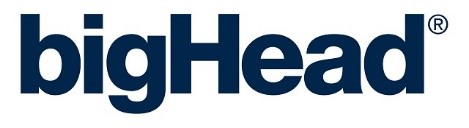
bigHead Bonding Fasteners are regularly challenged to provide custom designed fastening solutions for its customers. Whilst the standard range of over 400 mild steel and stainless steel ‘bigHeads’ provide efficient and effective discrete fixings, whether embedded or surface bonded to composite materials, there are some applications that benefit from a design approach where the characteristic bigHead welded fixing is engineered and adapted to actually improve the final design, to enhance its performance or reduce costs – and even to facilitate increased safety.
One such situation that perfectly exemplifies this engineer-to-engineer process is when Siemens began to investigate composite materials for nacelles used on its new 6 MW offshore wind turbines. In particular a composite maintenance hatch had been designed to replace a steel panel and traditional bolt fixings were used to lock and unlock it. This required two persons to perform the operation – one inside and one outside the nacelle. Clearly ease of access and its related safely were problems to be solved, in addition to reducing maintenance costs. Siemens nacelle suppliers approached bigHead and together a solution was developed.
By surface bonding the 316 marine grade stainless steel bigHead to the outer skin of the nacelle and passing the threaded stud section through its composite structure, the panel is easily secured or removed by a single person from the much safer interior of the structure. The bigHead’s large perforated head allows a generous flow of adhesive to firmly secure it in position and its outer surface includes an over-moulded insulation layer that safeguards the nacelle against lightning strikes as well as match its colour.
bigHead worked with the customer through a stringent development stage – prototyping and extreme testing the solution against the harsh conditions that the offshore wind turbines need to endure until a final design was agreed. Now in its third year of supply, the solution has been thoroughly field proven. Like all bigHead’s produced at its Verwood – UK factory, every production batch is tested and documented with completely traceable results as part of the manufacturers ISO 9001:2008 Quality Management System.
bigHead have been manufacturing its distinctive and leading brand of discrete bonding fasteners for over 50 years and has extensive experience across a wide range of industries where formed and moulded composite products require discrete and completely secure fixing. Applications range from carbon fibre panel fixing in specialist and luxury car production to building and construction, railway carriage construction, marine and boatbuilding and more.
All bigHeads are supported with tensile strength and torque performance data which is readily available from the website at www.bighead.co.uk – along with application downloads, drawing requests, whitepapers and useful FAQs. bigHeads are available for small- to large-scale production as male studs, female collars and nuts, or pins and customised fixings in a choice of BZP mild steel or 316 stainless steel.
For further details, please visit the website at www.bighead.co.uk, call + 44 1202 583696 or email tech@bighead.co.uk.