Researchers and companies in automotive sector constantly try to develop new lightweight components to reduce vehicles weight. Currently, however, cars still have camshaft modules, which are a key component of powertrains, made from aluminum. Now a research team from the Fraunhofer Institute for Chemical Technology ICT, in collaboration with their partners, has succeeded in manufacturing a camshaft module from fiber-reinforced thermoset polymers. This lightweight design element helps lower engine weight and reduces assembly costs. It is currently available as a functional demonstrator.
Camshafts ensure that the charge-cycle valves in internal combustion engines are opened and closed reliably and precisely. These valves are located in the camshaft module, the standard material for which is still aluminum metal. But automotive manufacturers and suppliers are putting great effort into producing powertrains and their components in lightweight design because reduce weight is one of the most effective methods for reducing CO2 emissions. Researchers at Fraunhofer ICT in Pfinztal are supporting the automotive industry in its efforts with a newly developed camshaft module made of thermosetting composite materials. This lightweight camshaft module was realized in cooperation with the MAHLE Group and associated partners Daimler AG, SBHPP/Vyncolit NV and Georges Pernoud. The German Federal Ministry for Economic Affairs and Energy (BMWi) has been funding the project.
The material choice
When it comes to the choice of the right polymer, the project partners opted for high-strength, fiber-reinforced thermoset polymers, as they are well able to withstand high temperatures and mechanical and chemical stresses such as those caused by synthetic motor oils and coolants, for instance. “We contribute the know-how regarding how to design the component geometries to suit the material and the process so that they satisfy all requirements,” says Thomas Sorg, a researcher at Fraunhofer ICT. “The camshaft module is located in the cylinder head, so normally in the upper installation space of the powertrain. Here, it makes particular sense to reduce weight, since doing so also contributes to lowering the vehicle’s center of gravity.”
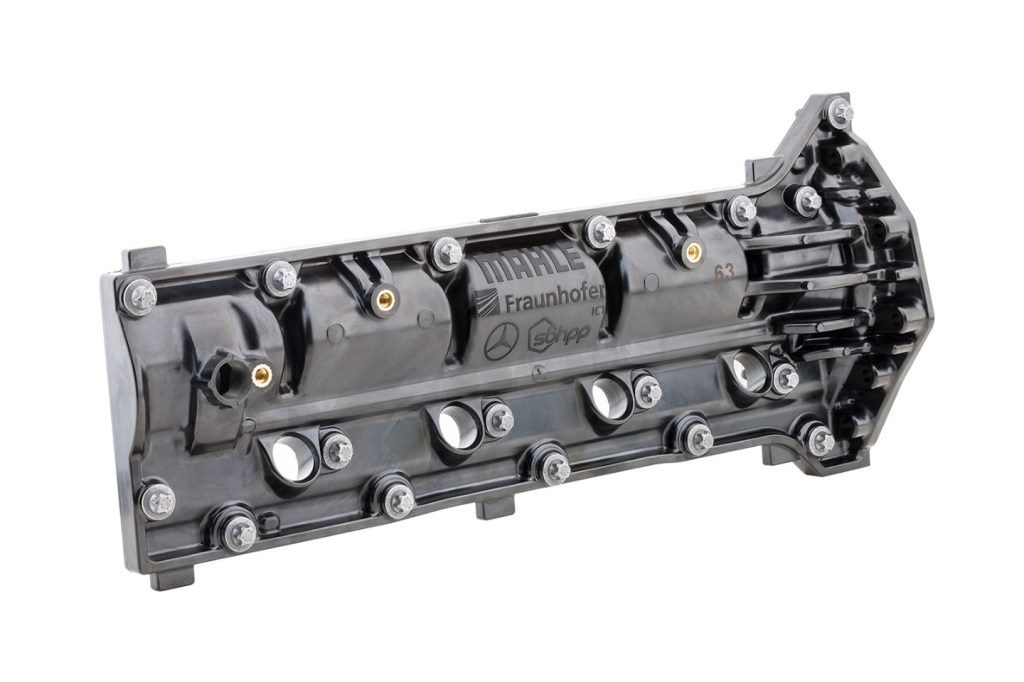
Composite camshaft module: advantages for the companies and for the climate
Castings made from aluminum require extensive reworking after casting, resulting in high costs. Fiber-reinforced thermoset polymers allow a near-net-shape manufacturing, thus requiring comparatively little reworking and which again leads to reduced production cost. Also, at up to 500,000 units, the service life of thermoset polymer injection molds is significantly higher than that of aluminum high-pressure die cast molds. Furthermore, plastics reinforced with a high fiber content have a much CO2 footprint compared with aluminum, since this light metal is very energy-intensive to manufacture.
And there is another advantage: automotive manufacturers are eager to minimize noise emissions. Rattling cars are not only annoying, they are also a clear competitive disadvantage, so noise, vibration and harshness (NVH) characteristics are high up on the list of factors used to assess vehicle quality. Polymers have good damping characteristics.
The camshaft module features a monolithic design with integrated bearings – in other words, it is manufactured in one piece, thus reducing assembly time in the engine manufacturing plant. Car manufacturers receive a pre-assembled module from their supplier and can mount it on the engine with just a few simple mounting operations. This eliminates the need for separate, time-consuming installation of the camshaft. This innovative solution boasts an additional advantage: aluminum inserts in highly stressed areas of the camshaft bearings absorb the direct forces.
600 test hours on the engine test stand
During initial tests on the engine test stand, the researchers observed positive operating performance, and weight savings were demonstrated compared with the aluminum reference part. Simulation calculations help engineers design and validate the prototype before the manufacturing process begins. “Although the stiffness of the thermoset polymer is only a quarter of that of aluminum, design measures enabled us to adhere to the maximum allowable deformation.” After 600 hours of testing on the engine test stand, the lightweight design element demonstrated flawless functionality in a state-of-the-art internal combustion engine. With the aid of the planned fuel injection tests, the project partners want to prove the functionality and the NVH characteristics taking the gas forces of the combustion process into account.
Featured image: The composite camshaft module features a monolithic design with integrated bearings. © Fraunhofer ICT
Source: Fraunhofer ICT