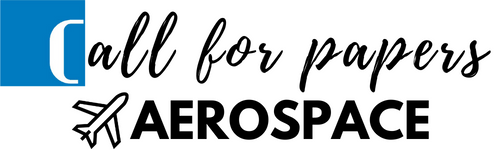
BAE System‘s goal is ambitious: to implement ‘The Factory of the Future‘, a state-of-the-art facility equipped with the latest technologies and production solutions that work seamlessly with the human element, in a completely new way. To realise it, the British aerospace, defence and security giant selected the most innovative technologies for its Samlesbury plant (Lancashire, UK), the ‘Factory of the Future’.
Among the solutions featured in this unique initiative is 3D printing, the use of which is increasingly widespread in manufacturing for the production of prototypes, tooling and final parts with benefits such as reduced costs and lead times compared to traditional methods.
Recently, BAE System added a fourth Stratasys F900 3D printer to complement the F900 series already in use, which will operate 24/7 to help further optimise manufacturing processes in the Factory of the Future.
To date, Stratasys’ industrial-grade FDM additive manufacturing is used to support aircraft ground equipment operations, with a wide range of applications from space models to design verification prototypes, from production to tooling such as jigs and fixtures to end-use parts.
According to BAE Systems, the use of additive manufacturing in these applications brings greater flexibility and speed to production, while also helping to reduce costs. Using the F900 3D printers, the company has seen the significant cost and lead time reductions in the manufacture of production tools compared to traditional manufacturing methods.
The benefits of 3D printing
The ‘Factory of the Future‘ programme aims to drive the future of fighter aircraft production with disruptive technologies. Stratasys’ FDM additive manufacturing plays an important role in this initiative, as it helps achieve the overall goals of reducing costs and time to market. With the total number of Stratasys printers increased from three to four, the 3D printing capacity is significantly increased. This purchase also allows BAE System to take advantage of new materials available for this technology for tooling applications. These include Nylon 12CF FDM carbon fibre, used to make robust yet lightweight repair and development tools for the production line.
According to official BAE Systems sources, this technology allows for the renewal of many traditional manufacturing processes. Other benefits are to
- quickly 3D print unique parts for new products
- replace tooling more easily and economically
- ensure production uptime even when components are delayed.
In the event of supply chain disruptions, the in-house availability of this production capacity allows the company to be more agile and continue to better meet the needs of its customers.
Beyond the Factory of the Future
BAE Systems has also very successfully identified traditional manufacturing applications that can be improved or in some cases replaced with the use of high-performance 3D printing materials. This includes the use of durable ABS and ASA materials for a range of aircraft ground equipment, such as cockpit floor covers for the Typhoon fighter aircraft.
With the new F900, BAE Systems is able to manufacture the thermoplastic covers much faster than versions produced using traditional methods, and they are now much lighter and easier for ground crews to transport, improving the efficiency of maintenance, repair and overhaul procedures. A further advantage is that they can be moulded in red, the colour that marks all components that must be removed before flight.