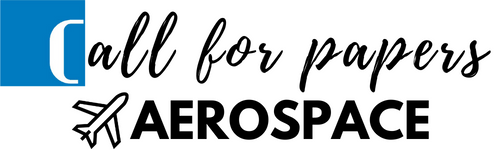
Mario Marchetti – R&D Director – A. Abete S.r.l.
For aeronautical applications of composite materials, the interest is in new alternative production technologies to pre-preg materials produced using autoclave. The RTM technology with all its variants is a valid alternative to OOA (Out Of Autoclave) techniques. This allows the creation of parts in composite material without the aid of an autoclave, by injecting thermosetting resin into a closed mold to impregnate the dry fibers previously deposited in the mold. One of the advantages of this process is the reduced equipment costs and materials costs compared to autoclave technologies. On the other hand, the infusion process can present critical issues related to the non-uniform impregnation that influences the mechanical performance of the component.
The research and development department of A. Abete S.r.l., directed by Ing. Mario Marchetti has been active for some years in research activities to develop an efficient and reliable RTM process for aeronautical applications and in related sectors such as the automotive, rail, and so on. The diffusion of low-cost composite materials in the transport sector allows for a reduction in overall weights, energy consumption, and polluting emissions.
Design
Starting from the CAD model of the RIB designed to be made of aluminum, we proceeded with the design of the equivalent component in composite material. Structural simulation analyzes were conducted to obtain equivalent or superior mechanical performance compared to the metallic element. These simulations allowed the determination of the correct thicknesses and the optimal distribution of the loads. The real loads were simulated and the structural connections for the carbon component were reproduced.
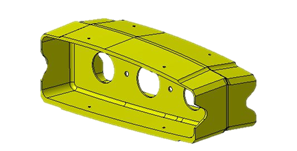
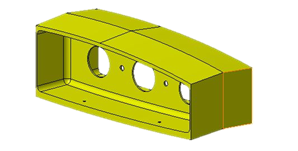
For the design of the mould, specific solutions have been defined depending on the manufacturing process, due to the geometric complexity:
- the wing surfaces of the part
- the preform preparation phases
- the infusion and extraction phases of the component from the mold.
Due to the closing and opening sequence of the mold and the use of solutions designed to facilitate the extraction of the cured part, it was necessary to divide the mold into several components. This required the use of particular solutions for the sealing elements in order to obtain high vacuum levels and high resin injection pressures inside the mold.
The analysis of the resin flows supported the design of the mold in order to have a perfect impregnation of the preform in all its parts to obtain compliance with the required mechanical requirements.
The temperatures of the infusion process are close to 180°C. This imposes particular infusion and “demolding” strategies (extraction of the part from the mold) which allow reducing the effects of the different thermal expansion of the materials compared to carbon fiber.
The mold was also used to make the preforms of the part. Its characteristics are such as facilitating the operator in the dry fiber rolling process. This is important because the fiber, by its nature, has poor “drapability” so it does not adapt well to complex shapes and small bending radii.
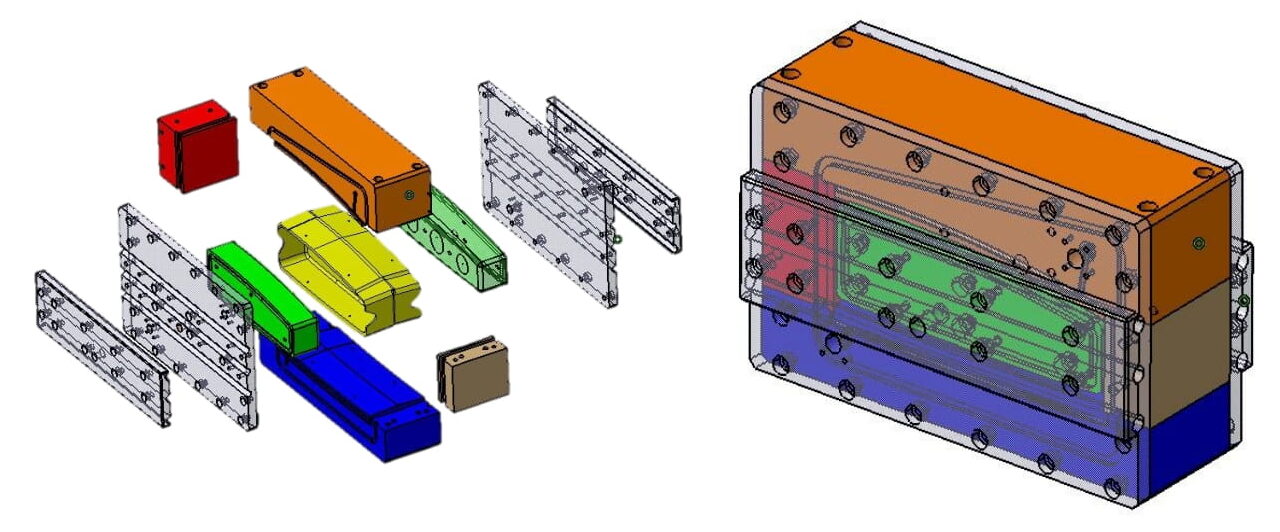
The mold is equipped with an electric heating system necessary to carry out the curing (polymerization) of the resin after the injection phase. The temperature control system allows managing the thermal cycle, which occurs between temperatures of 120°C and 180°C, in an accurate and repeatable way.
Mold manufacturing
Production technologies and experience in mechanical processing of Abete team have made it possible to create a modular mold made up of different elements with extremely precise surface couplings and complex surfaces.
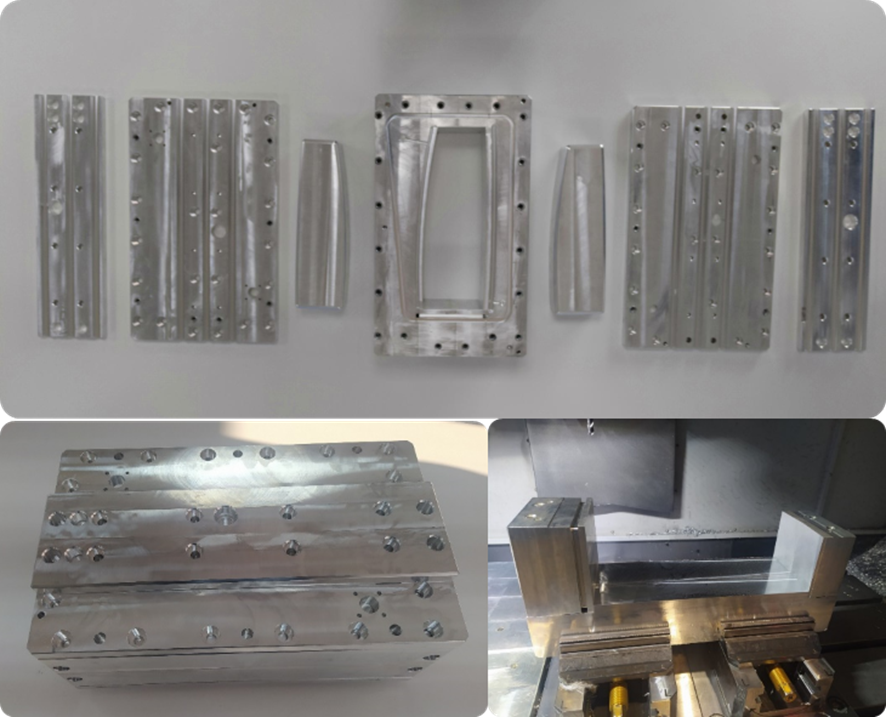
The studies carried out on this application and other projects conducted by the research group, for example on structural C frames in carbon for the fuselage, have allowed the acquisition of knowledge and specific design and construction procedures with effective and innovative solutions for the molds.
Preform making
One of the most important phases of the process is the realization of the preform of composite material. It starts from the cutting of the fabric according to forms established and studied in the design phase. The cut parts are deposited (lamination) on the mold, used as a mandrel, to create the preform for subsequent infusion.

Infusion process and cure
The laboratories dedicated to the preparation of the preforms and the infusion process are equipped with specific equipment and high technological content. The infusion process was performed with a particular system that allows you to automatically manage all phases. The machine has a control system that manages the preheating phases of the resin, its degassing and the verification of the seal of the mold, the injection and the curing phase.
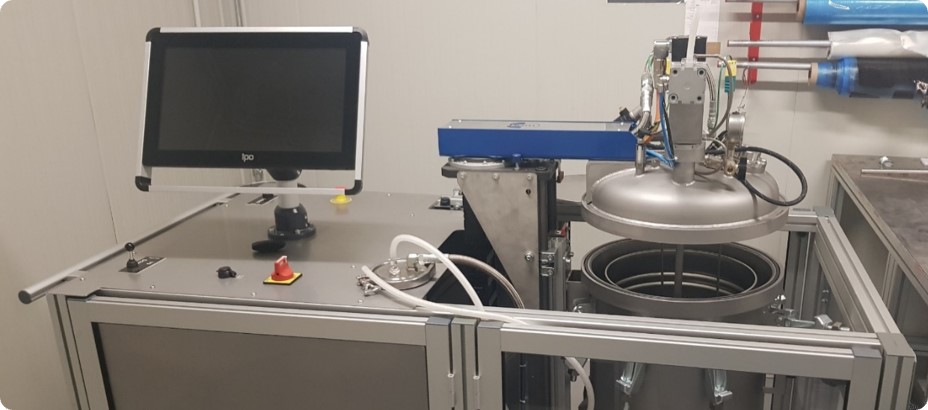
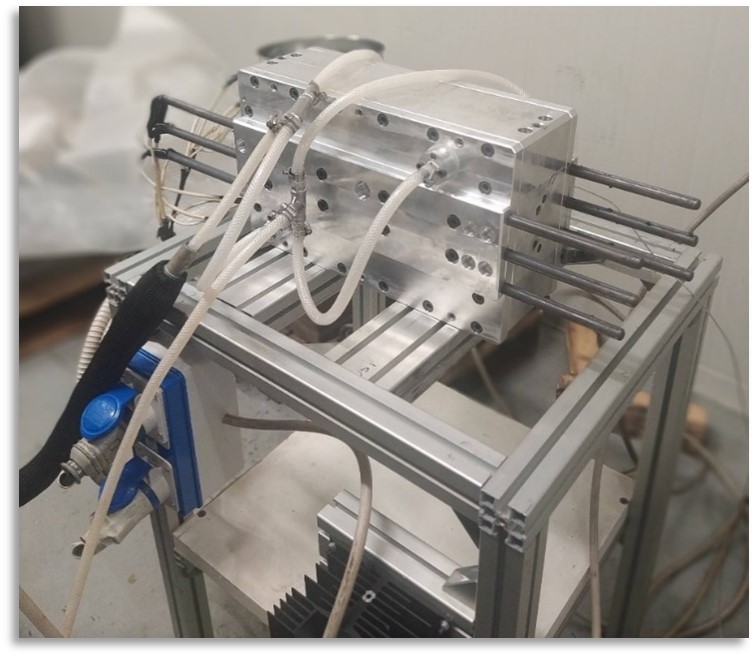
The automation allows to active control the injection process according to resin pressure management strategies such as allowing a correct impregnation of the fibers. The final high-pressure compaction phase eliminates even the smallest cavities within the part. In the final curing phase, in order to have the correct polymerization of the resin, a controlled temperature profile is created according to specifications.
The part, once extracted from the mould, does not require further finishing and trimming phases thanks to the constructive solutions introduced for the realization of the mould.
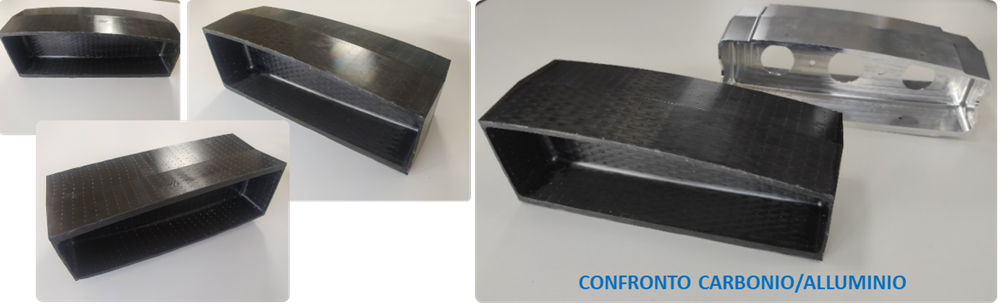
Conclusion
RTM technology is interesting for some aspects related to manufacturing and raw material costs compared to autoclave techniques with prepregs. The ongoing developments on the infusion processes allow obtaining an increasingly performing and repeatable process thanks to the use of automated resin injection systems and the use of innovative solutions in the construction of the molds. It is also possible to obtain very narrow machining tolerances thanks to the use of closed molds.
The activity carried out on the structural RIB for UAVs was an opportunity to develop innovative solutions. We find these above all in the mold, and in the advantages of an automated and controlled injection process thanks to the use of sensors.

It was also possible to carry out a comparative analysis of the production technologies, in metal and in composite, in terms of mechanical and physical characteristics and above all of the production costs:
- improvement of the structural resistance to operating loads of 10%
- weight reduction of 40% compared to the aluminum equivalent
- reduction cost of 20%.
The prototype realization leaves space for further improvements and performance increases.