Researchers at University of Delaware’s Center for Composite Materials (CCM) have created an extraordinarily strong short fiber composite material that can be stamped into complex shapes in less than one minute. The new high-performance material, known as TuFF (Tailored Universal Feedstock for Forming), can stretch up to 50 percent, achieve properties equivalent to the best continuous fiber composites used in aerospace applications and reduce part manufacturing costs. TuFF can also be produced inexpensively and sustainably from recycled composite parts or scrap carbon fiber manufacturers typically throw away and be reused to make high performance, high value materials and parts. (In the world of advanced manufacturing, “feedstock,” refers to organic materials developed and adapted in ways that serve a manufacturing process.)
TuFF was patented in June 2020 with 32 claims. According to the U.S. Patent Office, the claim(s) within a patent application clearly define the invention, its scope and what aspects are legally enforceable.
TuFF represents a paradigm shift in composites design and opens the door for composites to replace metals in a variety of applications in the automotive, aerospace, infrastructure, electronics industries and more. Many common products, from kitchen appliances to smartphones and more, are now made with stamped sheet metal, and manufacturers might someday use TuFF instead.
The potential of TuFF
“We are going after metals at their own game,” said Jack Gillespie, director of CCM. “TuFF is low cost, can be made quickly, and is recyclable. Instead of expecting the metal manufacturers to redesign metal parts like airplanes, we decided to create a new material that can be designed and processed like metals using their existing manufacturing equipment – while still providing 40-70% weight savings.”
In September 2019, the American Composites Manufacturers Association presented CCM their “Infinite Possibility for Market Growth” Award for Composites Excellence for the TuFF material in recognition that TuFF has the potential to significantly increase the use of composites in existing markets and new ones, too.
While transforming existing industries, TuFF could enable the development of new products, such as flying cars, said John Tierney, senior scientist at CCM.
The TuFF program
Researchers at CCM started working on TuFF in 2016, when they received a $14.9 million, three-year cooperative agreement from the Defense Advanced Research Projects Agency (DARPA) for the Tailorable Feedstock and Forming (TuFF) Program. The objective of the TuFF program was to develop a new composite materials with properties equivalent to previously used materials, and develop a single-step manufacturing process that enables the use of the advanced materials for small parts weighing less than 20 pounds at costs competitive with aluminum. The project also included CCM faculty alumni collaborators at Clemson, Drexel and Virginia Tech universities. Over the three-year project, more than three dozen faculty, staff and students worked on the project. Today, CCM has a scaled pilot facility.
To make TuFF, the research team at CCM had to line everything up just right. About four decades ago, scientists theorized that if they could align these short carbon fibers precisely, they could make composites with desirable properties, but no one achieved this feat in practice until now. It took a few years, but after trying several different alignment mechanisms, the team at CCM figured out how to bring everything in line. The process can now use any type of fiber (or combinations) with nearly all polymers (thermoplastics and thermosets).
“The concepts that underpin this are an evolution of many years of basic research,” said Joseph Deitzel, senior scientist at CCM, a research center founded in 1974. “CCM has people with the skills to attack problems of this size and complexity as well as historical knowledge and creativity.”
The manufacturing method
The team did not stop once they had invented the material. They are also developing cutting-edge methods to manufacture it. CCM established a semi-automated pilot plant incorporating new control systems and inline sensors for quality control. TuFF product forms range from 20-inch wide rolls, tailored blanks for forming parts and narrow and steerable tapes for additive manufacturing processes. The team has demonstrated the feasibility and scalability of novel technologies developed through this program and are looking to supply TuFF material to designated industry partners for evaluation, prototype development and scale-up.
Researchers are now conducting additional experiments, including modeling and simulation, to further understand the behavior of TuFF so that they can tailor it for more applications.
A variety of fibers and polymers could be used to make TuFF, and the microstructure of the TuFF matrix can be tailored to each application, so there are “infinite possibilities for market growth,” but also infinite opportunities for continued basic and applied research.
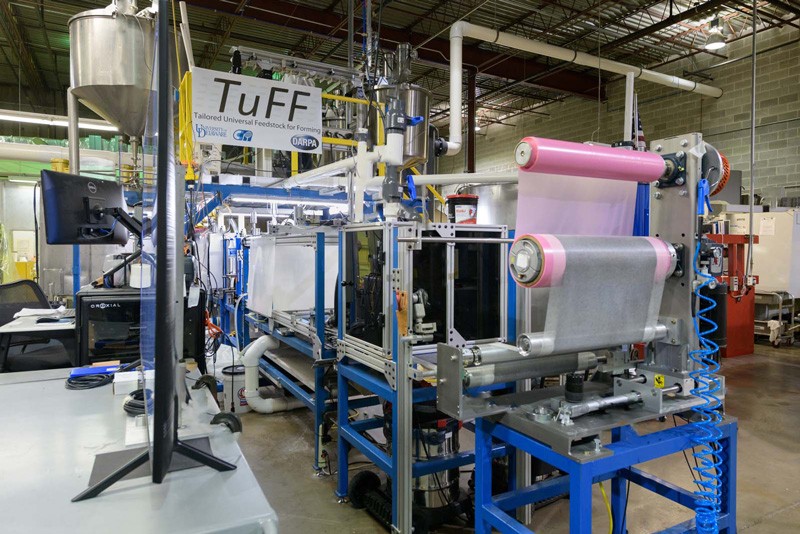
Featured image: University of Delaware researchers have developed a new high-performance material, known as TuFF (Tailored Universal Feedstock for Forming), with properties equivalent to the best continuous fiber composites used in aerospace applications. Like sheet metal, TuFF can be stamped into complex shapes | Credit: University of Delaware
Source: University of Delaware