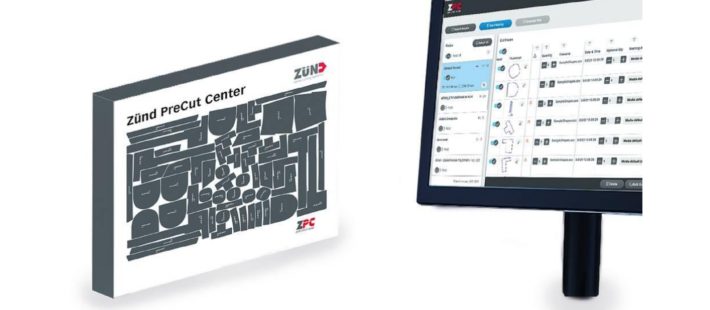
Il peso dei satelliti spaziali può rendere costoso il raggiungimento dell’orbita terrestre bassa (LEO). Se ne sono rese conto le aziende australiane che hanno dovuto fare i conti con i fornitori di lancio che fatturano i carichi utili al chilogrammo. È emersa quindi la necessità di utilizzare strutture più leggere, ma al tempo stesso robuste, per resistere in ambienti spaziali con temperature estreme….
Axiom Space, ideatore della prima stazione orbitale commerciale, ha annunciato una collaborazione con Prada, luxury brand milanese fondato nel 1913, per la creazione delle tute destinate agli astronauti della missione Artemis III della NASA. Sarà il primo sbarco sulla Luna con equipaggio dai tempi dell’Apollo 17, che risale al 1972….
Con l’obiettivo di promuovere l’adozione di tecnologie verdi nel settore aeronautico, riducendo conseguentemente, le emissioni di carbonio. La NASA ha deciso di stanziare cinquanta milioni di dollari per finanziare quattordici organizzazioni che si occuperanno dello sviluppo di processi di produzione e materiali compositi avanzati per le strutture degli aerei…
Il Fraunhofer Institute for Manufacturing Technology and Advanced Materials IFAM di Stade (Germania) sta sperimentando nuovi materiali e soluzioni di automazione per produrre velivoli più leggeri ed efficienti. Queste tecnologie rappresentano un passo decisivo sulla strada della sostenibilità, dato che ogni chilogrammo di peso risparmiato in un aereo passeggeri comporta una diminuzione del consumo di cherosene fino a 120 kg all’anno….
La supply chain dell’Additive Manufacturing in scena dal 28 al 29 settembre 2023 nella cornice del Museo Alfa Romeo per la XI edizione del Convegno/Exhibition RM FORUM…