L’alleggerimento delle carrozze dei treni permette di migliorare l’affidabilità e la qualità del servizio del sistema ferroviario europeo, e di dimezzare i costi di produzione e di mantenimento durante l’intero ciclo di vita dei veicoli. L’utilizzo di materiali compositi per lo scheletro delle vetture permette di ridurre il peso totale del treno e di aumentarne il carico utile (passeggeri e bagagli) e la velocità.
Nell’ambito del Progetto PIVOT, condotto dal consorzio AERFITEC (composto da Talgo, Aernnova, Fidamc e Tecnalia), sono stati studiati diversi materiali per processi fuori autoclave (OoA), come infusione, semipreg e pultrusione, al fine di sviluppare combinazioni di tecniche in grado di produrre strutture complesse in un unico processo. Insieme ai partner dei progetti PIVOT e PIVOT2 del consorzio AERFITEC, Tecnalia ha lavorato allo sviluppo di una carrozzeria per treno con un’elevata integrazione di tecnologie composite, soddisfacendo i requisiti antincendio della norma europea EN‑45545.
Tecniche di riduzione del peso
Le attuali carrozzerie dei treni sono formate da una struttura metallica ricoperta da carenature con funzionalità aerodinamiche, estetiche, di manutenzione e di protezione degli elementi, ma non strutturali. Alcune parti di queste strutture sono sottoposte sollecitazioni meccaniche e, di conseguenza, richiedono numerose sollecitazioni meccaniche che aumentano significativamente i costi di produzione.
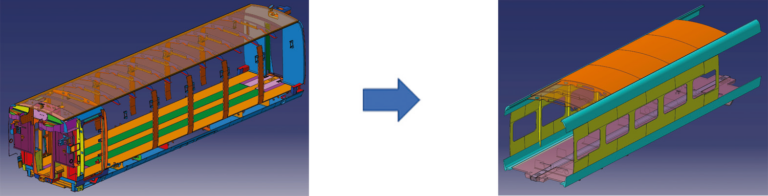
La principale strategia di alleggerimento del progetto è stata quella di unificare la carenatura e la struttura mediante processi produttivi one-shot, utilizzando materiali compositi ad elevate prestazioni meccaniche. A questo scopo, il ha team selezionato, attraverso processi di produzione come l’infusione e la pultrusione, materiali che soddisfacessero i principali requisiti degli standard ferroviari, con particolare attenzione ai compositi legati alla tossicità del fuoco-fumo (FST). Integrare diverse tecnologie è la chiave per raggiungere l’obiettivo di riduzione del peso. La combinazione di più processi produttivi permette inoltre di personalizzare le proprietà in base all’applicazione più recente e di ridurre il ricorso all’installazione di giunzioni meccaniche tra le diverse parti.
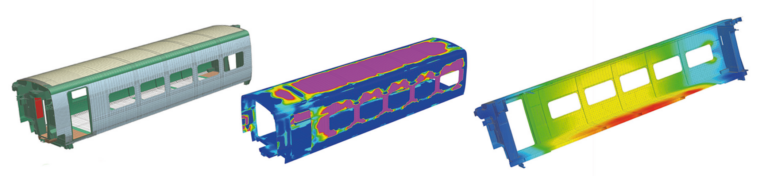
Per sviluppare una progettazione iterativa è stato necessario calcolare diverse configurazioni strutturali utilizzando l’analisi statica e dinamica (frequenza naturale-modale) attraverso il metodo degli elementi finiti (FEM), tenendo conto dei requisiti delle specifiche di carico e delle condizioni al contorno durante il funzionamento.
Soddisfare standard di alto livello
Il settore ferroviario richiede che le carrozzerie dei treni rispettino determinati requisiti e specifiche in termini di sollecitazioni meccaniche e di resistenza agli urti o alle vibrazioni. In particolare, la norma EN‑45545 prevede che i veicoli ferroviari rientrino in determinati standard di protezione antincendio che dipendono dalla natura intrinseca dei materiali, dalla posizione dei componenti nella progettazione (interno o esterno) in base al loro uso specifico (mobili, apparecchiature elettrotecniche o meccaniche), nonché dalla forma, dallo spessore e dalla distribuzione dei materiali.

Lo studio si è basato sulla valutazione dei materiali in conformità ai requisiti R7 della EN- 45545-2, tenendo conto del livello di pericolo (HL), mediante alcuni test: prova di propagazione della fiamma secondo ISO 5658 2:2006; prova di reazione al fuoco, metodo del cono calorimetrico, secondo la norma ISO 5660 1:2015; test di fumo e tossicità con attacco termico a 50 kW/m2 per il calcolo di Dsmax, Ds, VOF4 e CITg, secondo la norma ISO 5659 2:2017.
La messa a punto attraverso un dimostratore in scala
Il pavimento del treno è la parte strutturale più critica del telaio poiché trasmette la maggior parte dei carichi tra i diversi vagoni attraverso il giunto dell’accoppiatore.
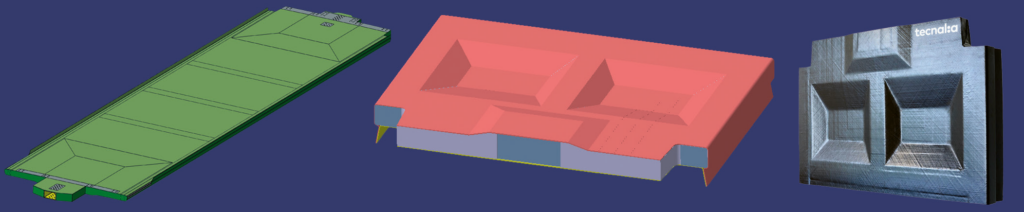
Partendo dal design di un pavimento lungo 13 metri e largo 2,8 metri, è stato progettato un dimostratore in scala semplificato dell’area dell’accoppiatore (1×1,3 m) per convalidare l’integrazione dei profili di pultrusione in una configurazione sandwich con anima in schiuma e per migliorare la laminazione e drappeggiabilità del materiale semipreg in aree con transizioni, come quella di integrazione posteriore del sistema HVAC con l’accoppiatore.
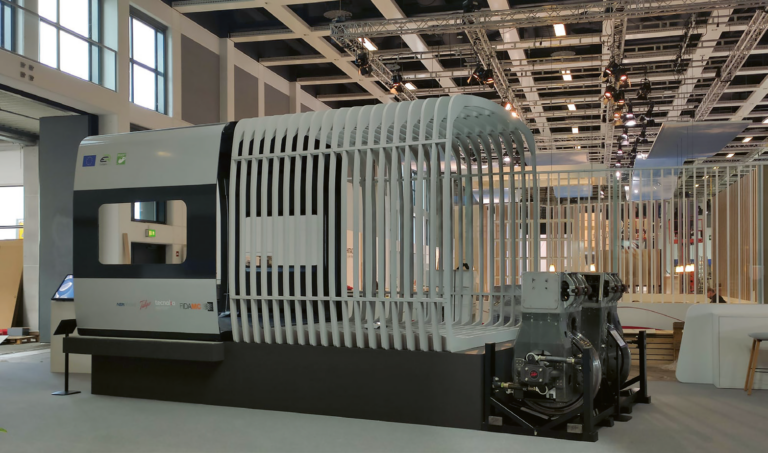
Per costruire il dimostratore è stato realizzato uno stampo in cui, inizialmente, la pelle inferiore è stata laminata con strati di diverso orientamento con un “drop-off”. I profili di pultrusione longitudinale e trasversale sono stati installati sulla pelle inferiore. Con l’aiuto di una pellicola adesiva e di una pasta riempitiva sono stati rifiniti i motivi tagliati dei nuclei di schiuma tra i profili. La pelle superiore del semipreg è stata laminata, cercando di adattare gli strati con orientamenti diversi alle transizioni geometriche che formano l’accoppiatore e gli spazi HVAC. Infine, utilizzando un sacchetto sottovuoto per la compattazione e la polimerizzazione. La parte è stata polimerizzata a 100°C in un forno per 4 ore.
Scale-up e validazione dei test reali
Una volta approvato il processo di fabbricazione, si è deciso di realizzare un dimostratore in scala reale di una sezione completa della carrozzeria di un treno per presentare i risultati del progetto alla fiera INNOTRANS22 di Berlino.
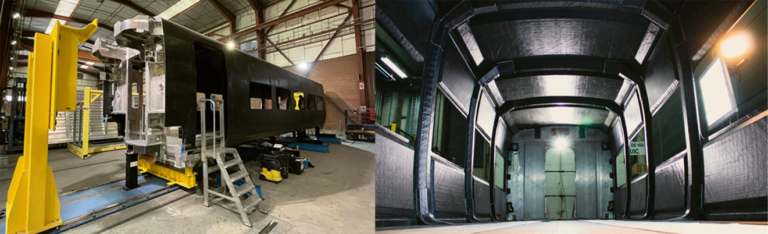
La tecnologia sviluppata è stata replicata nella creazione di un dimostratore in scala 1:1 di una struttura ibrida in materiale composito per una carrozza intermedia di un treno ad alta velocità Talgo, che è stato esposto al JEC World 2023.
Talgo 350 è un treno ad alta velocità che circola in Spagna da 15 anni e la variante Talgo HHR circola in Arabia Saudita da 5 anni. Le dimensioni della carrozzeria sono: lunghezza 12.140 mm x larghezza 2.942 mm x altezza 3.055 mm, passo: 13.140 mm. Ciascuna vettura è divisa in due parti principali che vengono integrate alla fine del processo di assemblaggio: le pareti terminali, realizzate in alluminio e CFRP, e il tubo principale (tetto, pannelli laterali e pavimento/telaio principale), realizzato in materiale monolitico, profili sandwich e pultrusione.
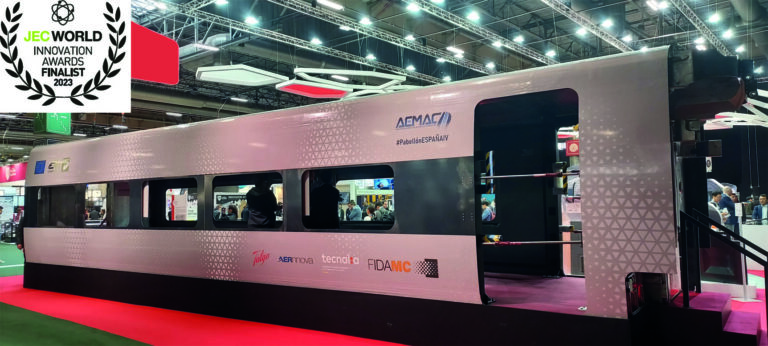
Le tecnologie utilizzate per produrre i componenti compositi si basano sulla stratificazione manuale e semiautomatica di un materiale semi impregnato CFRP conforme agli standard ferroviari FST. Ciò evita l’uso della saldatura su acciaio o alluminio durante la produzione del tubo principale.