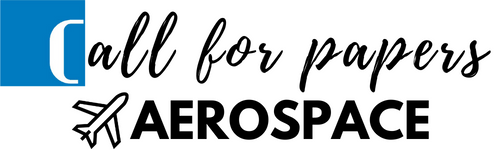
Leonardo Lecce1, Giulio Trevisan2, Francesco Galliani2, Massimo Di Pietro2
1 – Novotech
2 – Comec Innovative Srl
Nowadays the so-called alternative mobility is one of the main themes both in the automotive and the civil aviation field, but due to the urban constraints present in the area, in addition to the well-known initiatives such as car sharing, ride sharing, e-mobility, the sector of transport is moving towards alternative forms of mobility, in particular it is looking at new solutions based on air transport in urban areas.
From this point of view, the SEAGULL e-VTOL project proposes itself as a pioneer, at a national level, as regards the development of new generation transport systems, which make it possible to travel relatively short distances, included in an indicative range of no less than 100 -250km, in an average target time which is at least 1/3 lower than what would be required using the means of transport currently in use and which at the same time is sustainable from an environmental point of view (CO2 and NOx emissions; pollution acoustic and sound), but also cheap for users.
Description of the project
Electrical -Vertical Take-Off and Landing (e-VTOL) project aims to create a new generation of aircraft for private and public transport, with new business models that will allow travelers and cargo to “fly” above urban and extra-urban areas, through the integration of transformative digital technologies aimed at reducing local air and noise pollution.
The effect will be disruptive compared to existing aircraft in terms of fuel and CO2 reduction, thanks to the introduction of an all-electric propulsion system (zero emissions); but also thanks to the introduction of an adaptive and low-cost digital service platform that communicates aircraft performance and status in real-time to optimize missions (reduce fuel consumption) and preventative maintenance operations.
The reduction in consumption will also be given by the reduction in weight as the fuselage will be completely made of carbon fiber with the AFP (Automatic Fibers Placement). This will result in increased resilience to external shocks of the aviation ecosystem (end users, scientific community, industry players), creating scientific, economic, technological, environmental and social benefits.
The SEAGULL e-VTOL program will provide emission-free flight paths compared to high-speed trains and private or public cars, in fact, according to the results of a first feasibility study, these challenges will be pursued:
- capacity 4 seats
- Average load factor of 70%
- Gross vehicle weight of 1,500 kg
- ≈ 200 kW of power for short-term take-off with 2 minutes of full power (hover) at take-off and landing, with ≈ 120 kW of power required at 230Km/h for the cruise phase
- Annual use of 1500-2000 hours
- Number of motors for hovering 2 or 4
- Total flight time: 30-70 min
- Target recurring cost per passenger ≈ €50-€100.
One of the challenges that from a technological point of view appear to be among the most significant concerns the e-VTOL module which will be developed within the project, as it will guarantee automatic attitude control in the vertical flight phases, through assisted navigation by autopilot. In the cruise phase however, flight control is entrusted exclusively to the pilot.
The implementation of these technologies will be implemented through a massive use of the “Fly-by-Wire” approach. The aircraft will be equipped with electric motors for vertical take-off and landing, with DC power supply through a suitable hydrogen/ fuel supply system cells and battery capable of ensuring at least 3-10 minutes of autonomy in hovering. The integration and interface of the devices with the Flight Control System will be operated by means of DC/AC converters.
In parallel with the development of the aircraft platform, as part of the project, given the need to automate the manufacturing processes of aerostructures (greater repeatability, increased productivity, reduced production costs), a new automatic rolling technology will be designed, built and validated “low cost oriented” based on the production principle of Automatic Fiber Placement which will take the name of Automated Towpreg Placement (ATP).
The current AFP rolling machines are not able to process material in towpreg format , so a product capable of automatically positioning continuous parallel rows of single tows will be created , using a head operated by a software system which will have innovative positioning, fixing and cutting processes.
The product will be mounted on a positioner, synchronized with the anthropomorphic arm on which the rolling head is mounted. The head will be designed in such a way as to be able to manage the arrangement of the material and its positioning in order to carry out the lamination of the product.
This technology will make it possible to model objects of complex geometry and, thanks to an appropriate software tool, it will be possible to define the correct orientation of the fibers capable of guaranteeing the resistance of the component to the loads to which it is subjected.
Furthermore, a compacting roller will be positioned on the deposition head which, by exerting a compressive action on the tows, will allow them to adhere to the work surface, removing any intra- layer voids. The material will be deposited without tension or creases with precise pressure applied to the compaction roller.
The new technology (ATP) that will be developed within the project will allow a large-scale use of composites and, at the same time, will introduce a production novelty that will allow more effective construction solutions through the use of towpreg.
The machine that will be developed will allow the composite fibers to be positioned so as to exploit the directionality of the material in the most efficient way. The developed technology will constitute a functional prototype for the purposes of process and product validation, will be validated from a functional point of view in each of its groups and will form the basis for further development, with a view to future introduction on the market.
As part of the project, all the technological problems will be addressed in order to carry out a product and process development validated for the objective to be achieved and the results obtained will lay the foundations for the subsequent development of the technology which will be ready to respond to the market needs.
There are many technical-scientific problems to be addressed:
- avoiding material breakage during lamination
- guaranteeing a constant deposition speed
- guaranteeing temperature control of the material and to favor adhesion between the towpregs, study of a compact deposition head, identification of process parameters and their effects (rolling speed, pressure during deposition, temperature, material tension ).
Each of these technical-scientific issues will be explored and studied in the research phase, while the identified solutions will be implemented in the development phase. This new deposition technology will make it possible to create the DEMO fuselage for the construction of the complete aircraft (fig.1).
Fig.1: Aircraft mockup
The technology that will be developed in this project aims to bring together the advantages of Filament technologies winding (FW), Tape Laying (ATL) or Fiber Placement (AFP), i.e. the most common ones for the construction of large aerostructures (e.g. wing, fuselage) and aims to make the manufacturing process ever faster and more efficient, in line with the increasingly stringent demands of the aerospace industries, both in terms of component quality and manufacturing speed using towpreg (more economical solution than slit tape).