettura, mentre il resto è stato attenuato dai pannelli in fibra di carbonio. La struttura dell’auto è rimasta rigida e dopo l’impatto non ha registrato né segni di flessione né di disallineamento.
Zef van der Putten, responsabile per la fibra di carbonio di Polestar, commenta: “Il risultato di questo primo crash test convalida la decisione di costruire il corpo della Polestar 1 in fibra di carbonio. Conferma anche che la fibra di carbonio supporta i più alti standard di sicurezza. Questo è un esempio di come Polestar lancia lo sviluppo della nuova tecnologia nel Gruppo Volvo“.
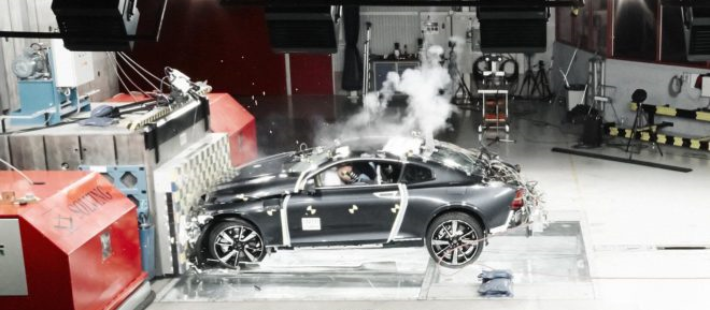